Robotic Welding with Machine Vision Explained
ABI Research state that 452,000 robots will be shipped in 2022, a massive increase of 65% compared to 2021. Joe Campbell, Senior Manager at Universal Robots, predicts in particular, “an expansion of the ease-of-use cobot paradigm beyond machine tending and into complex process applications such as welding in 2022”. He is right: the welding industry is seeing some of the most innovative growth in the field of robotics today.
Robotic welding is one of the most advanced, complex, and heavy-duty applications you can find. More and more manufacturers choose to add 3D machine vision to their automated solutions and boost their performance. With visual acuity, robots can follow weld seams with greater accuracy and speed than human welders.
Can robots really weld better? To answer that, we will see together what robotic welding is, the benefits of robotic welding with 3D vision, and give tips to enable your vision-guided welding solution. Finally, we will give a few real-life case studies.
Table of content
- Robotic vs. Manual Welding: what’s the difference?
- What is 3D vision (and why it matters)
- 3 Key benefits of automated welding with 3D vision
- Considerations before choosing your vision sensor for welding
- Robotic Welding with 3D vision: Case studies
- Conclusion
Robotic vs. Manual Welding: what is the difference?
What is welding?
Welding is a fabrication process whereby two or more parts are fused together by means of heat, pressure, or both forming a joint as the parts cool. Welding is usually used on metals and thermoplastics but can also be used on wood. The completed welded joint may be referred to as a weldment. In other words, welding is done by joining two materials together without any adhesive.
There are many ways to weld. These processes can be classified into two types:
- Fusion welding
- Solid-state welding
In this welding process, the joints are produced without the application of heat, but by applying pressure which results in diffusion or inter-surface molecular fusion of the parts to be joined. It is also known as the solid-state welding process. This process is mainly used for welding nonferrous sheet metal, particularly aluminum and its alloys. This includes ultrasonic welding, friction welding, explosive welding, etc.
Difference between fusion welding and solid-state welding
The rise of robotic welding
Across all industries, filling open vacancies for technical manual work is becoming more and more difficult. Lower-skill and semi-skilled positions where people can be brought up to speed rapidly are proving difficult enough, but where skilled labor is needed, it is a particularly worrying picture. Skilled apprenticeships have typically taken place over three or four years: you cannot teach people those jobs in a few months. Automation and robots are becoming essential to keeping economies ticking over.
Probably the most pressing case for the need for intelligent and highly capable robots is the welding market. As elsewhere, there is a critical shortage of experienced talent. A few decades ago, every big gathering probably had at least one welder in the throng, but now they are becoming a very rare find, especially in North America and Europe.
There are approximately 450,000 welders in the United States, with a current shortfall of 140,000. Now the average age of a welder in the United States is 55 years old, and for various reasons, there is a huge gap in where the next generation of welders should be.
Why is this shortage happening? The facts are that it is not seen as an attractive occupation to enter by the youth of today. The median pay of a welder is around $45,000 a year, which is about $5,000 less than the overall median in the United States. Welding is also a tough job. Working with temperatures of 2,800 °C, lots of sparks, burns, and uncomfortable, yet essential work clothing and safety equipment; it is dirty, hard work. It can be a dangerous business for humans, and even in the best circumstances, welders can only have 50% ‘on-arc’ time. Robot welders don’t have those same limitations.
Welding is a critical part of many high-value industries, and it is vital welding processes can take place unhindered in most advanced economies. Cobots have for some time now worked side-by-side with human welders to assist and carry out the more rudimentary tasks to great effect and increased efficiency. In fact, more and more well-established robotic companies have answered the call for welding cobots. Danish giant Universal Robot, for example, has been focusing the past month on marketing the UR+ products range for welding. But it is now at a point where robots need to be the welder, not just the assistant.
Manual or robotic welding: pros and cons
Robotic welding, or automated welding, refers to the process of fusing two materials together using mechanized programmable tools that heat, mix, and/or cool metal materials. Some companies still rely on manual human work, but more and more manufacturers are turning to robotic welding.
