5 Benefits of using 3D Machine Vision for your Pick and Place Robots
Pick and place robots are widely used in manufacturing and logistics environments. They provide higher productivity compared to manual work as they can reliably run on a 24/7 basis. With high-performance 3D vision, they can add more value to warehouse operations and perform repetitive or dangerous work that human workers avoid. In this blog, we will discuss the benefits of using 3D vision for pick and place robotics and explore real-business use cases.
Table of content
- What is a pick and place robot?
- What is 3D machine vision?
- Five benefits of 3D machine vision in pick and place robotics
- Examples of pick and place robots with 3D machine vision
What is a pick-and-place robot?
Pick-and-place robots are used in industrial automation scenes to move parts from one place to another. In a typical automated bin-picking scenario, an industrial robot can pick an item from a bin and put it into another bin or a package for further processing. The bin-picking operation aims to empty the bin without damaging or crashing the target objects. In machine tending, a pick and place robot can be used to load and unload parts into machines or insert objects into a feeding hole in a uniform way. The goal of 3D machine vision is to achieve comparable levels of human vision and, in some areas, such as depth resolution and accuracy - surpass it.
What is 3D machine vision?
3D machine vision provides eyes to robots so that robots can detect, process, and perform a given task. Human vision is capable of capturing high-resolution, wide dynamic range images in an extreme working distance, with color and depth perception on virtually any object. The goal of 3D machine vision is to achieve comparable levels of vision and surpass human vision in some areas, such as depth resolution and accuracy.
Five benefits of 3D machine vision for pick and place robots
1) Accuracy
Robotic pick and place require high-quality, accurate point clouds. High-resolution 3D data enables robots to detect a broad set of objects and surfaces, allowing faster, more flexible, and more reliable robotic operations. Traditionally challenging parts such as sheet metal, machined and polished parts, and glossy packaging can be automatically handled with our OmniEngine 3D vision technology that uses robust reflection suppression technique and exposure control.
Zivid 3D cameras provide best-in-class point clouds with sub-millimeter level resolution, native full RGB colors, and > 99%-dimension accuracy even of transparent items. All Zivid 3D cameras go through extensive factory calibration across the entire working volume of the 3D camera. Each camera underwent over 100 hours of intensive testing to ensure quality remained the same, even under vibration, drop, and temperature extremes.
2) Productivity
With high-performance 3D sensors, pick and place tasks such as detection, processing and picking of random objects have become easier and more efficient. The vision-guided robots can continuously operate without losing quality and productivity, which is essential for e-commerce, manufacturing, and logistics businesses. Further, the automated robotic system can handle more parts faster, more precisely, and more reliably than manual labor.
The Zivid 3D cameras can distinguish features smaller than 5mm with robot-mounted flexibility. This enables robots to reliably empty the bin generating consistent productivity. With its true-to-reality 3D point clouds, robots can easily capture tiny, densely packed objects in milliseconds without mispicks and crashes.
3) Reliability
Reliable picking is not only dependent on precise and reliable object detection but also a correct interpretation of the object's size, position, and form. These qualities are fundamental to localizing parts and finding the most optimal grasp points. Segmenting individual items and boundaries are important to find the best possible grasp points. That is why trueness errors due to scaling, rotation, and translation matter in pick and place robotics.
Trueness describes how true your image is to the reality you are representing. Many customers say that despite being able to see the objects in their bins using an incumbent 3D sensor, their robots cannot pick them every time. This is because the point-cloud images are not true: there can be scaling errors, where objects appear larger or smaller than they are; rotation errors; or translation errors, where objects appear to be in a different orientation or position than they are in reality.
Zivid 3D cameras deliver high-quality 3D vision with a very low trueness error of less than 0.2%. With the low trueness error, the Zivid 3D camera can measure the correct representation of an object’s form and dimensions, rotation and position, and any warping or skew from the ‘the truth’. It improves picking reliability under mechanical stress from handling and use, which is crucial for industrial applications.
