5 Key Machine Vision Features in Robotic Assembly
In manufacturing robotics, automated assembly stands as an application demanding the highest degree of precision, accuracy, and stability.
Table of Contents
- Robotic Assembly Tasks
- Key Machine Vision Features in Assembly
- How Does Zivid Solve Manufacturing Automation Challenges?
While some tasks may allow for a degree of randomness, assembly requires a meticulous approach. Imagine a puzzle where each piece must fit perfectly, and every movement must be calculated with utmost care.
During assembly tasks, robots must understand the exact shape of each component and know precisely how and where to pick it. Moreover, it's not simply about picking and dropping - robots must navigate the placement with pinpoint accuracy.
Automotive assembly scenario
Robotic Assembly Tasks
An assembly robot cell performs a set of repetitive tasks, which vary depending on the industry and the solution. The experience we’ve gathered from our customers, teaches us that the most frequent operations in assembly are the following:
- Bin Picking - identifying and picking individual parts or components from a bin or container. Bin picking is a task found in many manufacturing robotics applications, but assembly bin picking must be more precise, as the gripper must pick the object in a certain way. If the tool or gripper is unable to pick the object accurately out of the bin, customers will often set up a step in-between, a repositioning station.
- Insertion - inserting pins, plugs, connectors, or other components into target holes or fittings ensuring proper alignment and fit.
- Joining - bringing two or more parts together and securing them to form a single assembly. Joining methods may include welding, adhesive bonding, riveting, or mechanical fastening.
- Fastening - applying fasteners such as screws, bolts, nuts, or clips to securely fasten parts together.
Now that we’ve established that automated assembly is challenging, let’s explore what machine vision features can make or break an automated assembly system.
Zivid camera mounted on a robot in a tire assembly scenario
Key Machine Vision Features in Assembly
It takes a village to achieve perfection in robotic assembly, and that village consists of accurate perception, robot coordination and motion. While all three are equally important, let’s focus on the 3D camera features that robots need to successfully execute a task.
1. Field of View (FOV)
FOV (Field of View) refers to the extent of the observable scene captured by a 3D camera. Depending on the task, camera FOV could be too narrow. In this case robots might need to make additional movements and captures to compensate, which reduces efficiency and increases the cycle time of a task.
2. Accuracy
High accuracy is achieved through trueness and precision. Assembly needs utmost precision to be able to recognize and localize small and/or shiny irregularly shaped objects.
High level of trueness is then needed to be able to pick the object in the right way and to insert it to the ‘’end goal’’. If any of these features is lower than perfect, the tasks usually cannot be performed.
Some of our clients that deploy automated assembly systems used to have accuracy challenges that could’ve caused real life implications. Take Vamag’s contactless wheel alignment as an example. High precision is the key to a successful wheel alignment system as proper wheel alignment increases your tire life and road safety.
3. Flexibility
Flexibility in robot-mounting a camera refers to the ability to easily and securely attach the camera to different robotic systems, allowing for versatile deployment in various applications.
Our customers in the automotive industry have encountered the challenge of access and flexibility, as many tasks are performed on ‘’awkward to get places’’. These tasks can be performed by humans, but they saw that is not only uncomfortable, but can also cause injuries.
That is why they wanted to find the right solution – a 3D camera so compact and strategically mounted onto the robot that it can ensure capturing the feature of interest from the right angle.
4. High Quality Point Clouds of Challenging Objects
Point cloud quality is crucial for robotics as it ensures accurate representation of the environment, making navigation and object recognition possible.
An example of challenging objects in manufacturing
Objects in the assembly environment may vary in shape, size, and surface characteristics, such as reflectivity or texture, making it challenging for machine vision systems to accurately detect and classify them, especially when dealing with shiny or irregularly shaped objects.
5. Environmental Robustness
Environmental robustness in 3D cameras refers to their ability to maintain reliable performance in various environmental conditions, such as changes in lighting, temperature, or humidity, ensuring consistent and accurate operation in diverse settings.