Here are a few benefits of robotic welding and some disadvantages:
Pros | Cons |
Weld Quality Automated processes and controllers ensure that weld integrity is refined with consistent results for fast-quality welds. There is also no issue with human error, fatigue, or distraction that may cause defects, unlike manual welding. |
Initial Cost Although you save money on production costs with robotic welding, the upfront costs for automated machinery are often quite expensive. Not only is the initial cost expensive, but you must factor in the amount it costs for the machinery to be maintained. |
Reduced Waste When welds are performed incorrectly, it leads to scrap metal and other wastes. Due to more accurate and precise welding, there is less scrap metal and waste with robotic welding. |
Technical Issues As with any technology, you may face technical issues with automated welding machinery. Companies that are fully reliant on robotic welding could shut down for hours or days if the welding machinery breaks down. |
Decreased Production Cost Automated welding machines perform various welding processes day and night with less manpower than manual welding. This means you don't need to hire additional staff for production. Additionally, you won't have to consider labor costs such as injury, sick leave, staff turnover, or overtime. |
Lack of Flexibility Robotic welding machines can carry out the same tasks routinely. But if you require the machines to weld a different way or to carry out other processes, the machines must be reconfigured. This usually takes extra time and money to do. |
Higher Output Robotic welding doesn't rely on the endurance of human staff to produce the work. Automated processes speed up output by working longer and moving faster than manual welders can. |
An automated system is overall more advantageous for welding, and it is a necessity to save the industry. Getting a robot to do the task is a great start, but you can go even further in the automation process by adding 3D machine vision to the mix.
What is 3D Vision (and Why it Matters)?
The world we live in is a 3D world. We, humans, see and process the visual input from our eyes to generate a 3D understanding of our environment in our brains. It follows that if we want machines to understand and perform the tasks humans are capable of, they will also need the ability to see and perceive in three dimensions as we do. For this reason, there is now a burgeoning demand in the industry for robots and machines to have the ability to do this. 3D vision systems are steadily being deployed across a range of applications in industrial, automotive, and consumer verticals. We will look at 3D machine vision technology and systems that have use cases in the worlds of automation, logistics, and manufacturing.
Robots and machines are becoming increasingly prevalent in manufacturing and industry. Machines can perform routine, dirty, and dangerous tasks, thus relieving people from doing these tasks. Some areas in industry where vision-enabled robots are becoming very popular are random bin-picking, pick-and-place, inspection, assembly, and measurement. Machine vision systems are usually comprised of five elements:
- Digital imaging sensors (CMOS or CCD)
- Optical lenses
- Lighting (specific to the vision system)
- Communication
- Image processing software
2D vs. 3D
2D vision systems have been in existence for a few decades now. These systems have served us well by yielding crucial information to help machines make better decisions. But as demands grow, 2D just won’t cut it in a lot of situations, and the evolution to 3D is clearly necessary. A very typical example of where this is needed is accurate and reliable recognition, selection, and picking of objects. These operations fall under several sub-categories, some of which are bin picking, but also welding and repair. For welding and repair operations, you need to see in precise detail and up close the parts you are manufacturing.
Read more: the basics of 3D machine vision vs. 2D
3 Key Benefits of Automated Welding with 3D Vision
The research of machine vision for robot guidance applications has been applied in the welding field and has made great progress. Sensors have been added for adaptive welding to make robots user-friendly for more flexibility and speed.
Watch the webinar "Welding and 3D Machine Vision":
1. Democratizing robotic welding
Robotic welding gives good repeatability of the welding path trajectories, as robots perform well in structured environments. However, in contrast to manual welders, the robot is not able to modify the welding path continuously by itself. Thus, a human must interfere and modify the trajectory of the robot every time something changes, which can be tedious. Many small and medium-sized enterprises are not using robots in their facilities because the configuration and programming process of this type of equipment is time-consuming and requires workers with a high level of expertise in the field.
By using a 3D vision sensor, you can improve the programming of the robot and give it the capabilities needed to be autonomous. Enhanced use of computer vision for detecting and estimating the position and orientation of workpieces to be welded could improve the efficiency of welding processes by offline programmed robots, and the required level of competence for using a robotic welding system could potentially be lowered. This will allow many more enterprises to benefit from robotic welding systems.
2. Making robots adaptable
Due to tolerances in the workpiece geometries and uncertainty in workpiece position and orientation, the desired welding path will vary from one workpiece to another. To make robotic welding systems more flexible in dealing with varying workpieces, external inputs such as computer vision must be introduced. Different types of vision sensors can be used for welding. Some will provide geometry control, while others can give thermal information.
With 3D vision, in particular, the robot gets a sense of sight of the part in front of it, what it looks like and where it is. Welding robots driven by 3D-based vision software can adapt and change the welding path when it notices small changes in the arrangement of the components that are being welded. The welding paths are corrected before execution with 3D vision, where the 3D image is aligned with the CAD model of the workpiece to be welded. This way, a welding robot is more adaptable and autonomous.