Watch the webinar on Point cloud trueness: the secret to reliable picking:
4) Safety
Industrial robots are designed to carry out tasks beyond the strength of humans; they incorporate very powerful, high-torque motors, which means they are capable of inflicting very serious injury and damage if not managed correctly. While industrial robots still must be treated with care due to their powerful capabilities, with 3D vision they can have much better situational awareness and can become cognizant of their environment and surroundings, and thus safer.
With advanced 3D machine vision technology, robots can now see better, work safer, and make aware of their surroundings better. It means that industrial robots can collaborate with human workers or operate by themselves safely with 3D vision.
All the Zivid cameras use a safe white light source for illumination, which is the best choice for various industrial automation applications. The Zivid cameras are designed for pick and place robotics to minimize mispicks and crashes. The high accuracy level makes it ideally suited for collaborative human-robot work scenarios.
5) Cost
Automating repetitive processes increases efficiency by reducing long-term costs and improving quality. High-quality 3D vision helps automate a broader range of labor-intensive tasks with better results. The initial investment in automating the tasks can be highly cost-effective as you save long-term manual labor time for repetitive tasks. It also helps mitigate the skilled labor shortage without the need to train new employees on a regular basis.
Zivid 3D cameras enable industrial, flexible, high-quality automation applications. With multiple mounting options, you can use a single 3D camera mounted on the robot arm to capture point clouds from different angles and positions. Therefore, the 3D vision minimizes the total cost of ownership by reducing the number of components that need to be installed, calibrated, maintained, and repaired. Each Zivid camera also undergoes a series of functional, environmental, reliability, and performance tests to ensure that customers can enjoy its performance throughout its lifetime without additional maintenance costs.
Read more → Unlocking the Full Potential of Bin Picking with the Right 3D Camera
Examples of pick and place robots with 3D machine vision
Pick and place robotics in the logistics industry
Logistics is a high-paced real-time operation with multiple boxes, parcels, and packages moving quickly through logistics facilities. It is a very unpredictable situation with no prior knowledge of what will arrive and need to be sorted and sent to its destination. These demands necessitate a highly adaptable and intelligent solution that can make decisions and learn as it goes. Over time a system understands more of what it sees and becomes even faster at differentiating between items.
Fizyr is an expert in pick and place solutions for the logistics industry. With a solid understanding of the challenges involved. Together with Zivid 3D camera technology, they have developed and deployed systems operating at some of the biggest logistics facilities on the planet. This is all about recognition, making a decision, and acting correctly on that decision. Fizyr excels at software that can perform this task. But the data in any system will determine its efficacy. That is why they use Zivid 3D vision for robots. With their unparalleled point cloud fidelity in color. They are able to depend on what the robot is seeing and make informed decisions about automated picking and sorting.
Fizyr solutions are being used extensively in some of the largest, fastest-moving picking and sorting operations on the globe. Fizyr detection and picking software, together with Zivid's machine vision cameras, are proving themselves each and everyday making rapid decisions with a first-time-right solution essential for such a demanding application.
Read the full customer story →
Pick and place robotics in the automotive industry
The automotive industry is still very dependent on human labor for its operations. The assembly process is a particularly human-intensive part of the process. Many of the heavier tasks have been handed across to more efficient collaborative robots for some time, where the benefits were obvious. However, much of the assembly of a vehicle is thousands of smaller items on the car chassis and interior. When a human performs these tasks, they are often in awkward to get places, requiring work in uncomfortable positions for a human. Humans get fatigued when working this way, and robots don’t, so there is an obvious benefit to automating this work.
Automotive assembly is highly human-intensive with multiple complex and awkward operations. It is time-consuming and can lead to work-related injuries for those involved. Until recently, the technology wasn’t ready to meet the range and complexity of these tasks. With robot-mounted Zivid 2 3D sensing and sophisticated deep learning software, these assembly operations are now benefitting from automation efficiencies.
CMES are experts at making robots visually aware and capable of making considered decisions. They have married the outstanding performance of Zivid industrial color 3D cameras with the early version of EQUAL AI technology which will be officially launched in Q1 2023. 2D and grayscale solutions have been tried out before, and just weren’t suitable due to additional calibration work for accurate part detection. CMES have been able to develop a highly intelligent robot cell that has the 3D visual ability and the intelligence in software that offers a solution that performs accurately and reliably, something essential to the automotive industry.
