3 Innovations in Robotic Manufacturing that are Changing Automated Assembly
In the dynamic world of manufacturing, robotic technologies are pivotal in shaping the future of automated assembly lines. This blog explores three groundbreaking innovations in robotic manufacturing that revolutionize how products are assembled, enhancing efficiency, precision, and safety.
Table of contents
- What is automated assembly?
- 3 innovations in manufacturing with robotics
- Assembly use cases with 3D vision
What is Automated Assembly?
Automated assembly refers to the process of using machines, robots, and other automated systems to assemble components into finished products with minimal human intervention. This approach is commonly used in manufacturing industries to increase efficiency, reduce labor costs, improve product quality, and enhance consistency in production processes.
Automated assembly is widely used in industries like automotive, electronics, aerospace, and consumer goods, where products are made in high volumes and with precise specifications. It can also be found in smaller-scale manufacturing, where custom automation solutions are designed to meet specific production needs. Overall, assembly application is crucial in modern manufacturing, enabling companies to produce goods more quickly and consistently.
Assembly is one of the most challenging applications to automate with robotics. Most applications may have one operation that demands high accuracy and predictability, namely the picking operation.
Assembly, however, has two very demanding operations: a successful pick of a part at the correct location and a highly accurate assembly operation. In assembly, the success of the first operation will influence the second, and any deviation in the first will compound errors in the second.
Incorporating new technologies and innovative approaches can help to streamline production processes. In recent years, there have been notable advancements in manufacturing automation, particularly in automated assembly.
3 innovations in manufacturing with robotics
Here are three key innovations shaping the future of automation in manufacturing and impacting how we do assembly tasks:
1. Collaborative Robots (Cobots)
Collaborative robots, or cobots, are one of this decade's biggest industrial automation trends. They are designed to work alongside human workers, providing a flexible and safe environment. They are equipped with advanced sensors and safety features that allow them to detect human presence and adjust their movements accordingly.
Cobots are used in automated assembly to assist with repetitive tasks, such as screwing, gluing together, and fastening components. This technology enhances efficiency while maintaining safety, allowing humans and robots to collaborate in shared workspaces.
Universal Robots (UR) is often credited with popularizing the concept of collaborative robots by bringing them to the mainstream industrial market. UR's first cobot, the UR5, was released in 2008 and quickly gained attention for its ability to work safely alongside humans, thanks to its integrated safety features and collaborative design.
2. Machine Learning and Artificial Intelligence Integration
Traditionally, assembly relies on the use of known CAD models of the parts to be assembled. Machine learning (ML) and artificial intelligence (AI) transform robotic assembly by enabling robots to learn from experience and improve their performance over time.
AI-powered robots can analyze large datasets to identify patterns and optimize their assembly processes. This technology allows robots to adapt to changing conditions, such as variations in component sizes or unexpected obstacles. ML and AI integration reduces the need for manual programming and makes automated assembly more flexible and efficient. Using CAD matching, ML, and AI together allows the system to pick parts in unorganized bins.
3. 3D Vision Systems
3D vision systems allow robots to perceive their environment in three dimensions. This technology is used in manufacturing and automated assembly, in particular, to improve accuracy and flexibility.
Watch the on-demand webinar with Inbolt "High-Precision Real-Time Calibration for Assembly":
3D vision allows robots to recognize and locate objects with high precision, enabling them to perform complex tasks like picking parts from random orientations or inspecting assembled components for quality control. This capability reduces errors and increases the reliability of robotic assembly lines, making them more adaptable to various production needs.
Without high-quality 3D vision, the system struggles to handle uncertainty. This makes the multiple-step process of picking and manipulating parts and then assembling them extremely challenging. The robot will fail if the components are not in the expected position or orientation.
However, with advanced 3D vision, the system can adapt in real-time by observing the parts, recognizing their location, and adjusting to their orientation. This ability to adapt reduces the chance of error during assembly.