3. Increasing your arc-on time
Overestimating welding arc-on time is a common mistake. Manufacturing operations may be surprised to discover that the average arc-on time in a semi-automatic welding operation is only 10 to 12 percent. When companies aren’t thinking about how to improve arc-on time, they’re missing out on ways to improve throughput and the bottom line. Welding arc-on time directly affects how many parts go out the door each day.
We saw before that more flexibility will enable your solution to make fewer mistakes. Thus, you will manufacture parts way faster in a more consistent way. No need for touch-ups anymore. With 3D vision, robotic welding techniques offer huge possibilities for consistent quality and increased arc-on time that is not possible using human welders. In other words, the productivity of your solution would be through the roof if you fully automated your welding process with machine vision.
We know now that adding 3D machine vision to a welding system has many advantages. It opens the door for anybody who wants to automate their welding process, it makes robots flexible and autonomous, and it increases both your arc-on time and productivity. In the end, you are just doing a better job at welding.
However, enabling machine vision with your welding robot can have a few challenges if you are not choosing the right sensor.
Considerations before Choosing a Vision Sensor for Welding
1. Highly accurate 3D captures
A 3D point cloud is the digital representation of our reality produced by a vision sensor. It's this point cloud that your system must use as input when calculating how to perform changes in the real world. But the uncomfortable truth is that all 3D machine vision sensors introduce errors and uncertainties to the digital point cloud representation. When these errors are big enough, your solution will likely make mistakes. You want a sensor that is great at its job and gives you the most accurate 3D point clouds you can get to weld accurately.
Solution:
The way to remove uncertainties, and extra adjustments, and to trust the output, is simply to use an industrial robot vision camera with high-point precision and true-to-life form.
The Zivid Two industrial 3D color camera offers detail at 55 um point precision and true-to-life form and representation with < 0.2% dimensional trueness error. Zivid's industrial 3D cameras provide 2.3 Mpixel point clouds, giving you the data output, so there's no question about what objects you are looking at.
2. Working in a tough environment
It is no secret that welding is dangerous work, and that is one of the reasons human welders are harder to find. You are working in extreme conditions and in contact with vibration, heat, dust, and particles. In the case of robotic welding with a 3D camera, you must keep in mind that the sensor will have to work in a very tough environment. If you place the camera on the robot and close to the seam, where all the friction is happening, it will be even closer to danger. Any machine that is not equipped will end up crashing because of this challenging environment.
Solution:
You need an industrial-grade 3D camera for welding purposes. The key is to get a 3D camera strong enough for highly accurate arc welding processes that could also operate smoothly in a hot, dirty, and tough environment, designed with floating calibration to stay sharp despite environmental fluctuations.
3. Getting close to the seam
Welding requires that you go up close to see details that are sometimes millimeters small. Many vision sensor manufacturers choose to provide products that are ideal when mounted from far away. For welding, the perfect architecture is to have the camera mounted on the robot. This way, it can just see whatever the robot is going for and use the robot’s mobility for multi-angle captures. However, not every camera is meant to be mounted on the robot. They are usually too heavy and bulky and will just end up being in the way of the robot.
Solution:
Your welding system needs a camera light and small enough to be mounted on the arm of the robot. When you mount your 3D camera onto your robot, you have just given your robot the freedom to see anything within its reach, with optimal 3D image quality.
Zivid Two 3D cameras are specifically designed to be mounted on the robot’s arm.
4. Complex techniques require user-friendliness
Welding is very complex, but it is not uncommon to see welding processes coupled with other production techniques.
A good example is Wire Arc Additive Manufacturing (WAAM). WAAM belongs to the Direct Energy Deposition (DED) family of Additive Manufacturing and combines two production processes: Gas Metal Arc Welding and Additive Manufacturing. Compared to conventional manufacturing processes like metal casting and forging, WAAM has been around for a relatively short time, and it outperforms conventional manufacturing processes and other DED techniques in several ways (waste reduction, wide material availability, design freedom…).
Here is an example of a WAAM process by RAMLAB:
But if you are going to use multiple techniques on top of welding, adding a 3D camera that has its own application software and particularities can make your life even harder. If it is a complex product, there is a good chance you will go through some bugs, which can be a headache. You will need to allocate time to learn how to use one more item for your already complex system.
Solution:
Break down any robotic system into its parts, and it’ll ultimately be composed of just four interrelated functions: sensing, decision-making, acting and communicating. You need a sensor that focuses on one thing and one thing only: sensing. Many machine vision companies are designing sensors that include application software. You should not have to think about that on top of the rest when you are operating a welding process. You need a 3D camera that is simple, easy to use, and compatible with everything.