One example of this was the leveraging the Zivid 2’s full RGB color capability to enable much better part differentiation and detection. Another was using Zivid 2 because of its short baseline and true robot-mounted design to mount the ‘eye’ on the robot itself thus allowing the robot to see into any space or area, from any angle that was best suited.With the Zivid 2 machine vision camera and CMES’ EQUAL AI software, customers in the Korean automotive industry now have a highly adaptable and reliable robot vision system that can confidently tackle the myriad of assembly operations in car manufacture.
Pick and place robotics in the pharmaceutical industry
ESSERT is a robotic company founded in 2009 and based in Ubstadt-Weiher, Germany. The company designs modular and flexible robot workstations that enable human-robot collaboration for various manufacturing companies. Vetter, a leading manufacturer of pharmaceutical packaging solutions, approached ESSERT for a new solution to automate the packaging process of transparent syringes.
Transparent syringes are provided in a tote box before they are sorted and packed. Each syringe needs to be picked and placed correctly into the shipping tray from its random position in the box. This 24/7 process can be very costly and time-consuming when performed manually.
The new automation system aimed to detect, select, pick, and place individual transparent syringes within a few seconds with minimum manual interference.
Essert's robot cell needed advanced 3D machine vision to enablea reliable bin-picking operation for syringes in bulk. One of the challenges was handling the syringes' transparent property. With unclear edges and overlapping features, transparent materials are considered impossible or one of the toughest challenges for machine vision applications.