Changes in lighting conditions, ambient temperature, dust, or vibrations within the assembly environment can affect the quality and reliability of images captured by machine vision systems, leading to errors in object detection and recognition.
How Does Zivid Solve Manufacturing Automation Challenges?
The future of automation in manufacturing is about harnessing the power of advanced technologies like Zivid's 3D vision systems to unlock new levels of productivity, flexibility, and reliability in assembly processes. Let’s see how Zivid responds to the challenges of automated assembly.
1. Wide Field of View with 5mPx
With Zivid's wide FOV, robots can approach the scene at the optimal distance, maximizing accuracy and precision. Take, for example, the car battery assembly, where numerous screws need to be inserted.
Knowing that a wide FOV could imply low spatial resolution, Zivid develops cameras that have almost 60 degrees opening angle and 5Mpx – allowing robots to image the entire scene in high resolution.
Additionally, Zivid’s Region of Interest filter allows you to focus on one part of the scene per capture, which makes for very fast imaging.
2. High Level of Accuracy
Zivid point cloud capturing shiny metal objects with <0.2% trueness error
Zivid boasts 3D dimension trueness error of less than 0.2% for the Zivid 2+ M60 and less than 0.4% for the L110, ensuring sub-mm workpiece positioning to meet the stringent demands of assembly tasks.
Zivid cameras are engineered and crafted as industrial-grade technology, undergoing rigorous dimension trueness tests in real-world conditions rather than controlled lab environments.
This ensures that the high accuracy of Zivid cameras isn't just limited to ideal conditions but extends to every environment, guaranteeing reliable performance in any setting.
3. Compact and Easily Mounted
Zivid cameras are small, compact and designed to be mounted onto the robot. Mounting a 3D camera onto a robot enables them to explore multiple scenes within their working area with ease and precision.
4. Patented 3D Technology for Capturing Challenging Object
The manufacturing industry presents some of the most challenging objects to capture in 3D, characterized by their small size, shiny surfaces, and irregular shapes.
Zivid 3D cameras have been developed to produce quality point clouds with high coverage, low distortion, low noise, and high resilience specifically with assembly application in mind. We use:
- Stripe Engine
- HDR (patented)
- Filters (Reflection Cluster. Contrast distortion)
5. Industry Grade 3d Vision Technology
Every Zivid 3D camera undergoes over 100 hours of performance, reliability, and calibration tests to ensure industry-grade quality and accuracy.
Zivid's 3D hand-eye calibration simplifies the coordination camera and robot connection process, delivering 10x better results compared to comparable calibration methods, and ensuring optimal performance in real-world assembly environments.
Conclusion
To put it shortly, if you are deploying an automated assembly system, you want a 3D camera that has a wide field of view and allows you to position it close to the scene, while providing a high level of accuracy and quality in point clouds.
You want to be able to capture details of shiny, small, irregular objects with high resolution. And you want a camera that is compact, easily mounted to the robot, and has industry-grade robustness.
Basically, you want Zivid 2+ M60, which has a dimension trueness error smaller than 0.2% and 570x460 mm2 FOV at a focal distance of 600 mm. If you need even wider FOV, opt for Zivid 2+ L110, which has a dimension trueness error <0.4% and 1090x850 mm2 FOV at a focal distance of 1100 mm.
Both cameras use Zivid’s Vision Engine & HDR to power their captures, and paired with good robots can achieve sub-mm workpiece positioning accuracy.
If you are interested in hearing more about Zivid's machine vision technology and approach, book a demo!
