Top Machine Vision Considerations for Disassembly Applications
Disassembly is not the most common application that arises in robotic automation conversations, but it is nevertheless an important element of some manufacturing operations. It has many of the same demands of assembly, but some subtle differences should be considered. In this blog, we will look at these with a special focus on the 3D machine vision aspects.
Table of contents
- Who Disassembles?
- Recycling is top of the agenda
- Different demands for assembly
- Adaptability and performance
- 3D machine vision considerations
Trueness
High Dynamic Range (HDR)
3D and 2D in a single camera
Calibration and reliability - Summary
Who Disassembles?
When we think of manufacturing it is intuitive to think of building things up in stages towards a final finished product. But within the world of building things, it is also necessary to ‘un-build things. This can be for several reasons including:
- Recycling of items and materials
- Removal of hazardous items and materials
- Maintenance and repair
- Quality control and inspection
- Redesign and retrofitting
Recycling is Top of the Agenda
While all the above automated disassembly processes have important roles to play, recycling is probably the most critical, and economically beneficial currently.
The recycling and reuse of battery components is a major concern. Batteries are ubiquitous now and many of them contain rare earth metals. It is estimated that > 95% of most materials have some possibility for recycling. The cost savings are profound. Cobalt, a metal used extensively in electronics requires the heavy mining of 400 tons of ore to produce 1 ton of cobalt. The energy consumed along the process line is considerable. Aside from the ecological benefits, there are clear economic advantages. In 2021 Apple saved $120 million through recovery and recycling with their dedicated disassembly robot ‘Daisy’.
Different Demands for Assembly
While disassembly might appear the same as assembly, only in reverse, this is often not the case. In assembly, all parts are typically brand new or have at least been through an inspection and quality control process before being accepted. In disassembly, the products are often in an unknown condition or level of damage. This unpredictability is a key driver in many industries for the adoption of high-quality machine vision. The use of a 3D camera enables a system that can adapt to each new situation and still perform the task as intended.
Apple’s disassembly robot ‘Daisy’
Adaptability and Performance
Because there is inherent entropy related to disassembly applications given the unknown state and condition of the parts to be disassembled, the robot cell must not only be performant, but it must also be adaptable. A high-quality vision system will allow the robot to make better choices because it has more, higher-quality data. What it also enables are flexible disassembly stations that can work on a variety of different tasks.
3D Machine Vision Considerations
Trueness
Learn more about trueness, precision and accuracy →
The next time you unscrew a bottle top, just think about the complexity of that task that your brain and motor functions are handling. It seems so straightforward, but it is demanding in ways we take for granted. The human vision system and brain are exceptionally good at judging size, distance, orientation, and shape. For a robot to do something approaching this, it needs a similar capability in terms of judging ‘what something really looks like, and where it really is’.
For the ‘where it really is’ part of this requirement what is required in a 3D machine vision system is very good trueness. A high-quality 3D camera must deliver excellent trueness; dimensionally, rotationally, and positionally. Disassembly tasks are so demanding that anything below 99.5% trueness will struggle to be effective.
Point cloud trueness comparison.
The red point cloud has poor trueness and possible manipulation problems.
Pain point
Disassembly involves very precise orientation of grippers, end tools, and parts to be disassembled. If trueness is not exceptional parts will be damaged and the robot cell will likely have to stop.
Cure
A 3D camera with exceptionally high trueness will enable a reliable disassembly system with very accurate and precise manipulation necessary. Zivid 3D cameras typically have a trueness value of 99.7%, or better.
High Dynamic Range (HDR)
Many of the parts that need to be disassembled are metallic and often very shiny. This leads to very high contrast in the scenes. Again, human vision systems have superb dynamic range, in the region of 80dB. If a 3D camera does not have HDR it will have to choose between exposing for the highlights, or the lowlights in the scene. This leads to incomplete point clouds with missing data.
An example of HDR with complete point cloud coverage (left), and limited dynamic range with missing point data (right).
Pain point
Incomplete point clouds with insufficient data do not allow the robot to see the object in its entirety. This leads to an inability to manipulate the object successfully.
Cure
Human eyes have approximately 80dB of dynamic range, and Zivid 2+ 3D cameras have as much as 120dB and 80dB in a single acquisition.
3D and 2D in a single camera
We mentioned that the human vision system is exceptional at detecting an object's shape, and where it is positioned. The 2D aspect of a machine vision system carries out the detection part of this capability. High resolution with low noise and low distortion is essential here so that the robot can successfully match what it is looking at with a CAD model of the same item. If the 2D is noisy and distorted this will be problematic. Often a separate, additional camera is used for the 2D only. This is an additional cost and involves challenging matching of the 2D pixel data with the point cloud from the 3D camera.
