Improve Your Bin-Picking Productivity with Robot-Mounted 3D Vision
3D cameras play a vital role in bin-picking with robots. Identifying and localizing parts that are often in a complex set of arrangements in a bin requires highly accurate point clouds and sophisticated software to successfully pick parts and empty the bin. To date, most 3D cameras are mounted in a static arrangement either above or to one side of the robot. While this is often adequate, only being able to view the bin from a singular point of view can lead to situations where it is impossible to get good data on some parts. Mounting the 3D camera offers the possibility to overcome these challenges with various camera viewpoints available to the system.
Table of contents
- Bin-picking primer
- Coping with different materials
- Emptying the bin
- Can a robot-mounted 3D camera reduce mispicks and optical singularities?
- Will robot-mounted 3D hurt your picking cycle time?
- The added benefits of a much larger workspace
- Should you switch to robot-mounted 3D?
Bin-picking primer
Bin-picking is a cornerstone activity in a host of manufacturing scenarios. It involves using a robot that is equipped with a suitable end effector (gripper or suction) and 3D vision that can autonomously pick objects from a bin. Typically, the bin-picking process is designed to pick unordered parts and place them in a way that makes them ready for the next stage in the process.
A bin of unordered parts and a bin of ordered parts after robotic pick-and-place.
In manufacturing, it is fair to say that many items being picked are metal parts of some sort. However, bin picking is also used for handling items that are not metallic, such as boxes, plastic parts, and even transparent items. All of these types of objects and materials present their own specific needs and challenges, which we will explore.
Coping with different materials
As mentioned, bin-picking is employed across many industries. In manufacturing, the robot works mostly with metallic and plastic parts. In medical and pharma operations, the picking can be of cardboard boxes, transparent plastic vials, and blister packs, which are commonly found.
Metal parts are often shiny and reflective, and the interreflections created between different parts and bin walls are a particular challenge for 3D vision systems. These challenges must be overcome to have a reliable and consistent bin-picking cell. While bin picking is usually of a singular part, the robot cell needs to be adaptable to handle many different parts.
A bin with a range of reflective metal parts.
Transparent items are especially challenging, but they are not very common in manufacturing or bin-picking situations, so we will not delve further into those challenges here.
Emptying the bin
This is, of course, the name of the game in bin-picking. While there are plenty of parts in the bin, finding good candidates to pick will not usually be a challenge. But this can all change as you get to the last remaining parts in the bin. It is not uncommon to have a part that creates interreflections due to how it interacts with light in its particular position and orientation. This phenomenon is called an optical singularity and can be a function of the 3D vision or the robot kinematics; singularities are caused by various factors.
Struggling with your vision-guided bin-picking application? Watch our tutorial:
3D vision-related singularities
These occur when the vision system cannot correctly perceive depth, orientation, or features due to limitations in the imaging process.
- Ambiguous views – Object appears similar from multiple angles (e.g., a cylindrical part)
- Occlusion – Parts of the object are hidden from the 3D camera
- Specular surfaces -shiny surfaces cause errors in 3D scanning data and incorrect point clouds
- Low contrast or textureless objects - Objects with uniform color or lack of texture
A reflective washer creates a singularity with insufficient 3D data for picking.
When optical singularities occur and there are no alternative picking options, the system is in a state of stasis. Something needs to be changed to overcome this. There are different methods to overcome this. A human operator can come to help the robot by moving parts in the bin or replacing it with a fresh bin with new parts. This option can introduce significant time delays and relies on the availability of a human operator. Another option is to mechanically rearrange the parts with an agitation machine or use the robot to move the part to a new position. This is quite a violent approach to solving the problem and involves considerable cost if an agitation table is added to the system cost.
The last solution is to mount the 3D camera on the robot arm. In this scenario, when a singularity occurs, the robot can move to an alternative viewpoint, which will alleviate the problem more often than not. This last approach involves practically no extra cost, with only a few extra mounting accessories necessary.
