How to Improve Order Fulfillment Processes
In the rapidly evolving landscape of e-commerce and intralogistics, efficient order fulfillment is crucial for maintaining customer satisfaction and competitive advantage. Among the various stages of order fulfillment, order picking (or piece picking) is one of the most critical and challenging tasks.
Table of contents
- What is Order Picking?
- Benefits of 3D Vision in Order Picking
- Main Challenges of Order Picking
Cycle time
Object shape and surface
Gripper compliance
Motion planning and collision avoidance - Conclusion
What is Order Picking?
Order picking, or piece picking, involves precisely picking and placing individual items from bins and totes. The millions of different items, often called SKUs, vary in shapes, sizes, and materials. A vision system must be capable of providing high-quality point cloud data for all these SKUs. Simultaneously, the robot system must ensure a low cycle time and a high throughput rate. Finding the line where the data quality is satisfactory and the solution is time efficient is vital for a successful application.
Mecalux order picking solution with Siemens Pick AI software and a Zivid 2 3D camera
Benefits of 3D Vision in Order Picking
Order picking has historically been a human task, as the demands on vision and dexterity to perform the task at the desired speed are high. Robotic automation brings the benefits of 24/7 operation, consistent performance, and reduced costs. In the case of robotic automation, the vision system is essential and needs to be comparable to human levels.
- Enhanced Accuracy: Nothing is more accurate than the human eye. But if you want to go full automation, 3D vision can enhance the accuracy of your robot. By providing precise item recognition and location data, 3D vision significantly reduces picking errors. This leads to higher order accuracy, fewer returns, and improved customer satisfaction.
- Increased Speed: Automated systems equipped with 3D vision can process orders faster. Pick and place robots and automated picking systems can quickly navigate the warehouse and retrieve items with minimal human intervention.
- Reduced Labor Costs: Automation reduces the dependency on manual labor, leading to cost savings. It also alleviates the challenges associated with hiring and training a large workforce.
- Optimized Space Utilization: 3D vision systems can analyze and optimize storage layouts, ensuring that items are stored efficiently. This minimizes retrieval times and maximizes the use of available space.
- Scalability: As businesses expand, 3D vision technology can easily scale to accommodate increased order volumes. Automated systems can be programmed to handle higher demands without compromising efficiency.
We discuss this subject in detail in our webinar with Siemens and Universal Robots, “Next-Gen Solution of Intra-Logistics Fulfillment.” Watch it on the go here:
Main Challenges of Order Picking
The main objective for successfully picking an object is to compute an accurate picking pose for the robot. Both 2D and 3D data are helpful for finding the picking pose. In 2D, object segmentation or recognition is typically done with, e.g., template matching or machine learning networks. For utilizing 2D data, it is especially important to minimize defocus, blooming, and saturation. In 3D, object segmentation, detection, or pose estimation is typically done with, e.g., CAD model matching, machine learning networks, or geometry matching.
- Cycle time
- Object shape and surface
The variety of products that need to be handled is wide. Now, we will focus on some of these objects and scenes. The presented categories of scenes are handpicked because they each constitute individual types of challenges.
Textured scenes
For these scenes, preserving 2D and 3D edges is most important. Sharp edges enable one to clearly see, for instance, gaps between objects that are closely stacked and clear differences in depth for overlapping thin objects. This means it is easy to see where one object ends and where another begins. This is important for detection and segmentation algorithms both in 2D and 3D. 3D shapes are also important to maintain for doing, for instance, plane fitting for detection and pose estimation algorithms using 3D data. For 2D detection, textures should also be preserved, i.e., with minimal saturation, blooming, and halation.
Reflective scenes
For these scenes, it is important to preserve the 3D shape of the object. The surface coverage should also be as continuous as possible. This is important for 3D detection algorithms. For 2D detection and object segmentation, the edges should be sharp and visible. Additionally, to ensure object detection in 2D, the textures should also be preserved, i.e., with minimal saturation, blooming, and halation.
Transparent scenes
Transparent and semi-transparent objects are among the most challenging objects to identify in piece-picking applications. These objects often lack well-defined edges and surface features, and the data may be noisy and patchy. This makes it difficult to represent their true shape and, for many object detection and pose estimation algorithms, to correctly identify them. Having good surface coverage is crucial for successfully detecting and picking these objects. Lighting conditions, background, and capture angle are other factors that should be considered to ensure a successful pick.
Learn more about Zivid 2+, the world’s first 3D camera that can image transparent objects →
- Gripper compliance
- Motion planning and collision avoidance
Motion planning optimizes a robot's picking trajectories to save cycle time and is often combined with collision avoidance to prevent crashes into obstacles like bin walls and other items. The vision system helps the robot identify and avoid these obstacles. Ideally, the vision system would perfectly map the environment, but artifacts such as false or missing data can occur. False data appear as non-existent objects while missing data create gaps in the point cloud. These artifacts can impede the robot's movement, requiring motion planning to determine which obstacles can be safely ignored. Higher-quality 3D data from cameras can simplify motion planning and collision avoidance.
Conclusion
Improving order fulfillment processes, particularly order picking, is essential in the competitive e-commerce and intralogistics landscape. High-quality 3D vision technology offers a robust solution to order-picking challenges by providing precise item recognition, increasing picking speed, reducing labor dependency, optimizing space utilization, and ensuring scalability. The implementation of 3D vision systems can enhance order accuracy and improve efficiency. As technology advances, integrating 3D vision into order fulfillment processes will be crucial for businesses aiming to stay ahead in a rapidly changing market.
