Cost Factors for Machine Vision in Automated Assembly
As companies strive to stay competitive in Industry 4.0, automation in manufacturing gains attention for its cost reductions and consistent production quality. Applications such as inspection, bin picking, and machine tending have seen widespread adoption of robotics and machine vision, becoming standard practices.
However, automating assembly has been particularly challenging due to its lack of forgiveness for error. Historically, the lack of high-quality robotic arms and industrial machine vision made cost-effective assembly automation difficult. High initial investments and frequent unplanned maintenance costs deterred its viability, as machine vision systems were not designed for industrial environments.
Table of Contents
- The Role of Machine Vision in Automated Assembly
- 3D Camera Cost Considerations
- Zivid’s Solution for Decreasing Regular Maintenance Costs
- Zivid 3D Camera Was Developed with Assembly in Mind
Nowadays, it is more than viable to automate your assembly process. However, to achieve optimal performance, it is crucial to invest in high-quality components for each part of the automation cell. In this article, we are talking about factors you should consider while choosing 3D machine vision solution for your automation cell.
The Role of Machine Vision in Automated Assembly
Machine vision enables the detection and determination of the position of workpieces, which allows for real-time adjustments and adaptations to production changes. By integrating machine vision, manufacturers can achieve greater flexibility, reduce errors, and streamline their operations.
Automated assembly using Zivid 2+ M60
Because machine vision reduces production errors, it is crucial to look beyond the initial price of a single 3D camera when adopting automated assembly solutions. It is imperative to consider the total cost of ownership (TCO) and cost savings accrued through minimized production stoppage.
3D Camera Cost Considerations
The latest industrial 3D cameras are becoming more affordable, or rather, quick to pay for themselves through productivity gains. The productivity of an automated assembly cell depends on the machine vision quality, precision, and industrial durability.
Therefore, the accessibility of one 3D camera shouldn’t be at the top of the mind when deciding on a machine vision solution. While the cost differential between low-end and high-end sensors might be several thousand dollars, this is a fraction of the overall robot cell cost. Additionally, just a handful of robot cell stoppages can quickly account for this difference in cost.
Development Phase Costs
During the development phase, the ease of working with the 3D camera's software development kit (SDK) and graphical user interface (GUI) is very important. A user-friendly SDK and GUI can significantly reduce development time, leading to lower labor costs.
Zivid Studio user interface
Ask yourself: Is the SDK intuitive and well-documented? How many man-hours will be required to train personnel to use and program the camera effectively?
Integration Phase Costs
The integration phase presents its own set of cost considerations. A key factor is the camera's adaptability within the existing system. An adaptable camera that reduces the complexity of the overall system can lower both initial integration costs and ongoing maintenance expenses.
Additionally, one good camera can replace some of the components and simplifying the setup can lower overall hardware and maintenance costs of the cell. For example, a 3D camera with an integrated light source does not need any external lighting equipment - meaning that you might save up to $4,000 on light domes alone.
Ask yourself: Can the 3D camera easily integrate with existing components, or will extensive modifications be needed? Can the new camera reduce the need for other components in the cell, such as light domes or additional cameras?
Maintenance Costs
Maintenance costs encompass both planned and unplanned activities. Stopping the production cell for 3D camera maintenance is costly, so minimizing downtime is crucial.
Regular calibration is essential, especially for cameras operating in environments with significant vibration – which most assembly cells are. Investing in a camera with calibration tools that enable quick adjustments is cost-effective over time.
Unplanned maintenance is always unwanted and problematic. A few unplanned stoppages can escalate lost production costs rapidly, and even a relatively small number of unplanned stoppages can amount to the cost of a high-quality 3D camera. A true industrial-grade 3D camera will maintain a high calibration state for a longer time and in more demanding operating environments.
Zivid cameras go though different set of tests, this one is the drop test.
Cameras selected based on low price rather than reliability can be more prone to failures and calibration drift, leading to unplanned maintenance. This can significantly disrupt production and increase costs.
Zivid’s Solution for Decreasing Regular Maintenance Costs
Our cameras stay highly calibrated even in rapidly changing thermal environments. Zivid's unique floating calibration system ensures your 3D performance is always spot on.
However, like most high-precision electronic instruments, they sometimes need a little adjustment to ensure their best performance.