Can a robot-mounted 3D camera reduce mispicks and optical singularities?
Taking a robot-mounted approach offers a greater range of picking strategies in bin-picking and many other manufacturing operations, such as assembly and machine tending. A classic approach is to take a capture for the next picking operation as the robot is leaving the bin after picking an object. This means the robot stops momentarily to make the capture which takes a few hundred milliseconds.
As the robot then moves to place the part, during this time, maybe around 5 seconds, all the computation for the next pick pose can take place and be ready for the next pick. Often multiple picks can be executed from a single capture, which means the time penalty incurred when the robot stops to make a capture might only be applicable for every 5 picks or so. Exposure times can be further reduced by going closer to the object in the bin. This is because this allows for brighter illumination of the scene, which leads to a shorter exposure time.
Finally, because we can now move the vision anywhere in the scene, we can use a strategy to take captures from different viewpoints alternately, which further reduces the risk of singularities. So, how do we approach bin-picking using a robot-mounted strategy? Firstly, choose a 3D camera such as the Zivid 2+ MR60 that is designed to excel in robot-mounted operations and has a suitable range of accessories.
3D captures taken as the robot is leaving the bin is part of a robot-mounted strategy.
Zivid 3D cameras are supported with a comprehensive range of accessories for robot mounting.
Will robot-mounted 3D hurt your picking cycle time?
This is a common concern when considering mounting the 3D camera on the robot to overcome unpickable parts due to singularities or other factors. The truth is that robot-mounted 3D vision will probably reduce the picking cell’s average picking time. While each cycle may have a cycle time that is very slightly longer, it will consistently empty the bin without long delays when waiting for operator intervention.
So, will a bin-picking robot with a robot-mounted 3D camera be slower than one with a static-mounted camera? The answer is, well, it depends. Sometimes, it can be slower, sometimes faster, but in practice, they are most likely to be very similar.
The added benefit of a much larger workspace
When the 3D camera is mounted on the robot, the available working area of the robot with associated 3D vision is vastly increased. Because the camera now travels with the robot, the entire operational envelope of the robot can now be considered viable for performing pick-and-place tasks. This opens the possibility of servicing multiple bins and workspaces with a single robot and vision system. This represents a leap in robot cell flexibility and adaptability and a potentially significant reduction in equipment expenditure overall.
Robot-mounted 3D vision expands the operational envelope of the robot.
Should you switch to robot-mounted 3D?
The benefits of switching to robot-mounted 3D vision in your robot cell are compelling. The range of viewpoints greatly reduces the problem of unpickable parts. You can confidently make productivity predictions and remove risks and uncertainties in your manufacturing processes. Combining this with the expansion of the working area and the capability of what a single robot and 3D camera can achieve is a game-changer for those who have adopted the robot-mounted paradigm.
Many engineers are still a little wary of making the switch to mounting the 3D camera on the robot arm because they perceive it as a very complex undertaking. At Zivid, we have customers such as PickIt who have embraced the robot-mounted approach with great success.
Is it time to rethink how you approach your robot cell and enjoy the advantage of robot-mounted 3D vision?
