7 Factors to Consider When Choosing a 3D Camera for Your Welding Cell
When integrating a robotic solution to automate a welding process, choosing the right 3D camera is crucial. The camera not only affects the accuracy and efficiency of the welding process but also plays a significant role in ensuring quality. Here's what you must consider when selecting a 3D camera for your welding cell.
Table of content
- Environmental Conditions
- Precision and Trueness Requirements
- Field of View and Working Distance
- Ease of Use
- Flexibility and Future Proofing
- Cost vs. Value
- Vendor Support
- Conclusion
1. Environmental Conditions
Welding cells are harsh environments with intense heat, sparks, and smoke. Your 3D camera must withstand these conditions without compromising performance. Consider cameras with robust enclosures that protect against dust, debris, and temperature fluctuations. Additionally, the 3D camera must tolerate the intense light from welding arcs without damaging any components inside the camera. With an IP65 rating, Zivid cameras perform in hot and particle-dense environments. It can withstand knocks and vibrations and still perform with excellence.
While Zivid 3D cameras are designed to deliver high performance, additional protection is needed in tough environments. Without adequate protection, even the most advanced 3D cameras could suffer from damage over time. Welding, for example, can send material splatter, damaging the camera's glass or lenses. Our welding customers use protective housing for their cameras to shield them from any shock. Take, for example, RAMLAB, which has designed protective gear for tough conditions:
2. Precision and Trueness Requirements
The holy grail of every robotic system is to achieve high accuracy and be as reliable as possible. Your 3D vision solution is accurate when high precision and high trueness are met. Precision is a well-known term: it represents the ability to distinguish edges of the object so that they are clearly visible and not “hidden” by general surface noise. Trueness is making sure the dimensions of the object are true to reality. Considering precision and trueness as independent metrics is critical to having a quality welding system.
Read more about accuracy, trueness, and precision →
For welding, the 3D camera must provide high-quality data on the precision and trueness front. High accuracy is essential for detecting small variations in parts and ensuring the welding torch is guided precisely. Crafted specifically for this kind of application, Zivid 2+ M60 has a dimensional trueness error of <0.2% and point precision of 80 µm, even in harsh conditions.
Metal parts captured with Zivid 2+ M60
3. Field of View and Working Distance
The camera's field of view (FOV) and working distance are critical factors. Depending on the object you are welding, you might want to choose a 3D camera better suited for smaller imaging areas, where finer details need to be captured, or a camera designed to have a wide field of view coverage for large objects.
Welding tasks often involve working on undulating, curved, and angled surfaces lying on different planes (X + Y). The end tool of the robot will often have to move through 180 degrees or more. This relies heavily on the inherent flexibility provided by a 6-axis robot. Because these surfaces lie through different planes and angles, capturing 3D and 2D images from a static point is almost impossible due to the limited field of view and viewpoint origin.
As a solution, choose to mount the sensor on your robot's end-effector. By elevating the robot's flexibility with a robot-mounted camera, you enable the system to view the scene from multiple angles and positions and to move closer or farther from the object, giving all the details you need and avoiding blind spots.
Learn more about robot-mounted 3D cameras →
4. Ease of Use
Seamless integration of the 3D camera should be a high priority for your automation system. When you have a 3D camera, you should be able to plug and play it to get your 3D data. It’s important to check what kind of interface you expect for your camera; for example, do you have a computer in your system, or are you expecting direct communication with the robot? Like Zivid, most high-performing 3D cameras require a PC as a middleman to handle point cloud processing and detection before sending poses to the motion planning software, either on the PC or robot controller.
At Zivid, ease of use is very important. Supported on Windows, Linux, and Jetson Devices, the Zivid SDK is free and easy to install. We have included ArUco marker detection in our latest release. ArUco markers have become a staple in computer vision for detecting and identifying objects. This new feature makes it easier than ever to get pose information from these markers in your scene. You can easily perform touch tests and hand-eye calibration, create a stitching turntable, detect container ID, and more.
One last point to note: the usability of the 3D camera can affect both the initial setup and long-term maintenance. Look for a camera that offers intuitive setup and calibration processes, minimizing downtime during installation. Regular maintenance should be straightforward, with easy access to components that may require cleaning or adjustment.
5. Flexibility and Future Proofing
Finally, consider how adaptable the 3D camera is to future needs. As your production processes evolve, you may require new features or higher performance from your 3D vision system. A flexible camera that can be easily upgraded or reconfigured will provide better long-term value.
Check if the camera supports software updates and if the hardware can handle potential future requirements. It is important to choose a product that offers regular, accessible updates at no cost. Zivid releases an update of their SDK every 3 months (and it’s free!), ensuring the best quality for their customers.