You May Also Like
These Related Stories
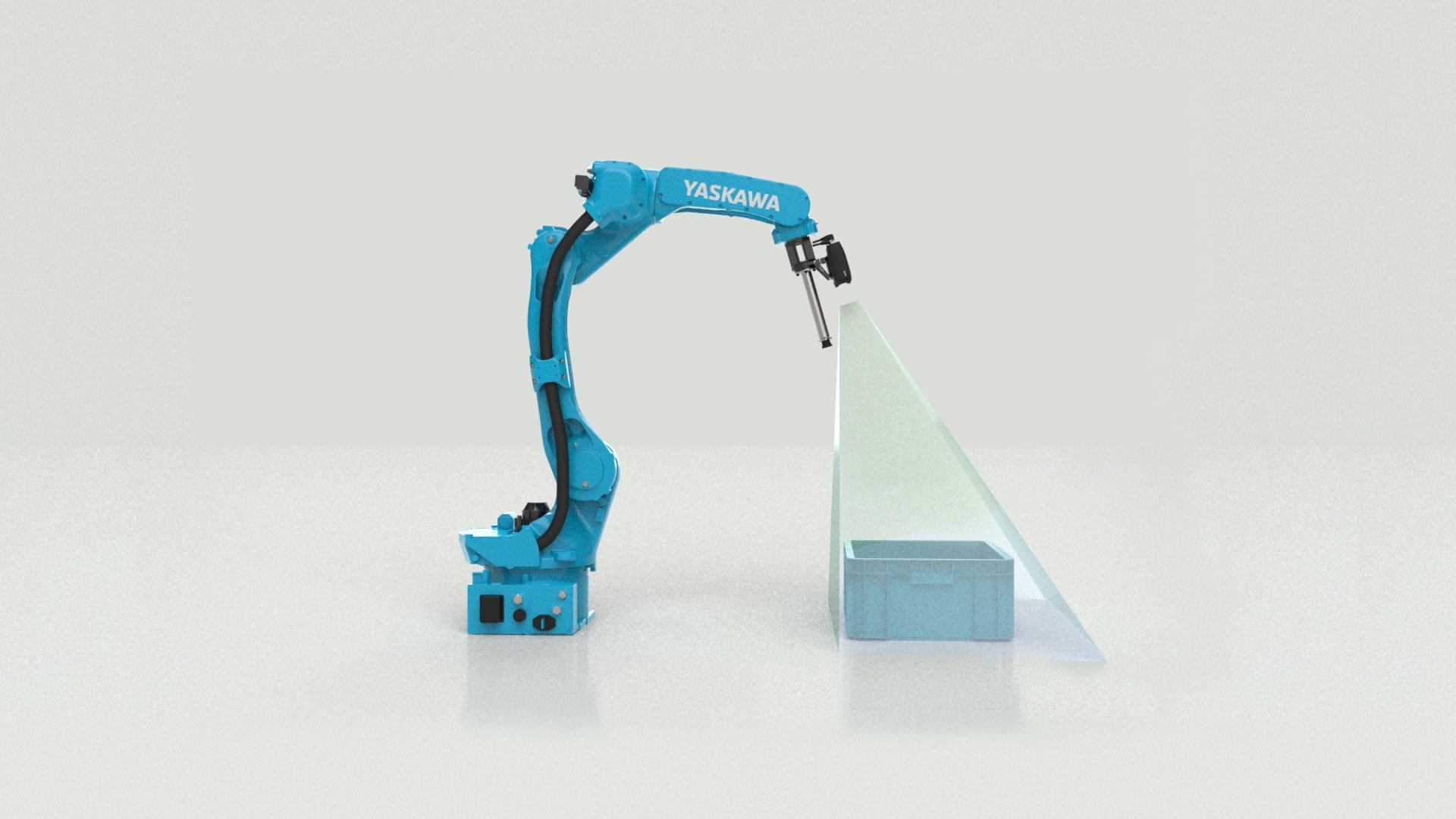