Robotic Welding with 3D vision: Case studies
We have selected for you 2 case studies of robotic welding applications where a Zivid 3D camera has been chosen as the vision sensor.
In a few words
Welding is one of the most difficult manual tasks you can find in the industry. As a result of the labor shortage, more and more companies have understood it is time to automate their system with a robot. If a robotic welding application has many undeniable advantages, without a vision sensor, it has a few limitations. By adding a 3D camera, you are unleashing the potential of your welding application. However, there are some key considerations we cannot disregard: the 3D camera needs to be industrial-grade, user-friendly, simple, and with high 3D point cloud quality, even when mounted on the robot.
For all these reasons, the Zivid Two M70 is ideal for the job. Book some time with one of our experts to learn more about the capabilities of the Zivid 3D cameras for welding applications:
You May Also Like
These Related Stories
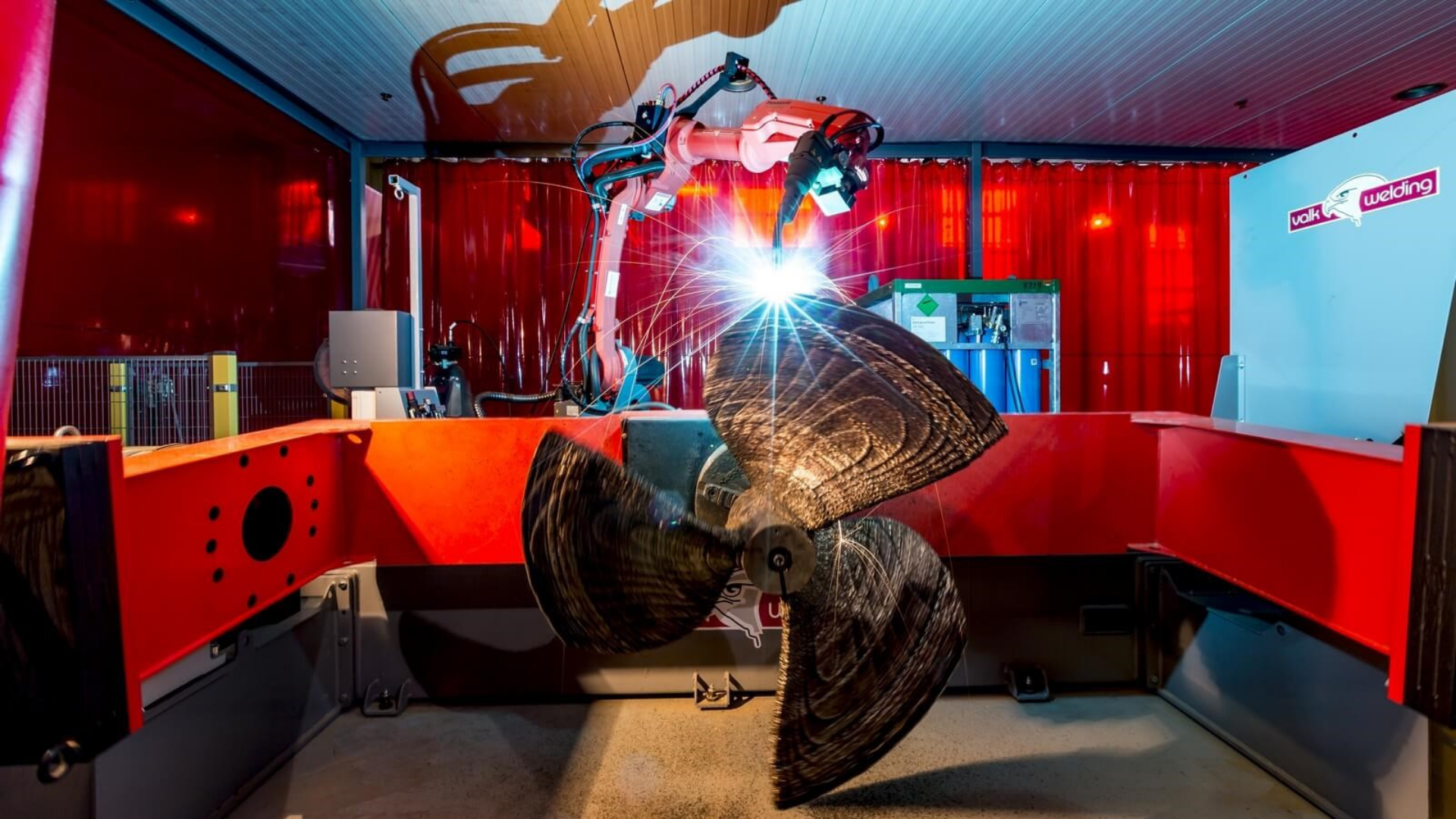
Robotic Wire and Arc Additive Manufacturing with 3D Vision
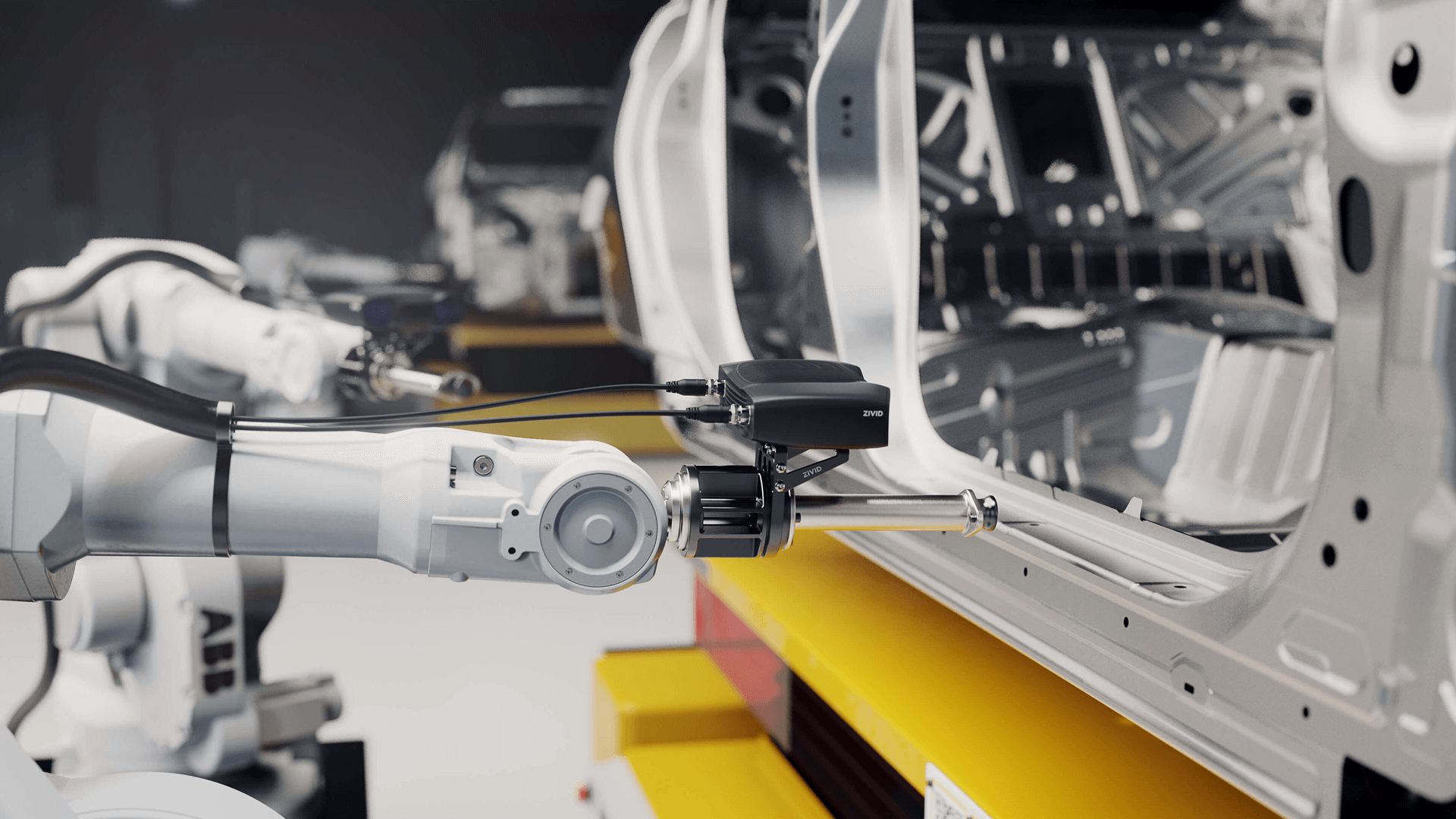
5 Examples of Robot Guidance Applications with 3D Machine Vision
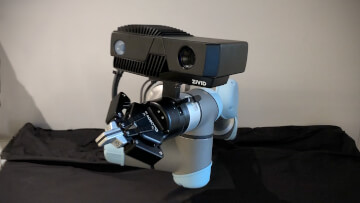