3D camera with integrated and coherent 2D data (left), separate 2D and 3D camera (right).
Pain point
Insufficient 2D image quality, and difficult, challenging integration between separate 2D and 3D camera systems.
Cure
Ideally, the 3D camera selected will have high-quality, high-resolution 2D in the same product. The Zivid 3D cameras have 3D and 2D unified. This means all 3D data points are correlated directly to the 2D pixels. There is no need for external or internal intrinsics. This allows much simpler and intuitive data manipulation by other systems in the robot cell.
Calibration reliability
3D cameras and sensors are extremely sensitive, laboratory-grade machines. However, they are typically deployed in environments not remotely as controlled as a laboratories, manufacturing plants, warehouses, welding shops, etc. This means temperature fluctuation, dust and particles, and vibration can often be present. The calibration stability of the 3D is what will ultimately determine its trueness and accuracy. Once the calibration begins to drift, it will become less and less accurate and at some point, will be unable to manipulate the parts for disassembly.
Pain point
As the 3D camera’s calibration drifts due to external influences (temperature, vibration, shock) the robot cell’s ability to perform the task is degraded. At some point without a re-calibration, the robot cell will no longer be able to perform its task and will stop.
Cure
All 3D cameras will need re-calibration at some point. What is important is that they remain in calibration for a significant length of time. Zivid 3D cameras are factory-calibrated across the entire