Reliability in Harsh Conditions: Insights from Zivid's Quality Experts
Reliability is a cornerstone of Zivid's philosophy. Ensuring our products perform consistently, even under the harshest conditions, requires a meticulous approach to quality, testing, and supplier selection.
Table of Contents
- Choosing the Right Suppliers
- Reliability Through Rigorous Testing
- Proprietary Calibration Process
- Proving Reliability
- First Choice for Robotic Cells with High Vibrations
What does it mean for a 3D camera to be reliable? It means that it consistently delivers the promised quality and accuracy of point clouds in all industrial scenarios, not just in a lab.
We sat down with our quality experts - Tor Magnus Briskodden, Production Test Lead, and Sindre Engebakken, Quality Manager, to delve into the rigorous processes Zivid employs to maintain its reputation for reliability.
Choosing the Right Suppliers
Selecting suppliers is a sport in itself, and we're fortunate to have a dedicated and solid supply chain (SC) team that works closely with our Engineering and Quality departments.
This collaboration starts when we identify the need for a supplier in product development and continues through sustaining and continuous improvement. Sindre explains:
By having this close cross-functional collaboration, we capture the technical, procedural, and commercial aspects of a supplier. Becoming a supplier to Zivid means demonstrating that product quality is maintained through prototyping and volume over time."
Our rigorous selection process includes due diligence, ensuring suppliers meet our high standards. Testing starts early in the prototyping phase, with verification processes implemented to ensure consistent quality throughout production.
Reliability Through Rigorous Testing
Reliability at Zivid is achieved through qualification tests, production tests, and maintenance. Sindre highlights the importance of beginning this process at the product development stage:
By having well-implemented processes for Design for X (X being manufacturing, testing, or service), Failure Mode, and Effect Analysis, we set the stage for a reliable product. We then prove the reliability of the design through rigorous qualification and First Article Inspections."
Our qualification tests include industry-standard assessments for external factors such as IP Rating (dust and humidity protection) and vibration/shock/drop tests. These tests ensure our products can withstand harsh environments.
This philosophy extends throughout our supply chain, with detailed inspections and tests integrated into our support systems. Tor Magnus explains how the whole team lives by this philosophy:
Printed Circuit Board Assembly (PCBA) test is close to the SMT line (Solder Mount Technology), and sample-based X-ray inspection and automated optical inspection are amongst other things."
Our Production Test Suite is a subset of our qualification tests, ensuring defects are caught early. This includes tests at the PCBA level, final assembly tests, post-calibration tests, and final deployment tests. Zivid's support system for assembly, test and inspection consists of several main components covering preventive and reactive actions – with a strong focus on the preventive part.
All equipment, tools, and jigs used during a production test and calibration are controlled within a calibration and maintenance process, including records of these activities. All tests using controlled equipment have records of the equipment's serial number.
By doing frequent and automated Gauge R&R (Repeatability and Reproducibility) calculations together with Process Capability Index (Cpk) measurements on the processes, we can preventively address any metrics closing in on tolerances before they are out of spec - and, by that, maintain a stable product realization. Repeatability results in reliability, given a reliable design, which we secure by adhering to the above-mentioned product development.
Proprietary Calibration Process
One of the distinguishing factors at Zivid is our proprietary calibration process. Tor Magnus shares:
Our calibration process is quite complex. What our competitors are doing, I don’t know, but the results of our evaluations demonstrate whatever they are doing - isn’t being done as thoroughly as Zivid’s is."
This process ensures thermal and ambient light stability, setting our products apart in the industry.
Staying Calibrated with Changing Temperature
Zivid quality engineers are aware of the fact that it is changes to environmental temperature that are the number one cause of 3D camera instability when in deployment. To qualify a 3D camera at a singular ‘convenient’ temperature would simply be remiss - the real world it operates in will not be like that.
All Zivid cameras go through temperature testing in a special oven
For this reason, we test all of our cameras across the full specified temperature range, 0ᴼC to 40ᴼC, where we constantly cycle the temperature between the limits. All these measured points must show trueness, accuracy, and precision, as specified in our datasheets.
In total each Zivid 3D camera receives over 100 hours of testing before it is accepted for shipment to a customer.
Proving Reliability
Proving our reliability goes back to the product development process. We conduct accelerated lifetime tests to determine the Mean Time Between Failure (MTBF), which measures the average time between failures of a repairable system or component during normal operation.
This is a testament to our commitment to reliability," says Sindre. "We design and select parts based on lifetime calculations and testing, making sure that each component contributes to the overall reliability of the product."