Automated assembly has unique and challenging demands for robotics. The tasks involve human levels of dexterity where parts must be cingulated and grasped. These fine motor skills are reliant on the performance and quality of the 3D vision system.
High precision is important, but of most importance is a very high degree of dimension trueness, meaning seeing things as they are and where they are.
Zivid 2+ M60 is a perfect example of 3D vision technologies enhancing assembly tasks. The next-generation 3D camera delivers the sharpest, most dense point clouds, with up to 5000 points per sq centimeter and dimension trueness >99.8 %. It effortlessly sees every detail, feature, and flaw for quality inspection and fine dexterity assembly tasks.
Assembly Use Cases with 3D Vision
We have compiled some use cases where companies have solved assembly challenges thanks to 3D vision:
Revolutionizing industrial assembly: InnoPICK transforms parts hanging processes
Hanging parts for processing has been primarily carried out manually, and automating this task has proven to be a real challenge. SIDASA Engineering has designed a new technology to hang pieces on hooks using a 6-axis robot to provide an adaptive solution for small and medium objects. It's a complex bin-picking and assembly application that requires a bit of ingenuity and advanced technology to solve.
Read the use case about SIDASA and Innodura’s solution →
Plaif enables new possibilities in appliance manufacturing with AI and 3D machine vision
Picking complex-shaped, hard-to-manipulate, and highly reflective metals is still challenging for robots due to poor vision. Plaif’s customer was dealing with small brackets used in electronic white goods assembly, some of which were inconsistent in shape.