Infield correction is a very important tool in the Zivid toolbox and paramount to future-proofing. It is designed to calculate, verify, and correct the dimension trueness of Zivid 3D cameras. Using infield correction, you can check the dimension trueness at different points in the field of view (FOV) and determine if it is acceptable for your application. If the verification shows the camera is not sufficiently accurate, then a simple correction process can be performed. This function helps enable long-term maintenance and stability of your welding cell. With infield correction, you can verify the dimension trueness of your camera seasonally or after accidental collisions have occurred.
6. Cost vs. Value
While cost is always a factor, evaluating the overall value the 3D camera brings to your welding cell is important. A higher upfront cost may be justified by superior accuracy, faster processing times, or reduced maintenance needs. Having a more expensive camera can also mean less engineering resources are needed to integrate it into your cell. Consider the total cost of ownership (TCO) over the camera's lifespan, including any potential savings from increased efficiency, reduced rework, and improved weld quality.
The best way to evaluate the cost vs value of a product is to get the testimonies of customers already using it. Read the customer story from RAMLAB, using Zivid 2 for welding applications.
7. Vendor Support
The reliability of your 3D camera is paramount in a production environment. Choose a camera from a reputable vendor with a record of high-quality products and excellent customer support. Reliable technical support can be a lifesaver when troubleshooting issues or optimizing the system for specific applications. Zivid, for instance, offers comprehensive support and continuous updates, ensuring your system remains up to date with the latest advancements.
Read the blog: Reliability in Harsh Conditions: Insights from Zivid's Quality Experts →
At Zivid, customers do not depend on contacting the support team; they can troubleshoot themselves, too! You can find all the information you need on your own in our Knowledge Base.