First Choice for Robotic Cells with High Vibrations
To be genuinely reliable, a 3D camera must overcome a series of stringent tests designed by our expert team. As Sindre succinctly puts it:
To actually be reliable, not just be considered reliable, a 3D camera has to overcome our tests."
At Zivid, we take pride in our meticulous approach to quality and reliability. We ensure our cameras meet and exceed the highest standards, even in the harshest industrial conditions.
This is not just something we like to think. In fact, many companies that are automating processes like assembly and welding, where strong vibrations affect the camera, seek us out precisely because the accuracy of Zivid cameras does not vary depending on external factors.
You May Also Like
These Related Stories
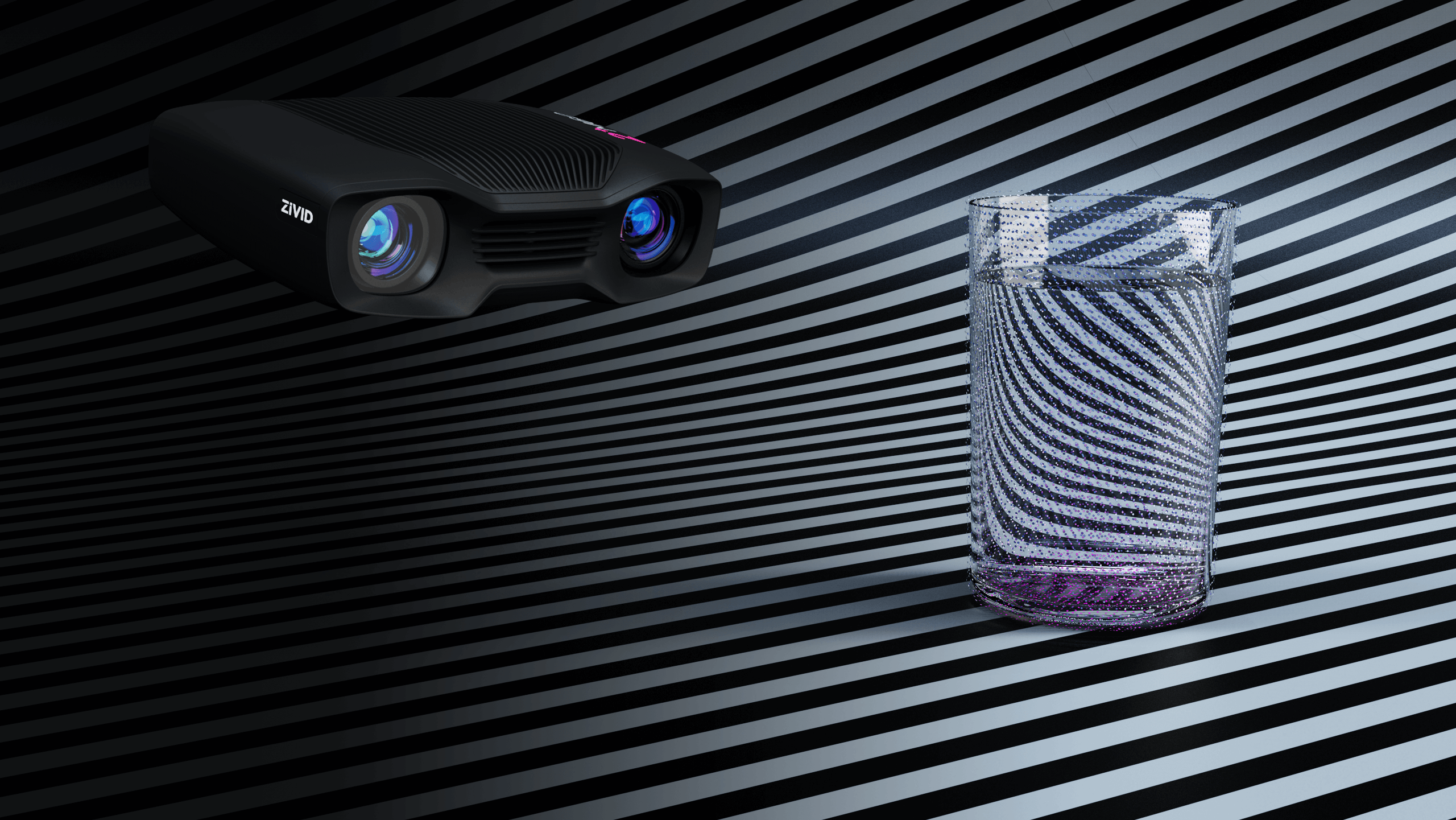
Zivid Unveils Transparent Imaging 3D Cameras
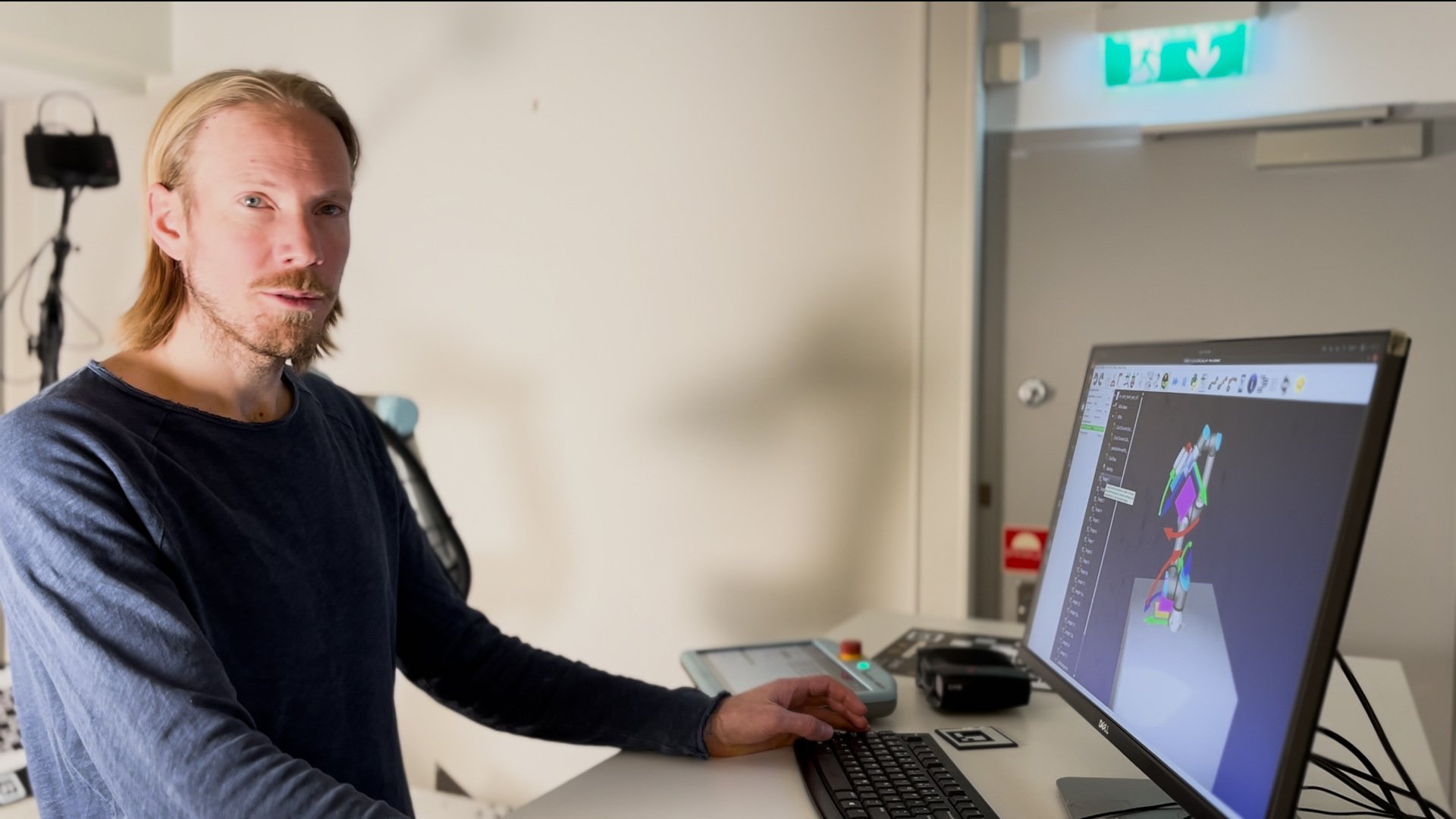
Zivid’s New Hand Eye GUI Makes Calibration and Verification Simpler
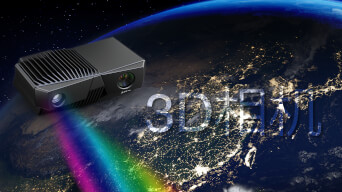