Read how Plaif solved those challenges in this case study →
In summary, cobots, AI, and 3D vision are the major industrial automation trends revolutionizing manufacturing by increasing efficiency, reducing costs, and improving safety.
By embracing these advancements, companies can stay competitive and meet the demands of modern production. The future of robotic manufacturing holds exciting possibilities, promising even greater innovations in the years to come!
You May Also Like
These Related Stories
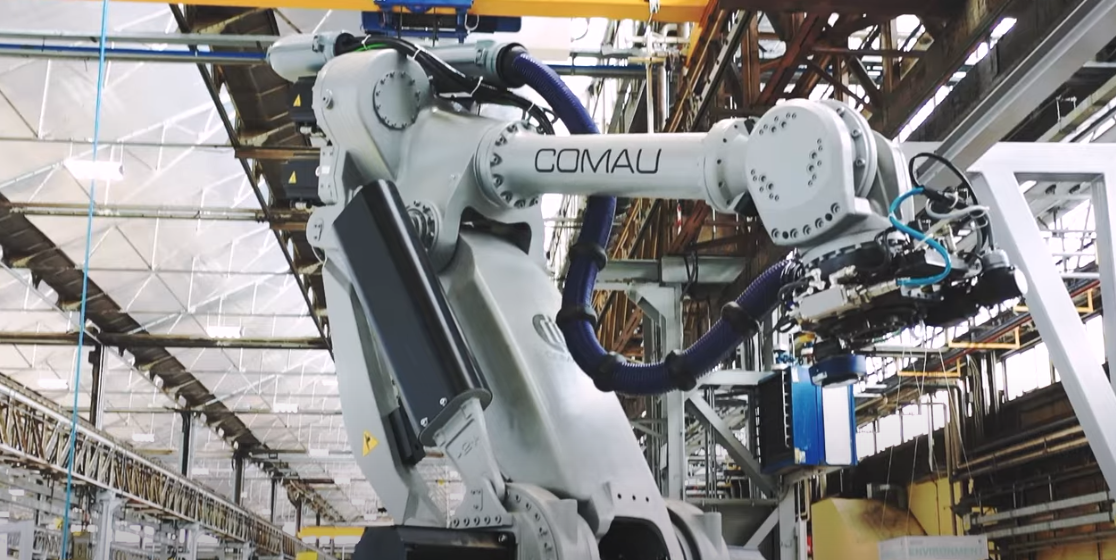
Top Machine Vision Considerations for Disassembly Applications
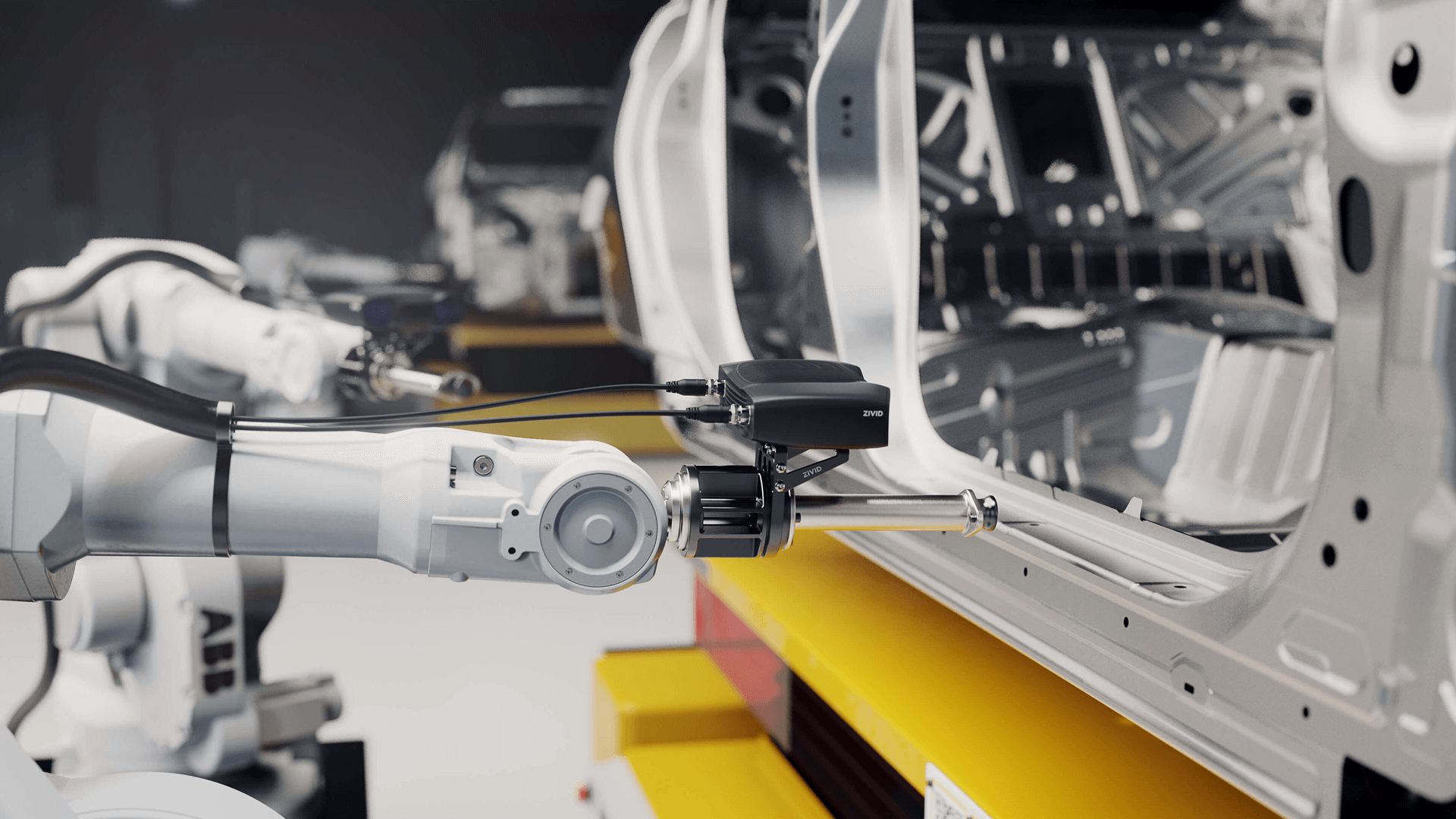
5 Examples of Robot Guidance Applications with 3D Machine Vision
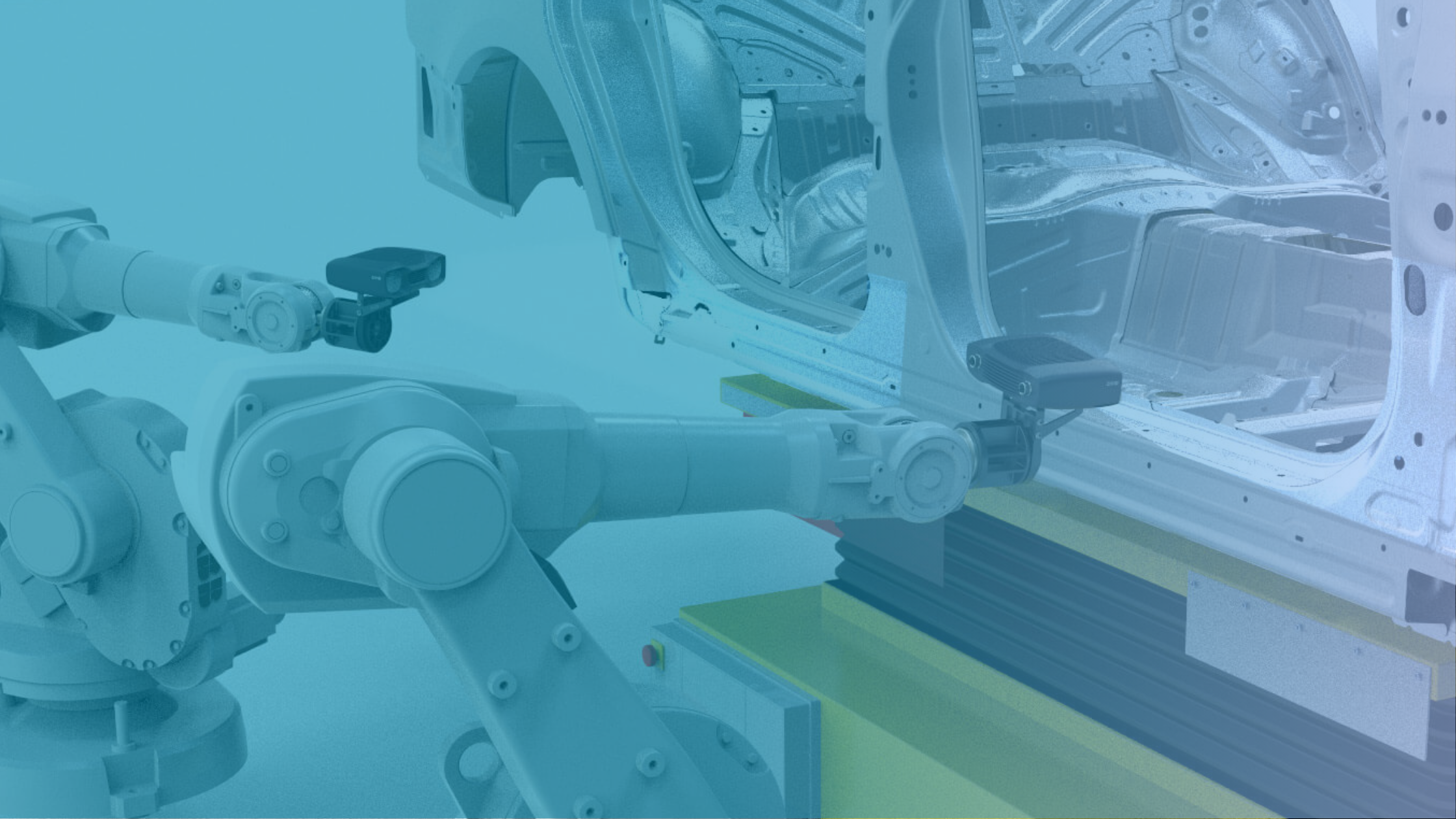