Conclusion
Choosing the right 3D camera for your welding cell is a balancing act that involves multiple factors. Finding the right camera requires careful consideration of performance, cost, environmental resilience, and future adaptability. It's essential to strike the right balance between these needs to ensure you get the best value for your investment without compromising quality or efficiency.
To help you navigate this complex decision-making process, we’ve created an in-depth ebook, “Key Considerations for High-Performance Robotic Welding with 3D Vision”. This guide offers comprehensive insights into everything you need to know, from selecting the right camera to optimizing your welding processes.
You May Also Like
These Related Stories
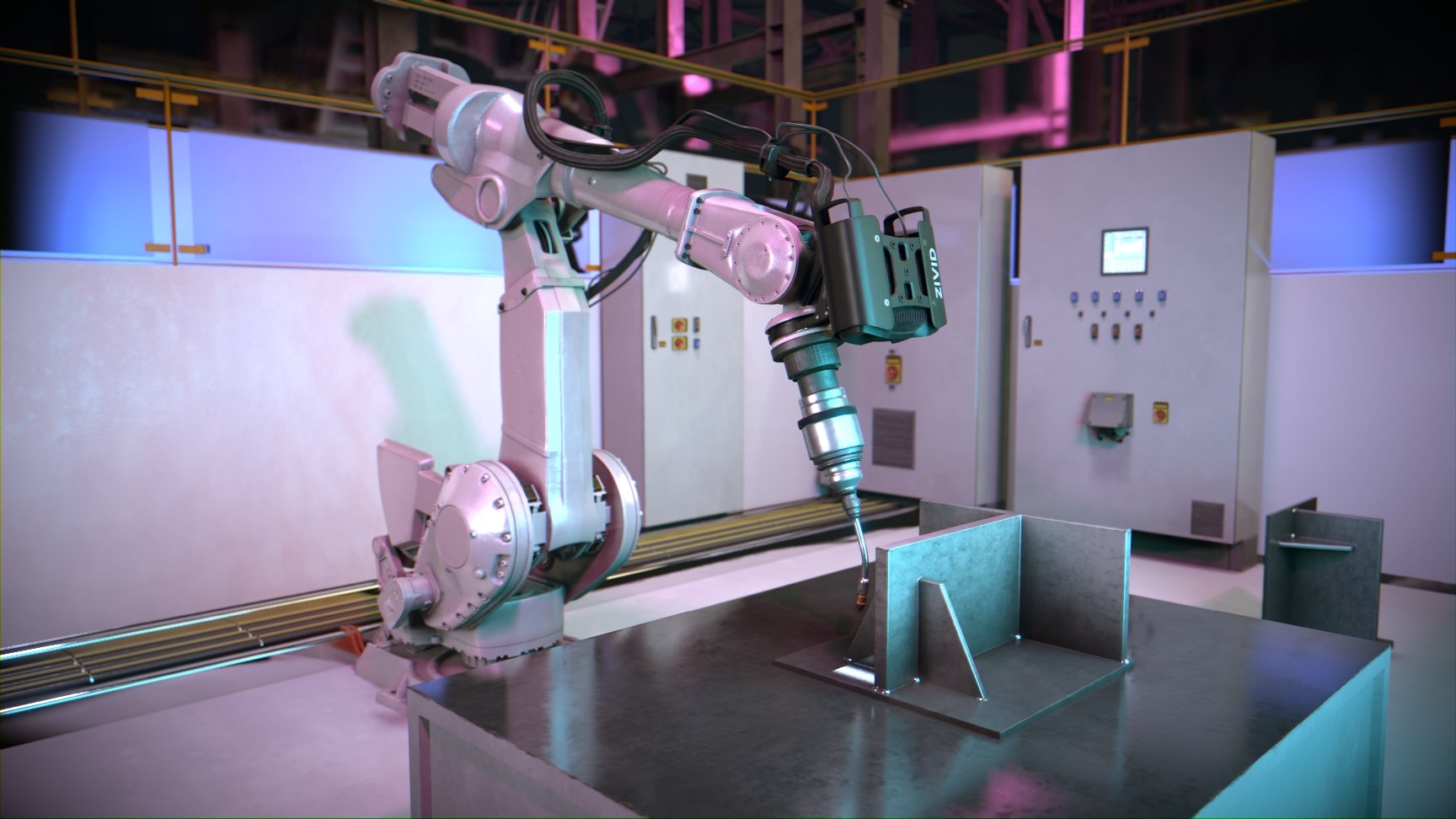
Robotic Welding with Machine Vision Explained
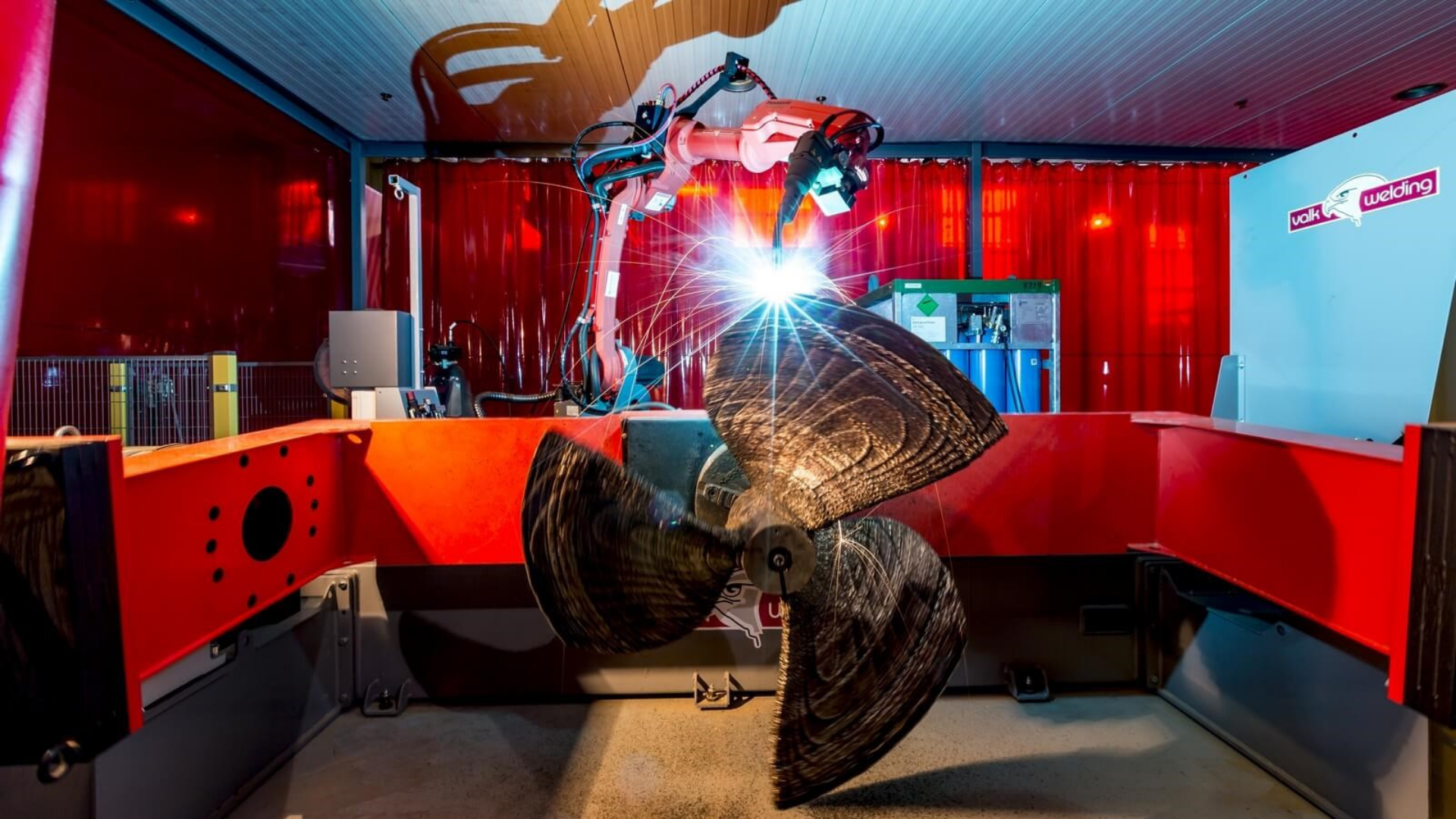
Robotic Wire and Arc Additive Manufacturing with 3D Vision
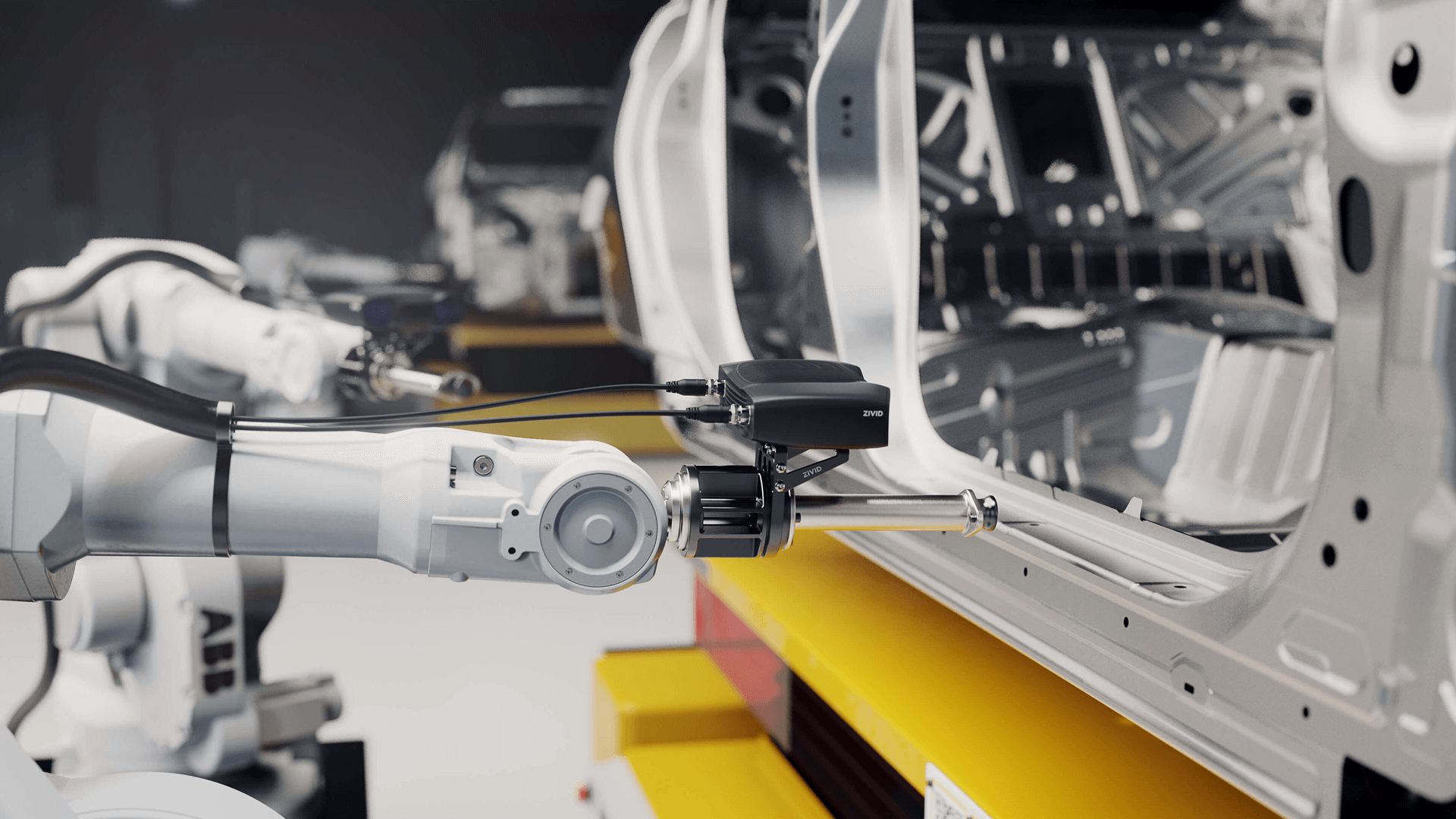