Want to learn more? Watch our on-demand webinar with Siemens and Universal Robots, “Next-Gen Solution of Intra-Logistics Fulfillment”:
You May Also Like
These Related Stories
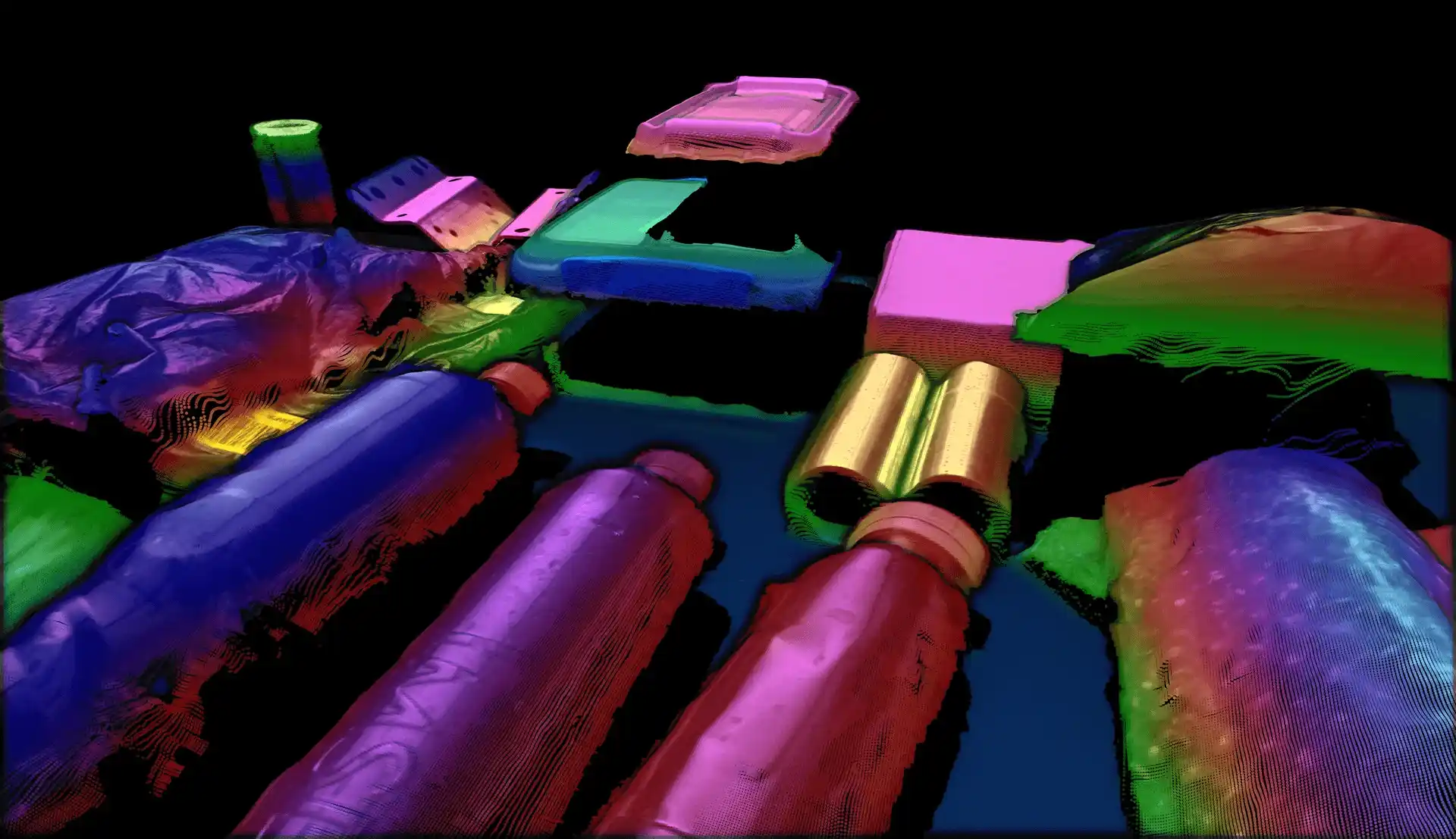
Why You Need to Capture in Both 3D and 2D for Order Picking
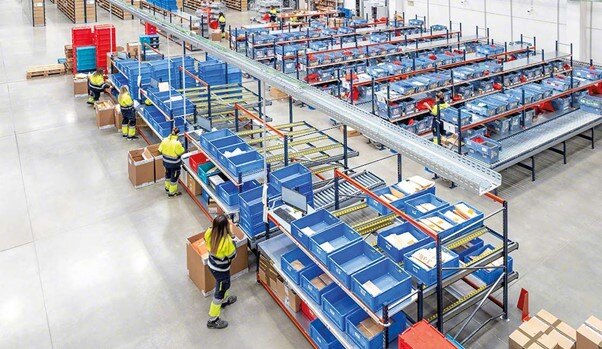
Why Low-End 3D is Hurting your Warehouse Piece-Picking Entitlement
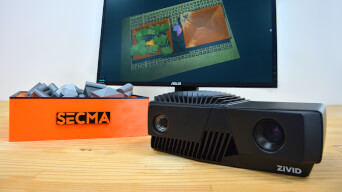