Automation set for explosive growth in 2022
The ‘new normal’ will bring new automation needs and humanlike vision requirements for skilled robotic techniques
Most analysts agree on this one. Widespread robotic automation is coming, in a big way and as 2022 rebalances we will see the uptick across multiple industries globally.
The ‘new normal’ will go beyond whether we will work from home or the office or in a hybrid manner. The new normal is going to be different at a fundamental level across myriad industries. A workforce shortage, a desire to re-shore more industry, the ever-present need to be more productive are only some of the factors driving the emergent automation boom. ABI Research state that 452,000 robots will ship in 2022, a massive increase of 65% compared to 2021. *
Pandemic and supply chain issues in the 3D machine vision industry: what is the solution?
It doesn’t happen overnight, but all the signs are there with new projects visible across industries where automation was not typically the first thought. The robot early adopters of automotive and logistics are set to be joined by thousands of more esoteric applications, in perhaps smaller numbers but massive overall quantity.
There are certain parallels to the cloud computing and IoT segments where the initial adoption was in the huge volume markets and subsequently triggered widespread longtail adoption. Robots have been a staple of automotive plants and logistics facilities for many years, now it is going mainstream.
This expansion was underway already, the pandemic has slowed some developments down, speeded others up, but as supply chains also rebalance the projects that were shelved due to product availability shortages are now being brought back to the table.
Skills shortages, people shortages, what to do?
The problem of being unable to fill open vacancies is now at an acute level. Lower skill and semi-skilled positions where people can be brought up to speed rapidly is proving difficult enough, but where skilled labor is needed it is a particularly worrying picture. Skilled apprenticeships have typically taken place over three or four years, you cannot teach people those jobs in a few months. Automation and robots are becoming essential to keep economies ticking over.
It should be considered that this is not a temporary fix, it is a fundamental shift. There is little sign that people leaving school want to enter manufacturing, assembly, and heavy industries in the numbers they once did. Automation is not merely plugging a hole, it’s a rebuild of industry as we know it.
Read more: What is Automated Material Handling?
2022 will be a landmark year for robotic deployment with over 452,000 robots deployed.
Robotic welders to go mainstream
Probably the most pressing case for the need for intelligent, highly capable robots is in the skilled labor market. As elsewhere there is a critical shortage of experienced talent. The difference here is most of these jobs take years to master and cannot be filled with the first person who walks in the door with a few weeks of training.
A few decades ago every big gathering probably had at least one welder in the throng, but now they are becoming a very rare find, especially in North America and Europe. Cobots have for some time now worked side-by-side with human welders to assist and carry out the more rudimentary tasks to great effect and increased efficiency. But it is now at a point where robots need to be the welder, not just the assistant.
There are approximately 450,000 welders in the United States, with a current shortfall of 140,000. Now the average age of a welder in the United States is 55 years old, and for various reasons, there is a huge gap where the next generation of welders should be. Welding is a critical part of many high-value industries and it is vital welding processes can take place unhindered in most advanced economies.
Welding is a skilled, high accuracy, and visually demanding task with high demands on movement and flexibility of 3D vision moving with the welding operation.
In addition to this, welding is a tough job, working with temperatures of 2,800 °C, it is dirty, hard work. Lots of sparks, burns, and uncomfortable, yet essential work clothing and safety equipment. It can be a dangerous business for humans, and even in the best circumstances welders can only have 50% ‘on-arc’ time, robot welders don’t have those same limitations.
See how Zivid industrial 3D cameras are stress-tested to work under extreme conditions.
The facts are that it is not seen as an attractive occupation to enter by the youth of today. The median pay of a welder is around $45,000 a year, which is about $5,000 less than the overall median in the United States. So, this shortfall isn’t going to go away, it is only going to become more pronounced.
This is the case for more automation and robots to be used in the world of welding, but much the same is true across automation and manufacturing industries also.