The best way to mount your 3D machine vision sensor
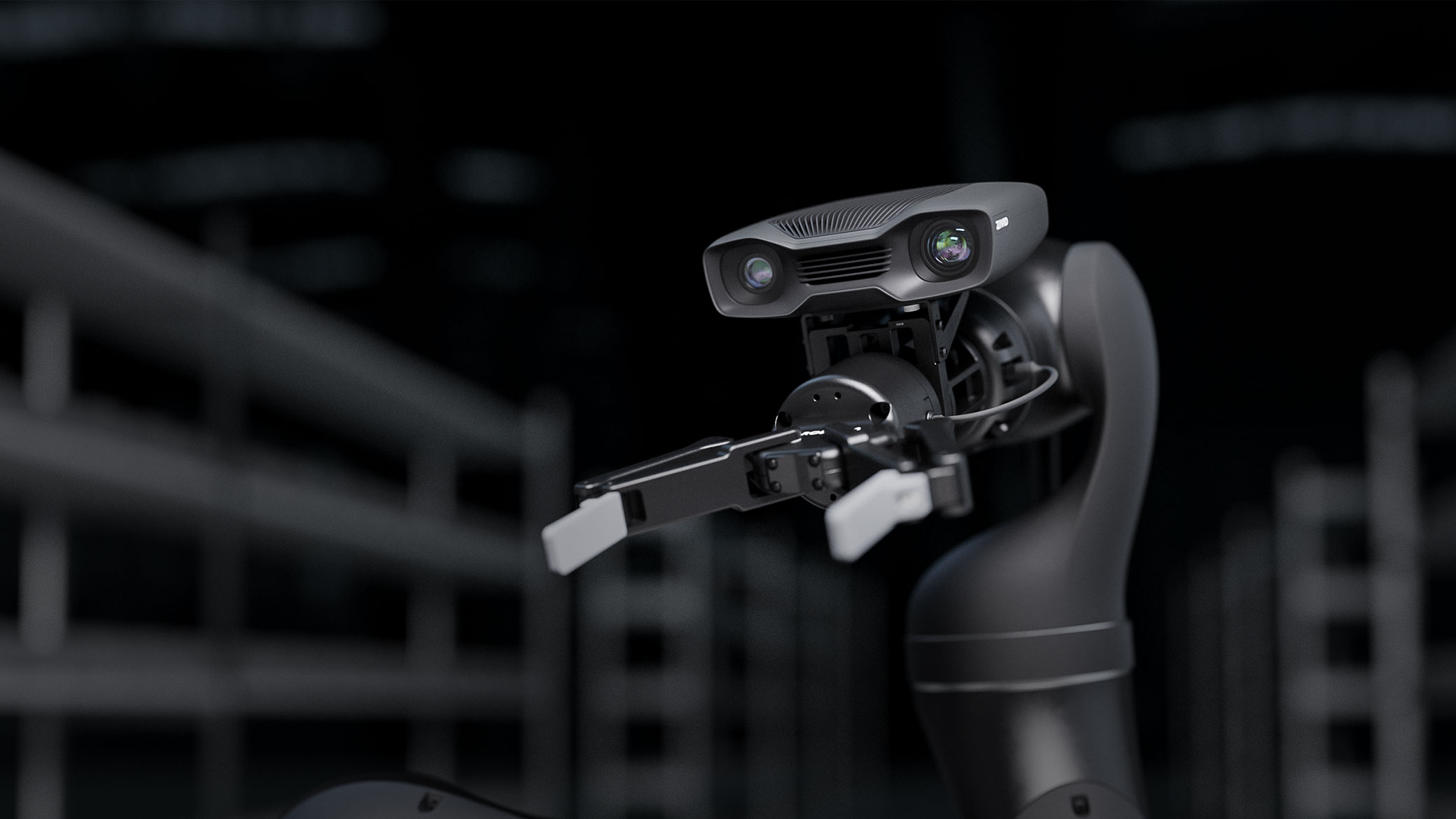