Zivid 3D cameras go through thermal stability tests.
Infield correction is a maintenance tool designed to verify and correct the dimension trueness of Zivid cameras. The user can check the dimension trueness of the point cloud at different points in the field of view (FOV) and determine if it is acceptable for their application.
If the verification shows the camera is not sufficiently accurate for the application, then a correction can be performed to increase the dimension trueness of the point cloud. The average dimension trueness error from multiple measurements is expected to be close to zero (<0.1%).
Zivid Industrial 3D Camera Was Developed with Assembly in Mind
Zivid 2+ M60, as a robot-mounted 3D color camera, is inherently ideal for robot-guided assembly applications. Built to true industrial quality standards to survive in the toughest conditions, it delivers consistently high-quality 3D point clouds offering detail at 80 µm point precision and true-to-life form and representation with < 0.2% dimensional trueness error.
Besides that, our infield correction tool makes regular maintenance easy and cost-effective, our support team and Knowledge Base make integration fast and easy, and we develop our Zivid studio to be the most user-friendly GUI in the industry.
You May Also Like
These Related Stories
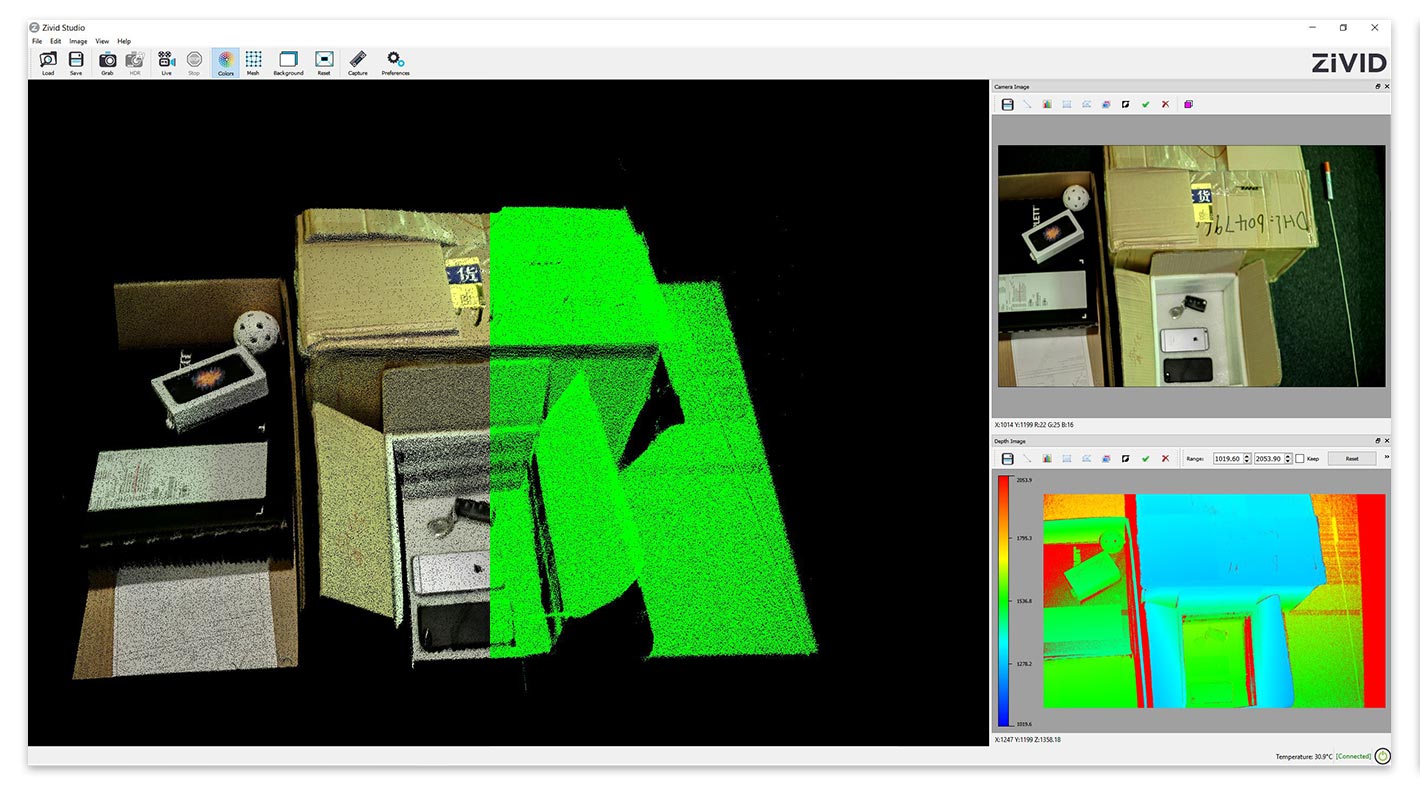
Peering into the world of 3D vision
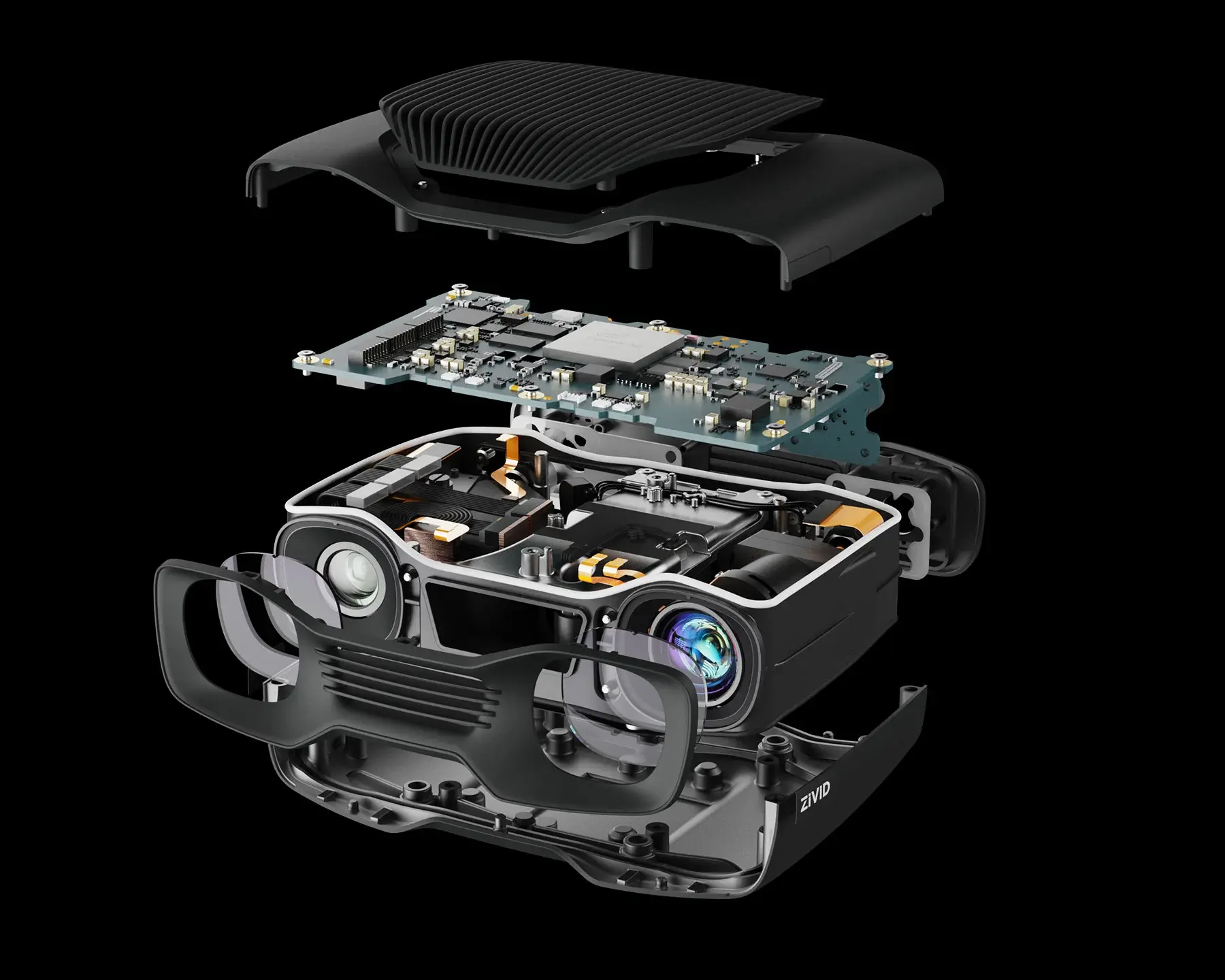
Reliability in Harsh Conditions: Insights from Zivid's Quality Experts
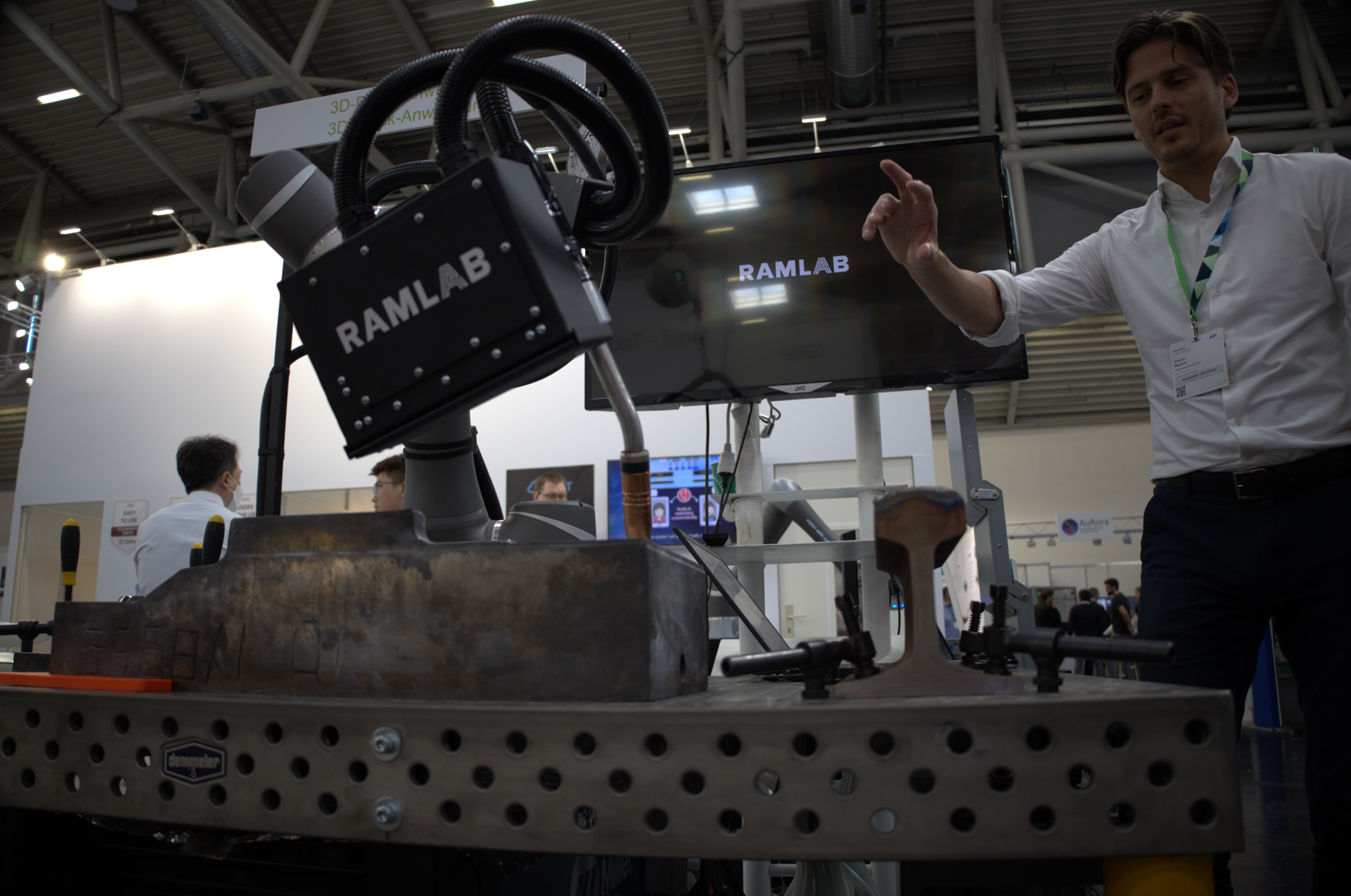