I foresee an expansion of the ease-of-use cobot paradigm beyond machine tending and into complex process applications such as welding, cutting and dispensing. Examples are OEMs such as Vectis Automation building cobot-based products that welders can set up and program for plasma cutting and MIG welding; and Robot27 that has launched a popular dispensing kit. We will continue to see new user-friendly application solutions for more advanced, heavy-duty cobot tasks appear in 2022.” **
Joe Campbell, senior manager, strategic marketing & applications development, Universal Robots
Embracing the initial costs and reaping the rewards
Often the biggest challenge is that the initial cost of ‘going robotic’ has a considerable CAPEX associated. A robot cell to replace a human can be in the tens of thousands at the lower end, stretching to many hundreds of thousands at the high end. But a high-quality robot cell will give high quality, reliable and repeatable service for five to ten years, or more. When you look at the overall costs associated with having a human, or, a couple of humans, do those jobs, it starts to look like a no-brainer. It is high-cost upfront, high reward down the line.
On-arm eyes are essential
Many industries cannot build their plant to a level of total control such that blind robots can do their job effectively. If you know everything in your process will look like it should be where it should be, is in the state that it should be, within a millimeter or so, then that’s great. But this is very rarely the case, things move, little variations occur.
Learn more about the "on-arm" paradigm and its benefits.
It is the nature of an activity such as welding or say, machine tending that the process is never 100% controlled. There will be anomalous situations where inconsistencies occur in placement and how the weld is progressing. Welding is a skilled profession where visual inspection plays an important role and relies on the flexibility of human adaptiveness to the situation.
Robots employed in such a scenario need similar flexibility and adaptiveness. Welds can follow complex paths starting on the top of an object and progressing around and underneath to completion. This is an ideal application of the on-arm 3D camera paradigm where the ‘eyes are following the hands’ of the robot.
Robotic welding is set to increase dramatically over the next couple of years.
This is why robots will need to be able to be spatially aware, in real-time to see what’s in front of them and make accurate decisions accordingly. This is why only really high-quality 3D robot vision is going to be up to the task. In addition, these robots need to be able to alter their viewpoints to get better perspectives and point cloud data on the task at hand.
In robotic terms, it is a slow painstaking process so there is no argument around possible speed/time penalties that some, often mistakenly, propose when discussing the use of the on-arm paradigm for robotic 3D vision and cameras.
In addition to the growing acceptance that in many scenarios tasking the on-arm camera route is the only way, many supporting technologies are also converging to enhance the entire process. Sophisticated motion-planning tools are becoming available that take robotic capabilities together with a camera mounted on the robot arm right up to the level of human capabilities, and in some cases taking it considerably beyond.
Robots in the world of welding will need vision quality and the on-arm flexibility of the level provided by 3D cameras such as the Zivid Two color 3D camera.
Welding or complex curved surfaces requires a flexible viewpoint provided by on-arm robot vision.
Faster to teach a robot to be skilled than a human
We know people are not entering industrial skilled and semi-skilled professions as they once did but what is interesting is it has been shown in many instances that it is much faster to spend time programming a robot to do a skilled job, such as machine tending a CNC machine than to train someone to do the same.
Benefits beyond productivity
An added benefit of moving faster towards automation is the autonomy of choice for your factory or installation. It places less dependence on a large pool of workers with specific skills, which typically means locating nearby to large population centers, in other words, in or close to cities. The new automation shift allows factories to be more self-sufficient and moving much of these operations away from cities helps alleviate other pressing issues such as traffic congestion and air quality.
MaxQ robotic welding system from RAMLAB using the Zivid Two industrial color 3D color camera.
Ultimately welding is just one type of work where flexible visually assisted robots can fill the workforce shortage. The adaptability that an on-arm high-quality industrial 3D camera can bring will come to the rescue, just as it will in a host of other industries having the same need of flexibility to fill their open position for skilled workers.
Find out more about Zivid on-arm 3D color camera solutions.
*’70 Technology trends that will – and will not shape 2022’, ABI Research.