The Advantages of 3D Sensors in Robotic Machine Tending
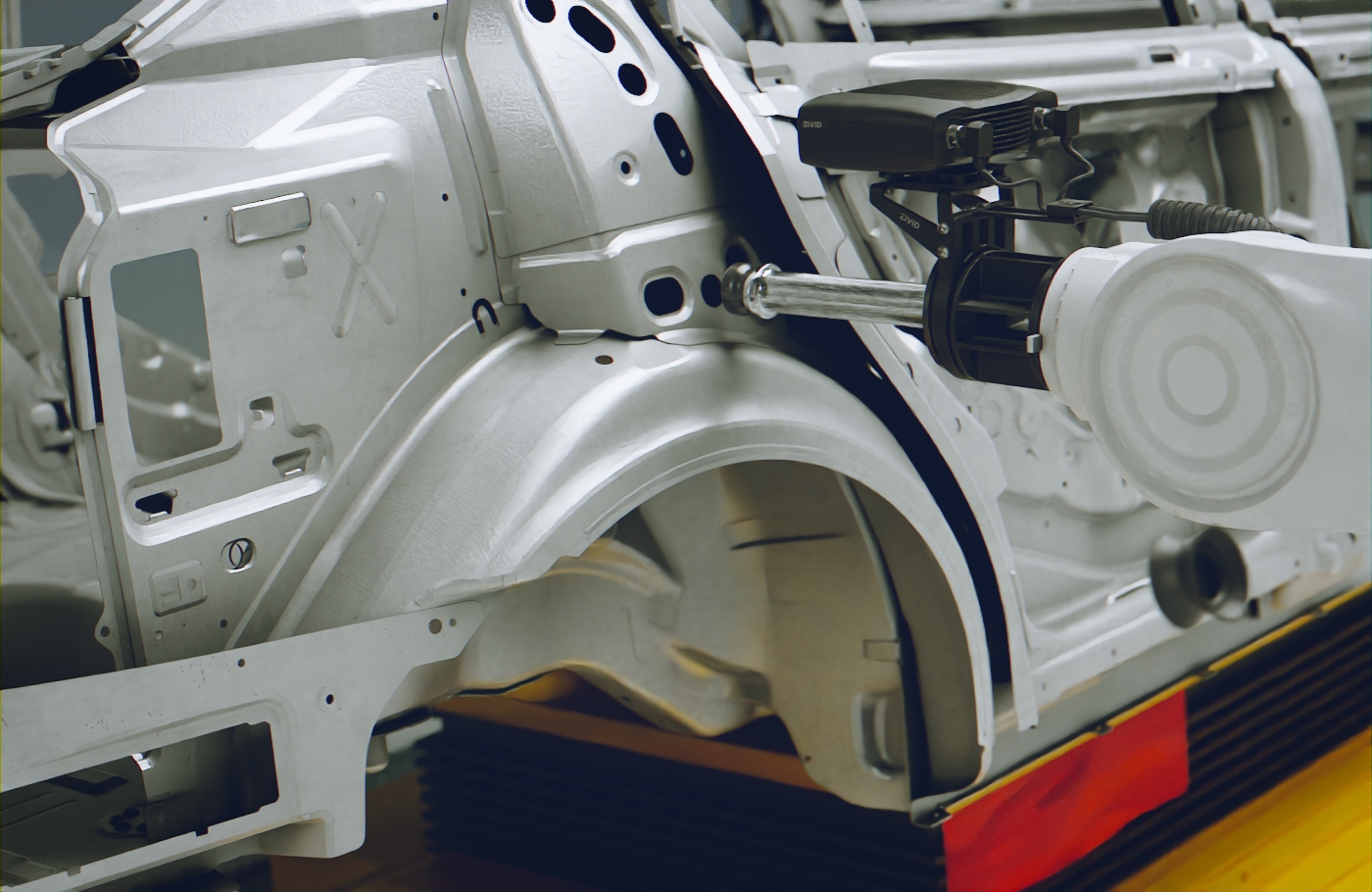