Watch the tutorial "Mastering Robotic Bin-Picking with Zivid 2+ 3D Vision" →
You May Also Like
These Related Stories
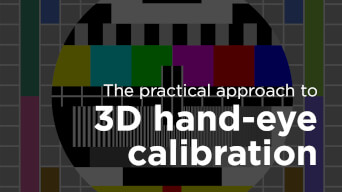
The practical guide to 3D hand-eye calibration with Zivid One+
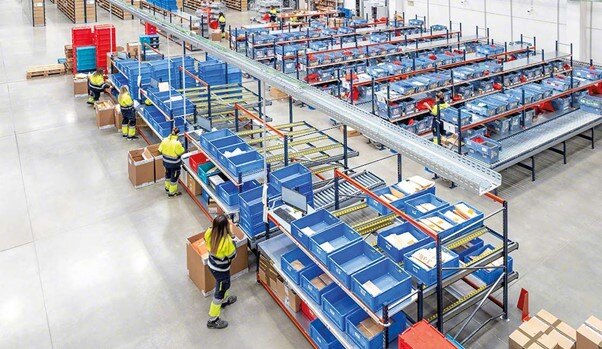
Why Low-End 3D is Hurting your Warehouse Piece-Picking Entitlement
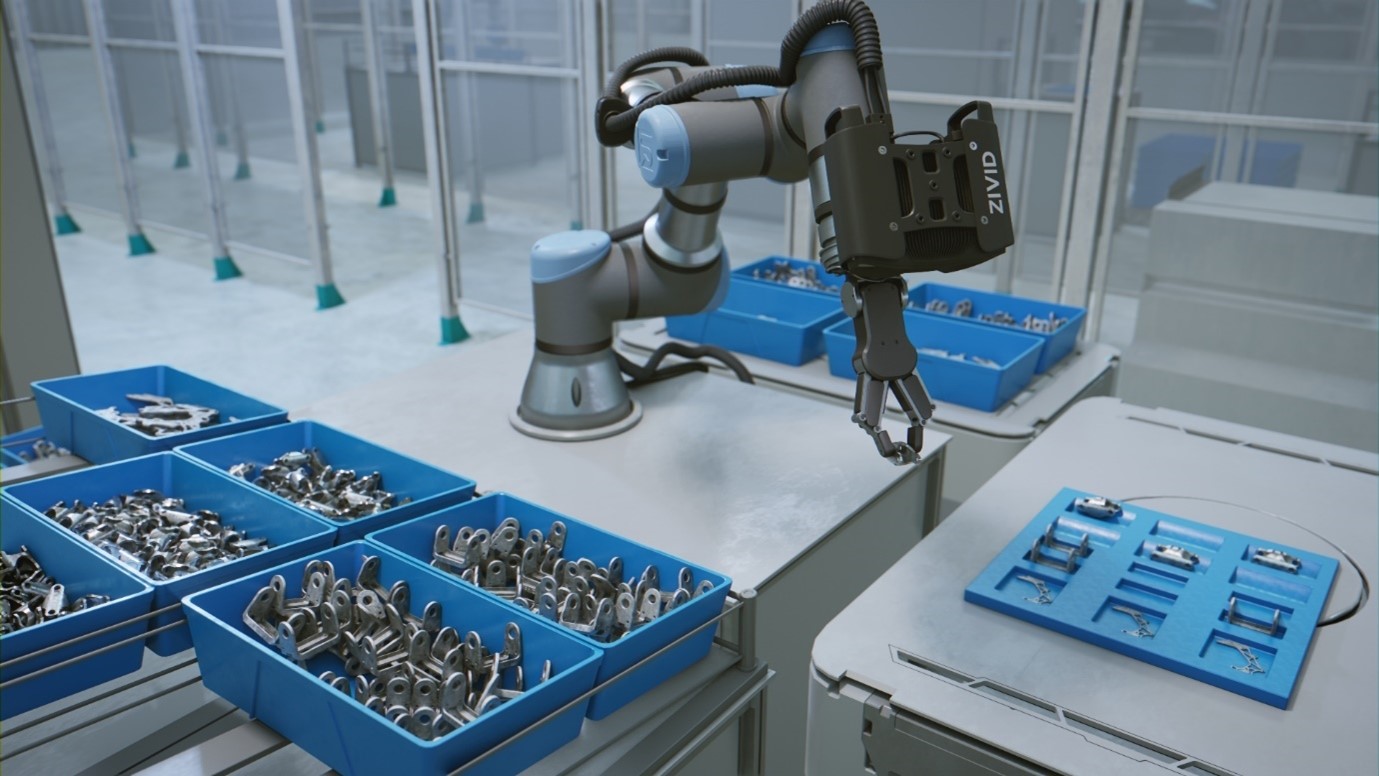