working volume before shipment. They also have a sophisticated internal floating calibration system that keeps the camera within calibration limits as temperature changes occur.
Summary
Disassembly applications have many similar requirements as assembly tasks. But there are subtle differences, and, in some areas, it is even more challenging. They are both at the high end when discussing the most challenging automation tasks. Because of the variation in the condition of the parts to be disassembled very high-quality 3D cameras are essential.
You May Also Like
These Related Stories
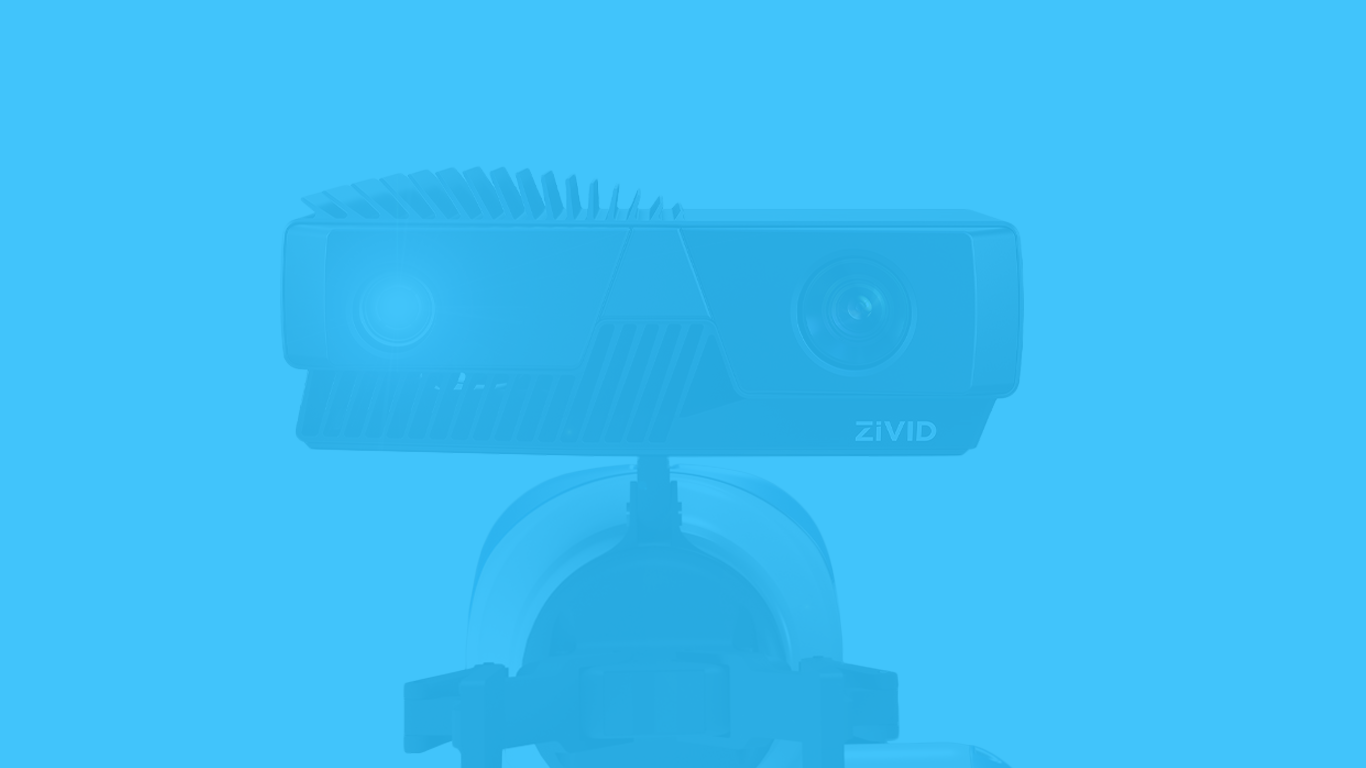
A beginner's guide to 3D machine vision cameras
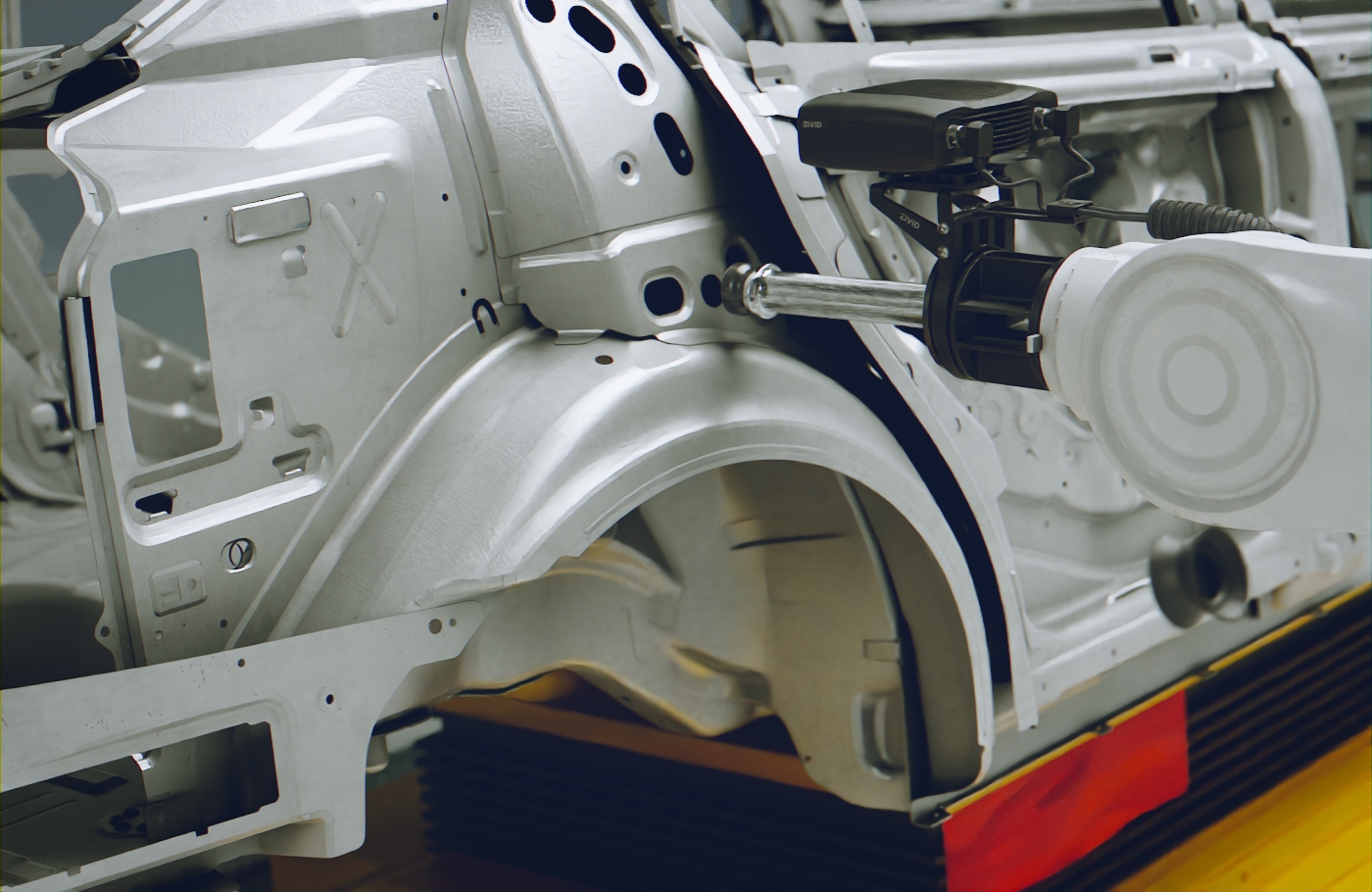
3 Innovations in Robotic Manufacturing that are Changing Automated Assembly
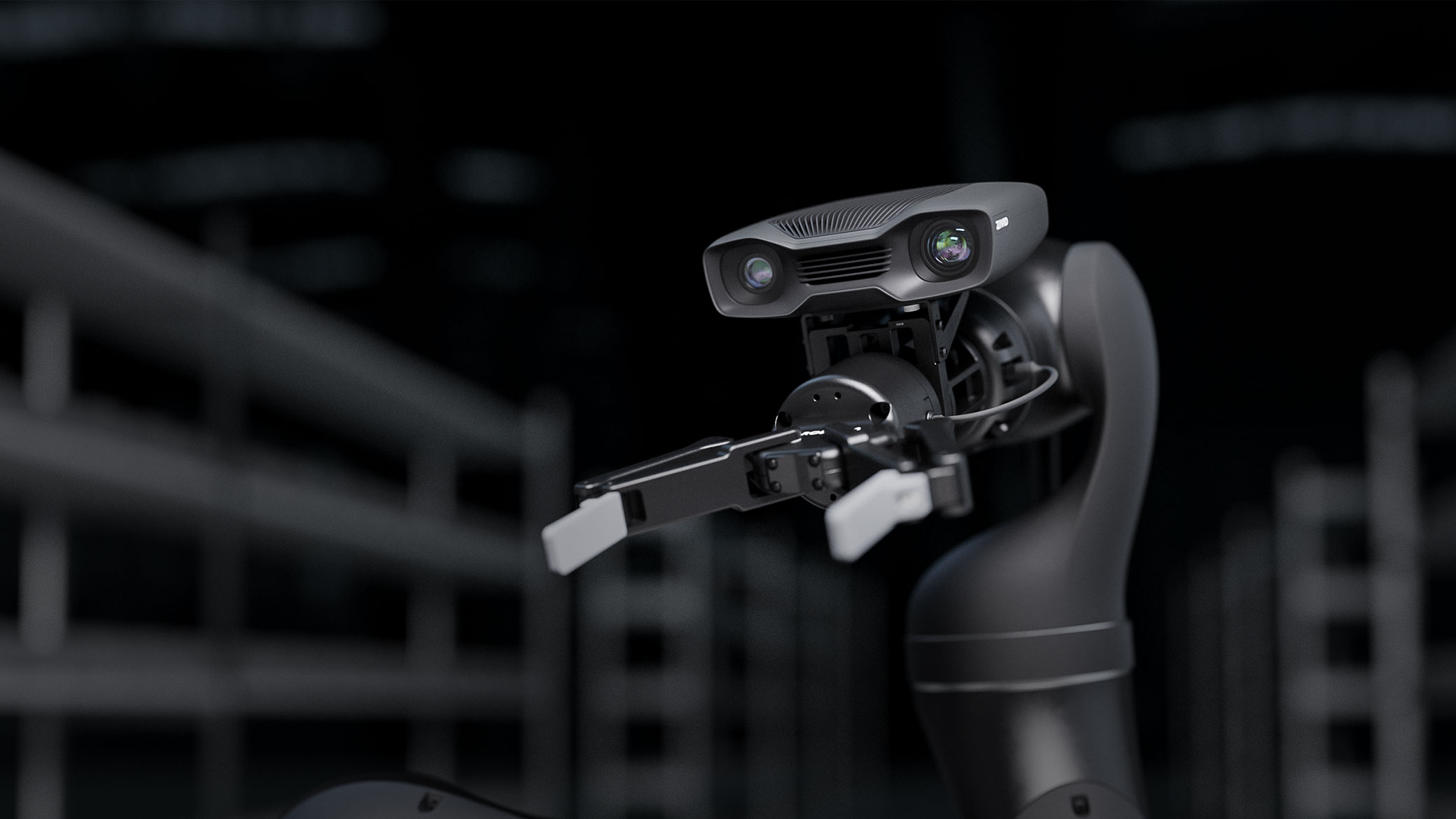