**Originally from ‘2022 robotics predictions from industry experts’, The Robot Report. January 3, 2022.
You May Also Like
These Related Stories
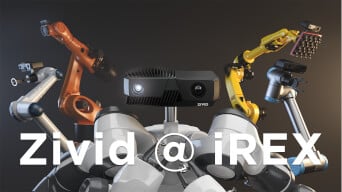
Zivid One+ and UR10 at iREX 2019
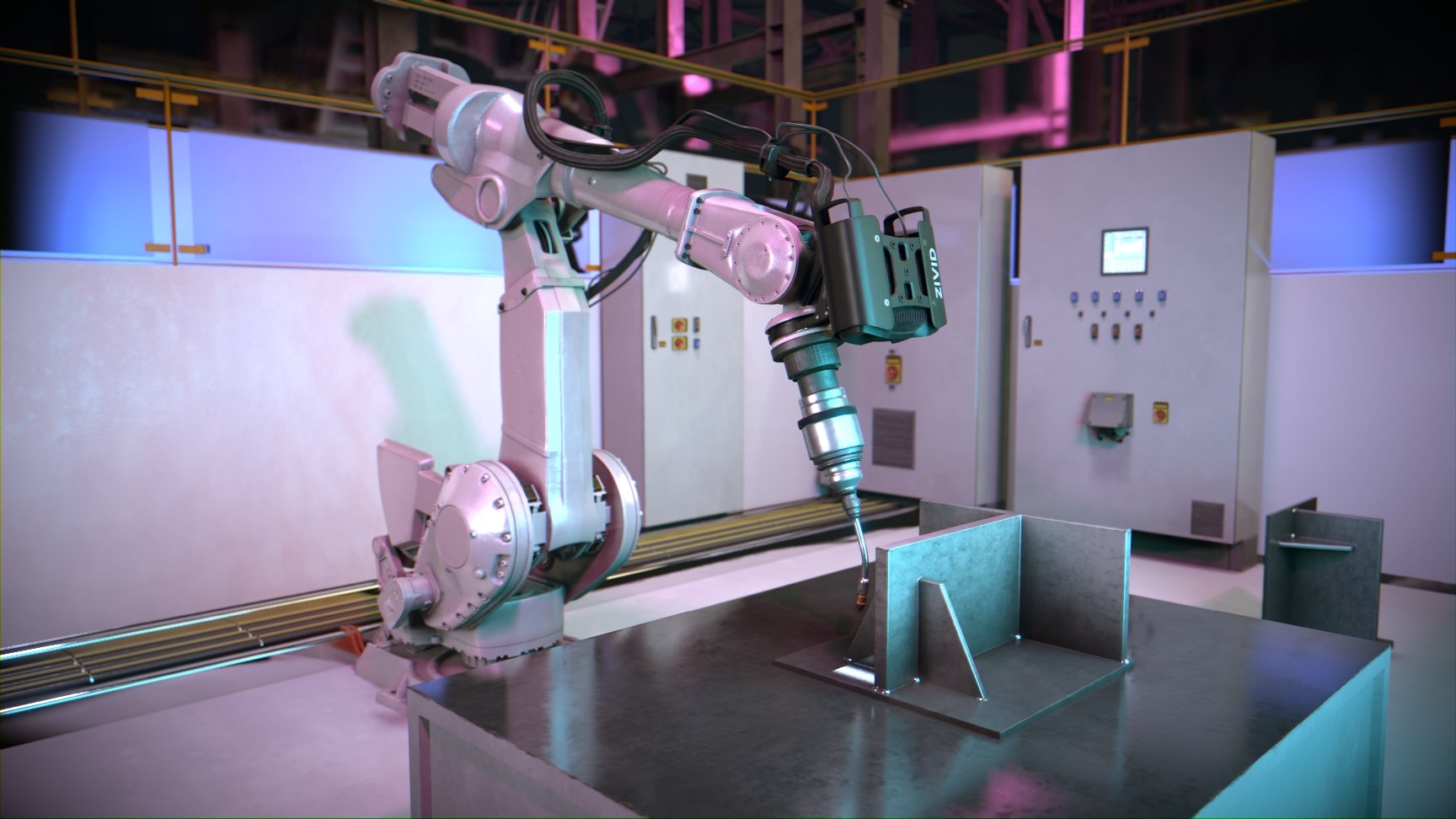
Robotic Welding with Machine Vision Explained
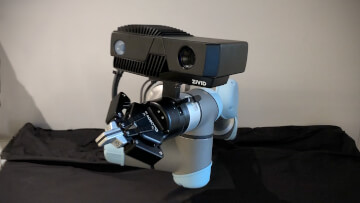