Ensuring a reliable and fast production cycle introduced another challenge. The YuMi robot had to complete each pick and place within a few seconds to meet the increased demand for medical devices. As a result, the machine vision system detects a target object, generates a 3D image (point cloud), and calculates the correct pick position in less than a second.
ESSERT decided to collaborate with Pickit, a 3D machine vision system provider, for handling transparent syringes. Fortunately, each syringe includes a black, reflective feature, which helps the system identify each object. Pickit’s M-HD machine vision system, which includes a Zivid 1+ 3D camera, was chosen to solve the bin-picking challenges, as the high-accuracy 3D camera is designed to detect small objects.
The Zivid 1+ 3D camera uses a 2.3 MPixels image sensor. It can capture RGB color, 2D, and 3D simultaneously, enabling Pickit to process high-quality 3D point clouds. With Pickit’s 3D vision software, developers can easily set up the robot cell with a machine vision system and run calibration tools without minimal experience. Finally, the short cycle time targets were met using the fast acquisition time of the 3D camera.
ESSERT’s flexible robotic workstation with cutting-edge 3D vision solution opens up a new opportunity for pharmaceutical companies that need to handle challenging objects. Their automation solution will help the companies to meet the demand in the rapidly growing pharmaceutical market reliably.
Read the full customer story →
Are you interested in unlocking the superpowers of your pick-and-place robot? Ask your questions to our vision engineers by booking a meeting with them:
You May Also Like
These Related Stories
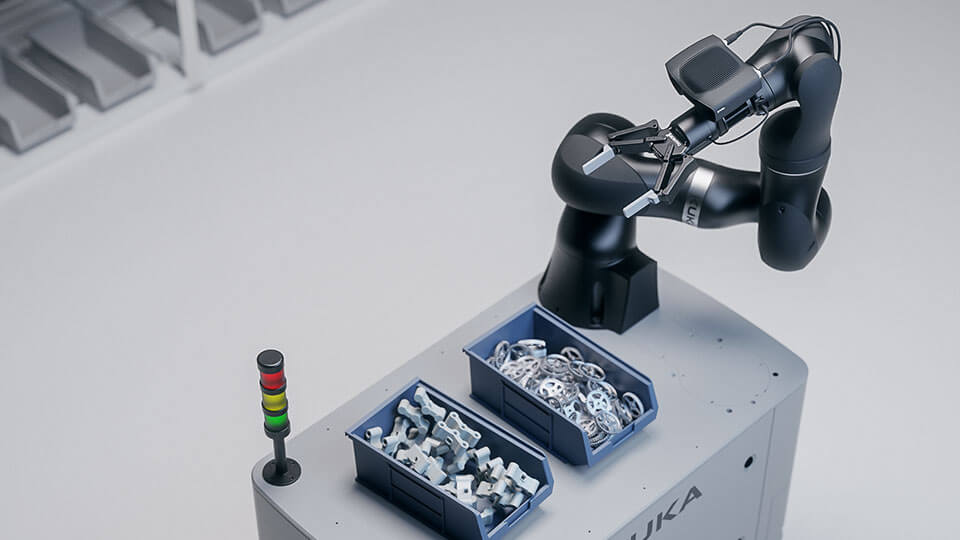
Solving the Top 3 Bin-Picking Challenges with Machine Vision
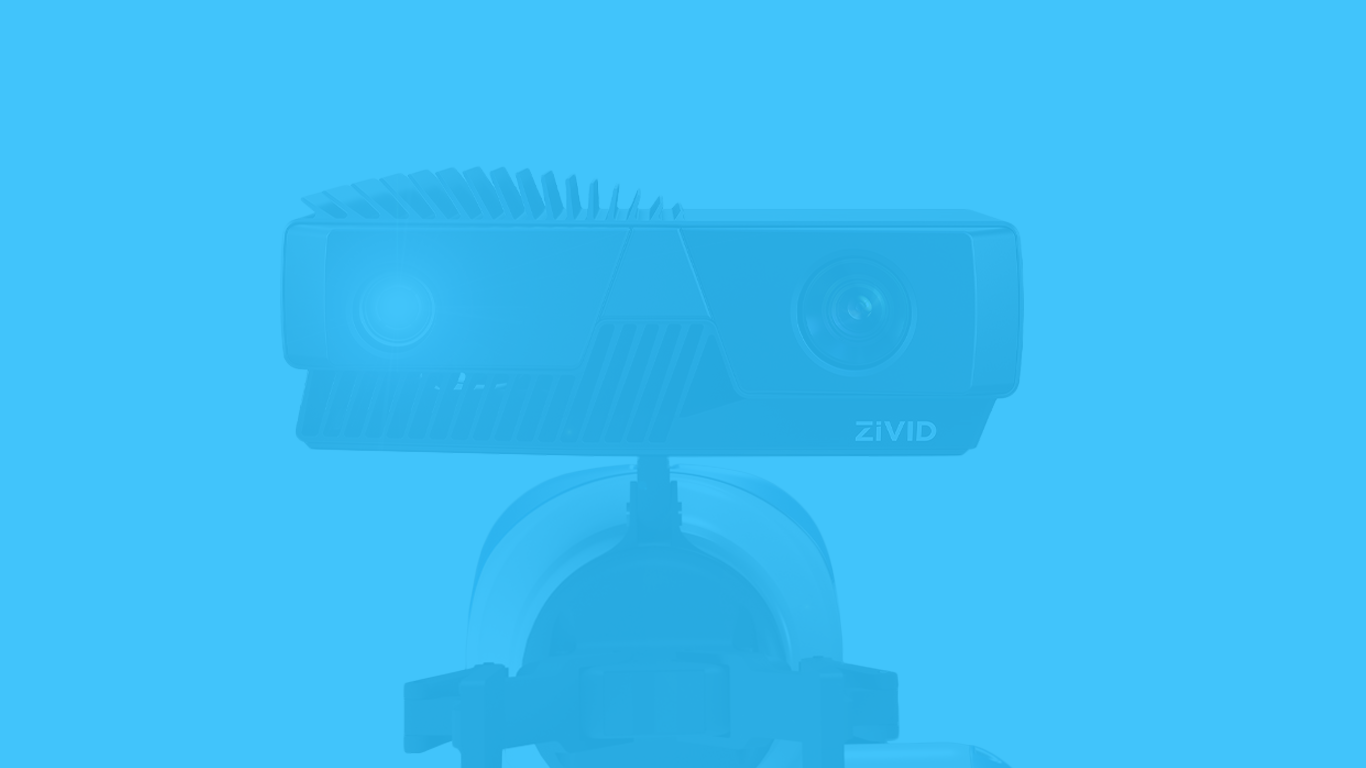
A beginner's guide to 3D machine vision cameras
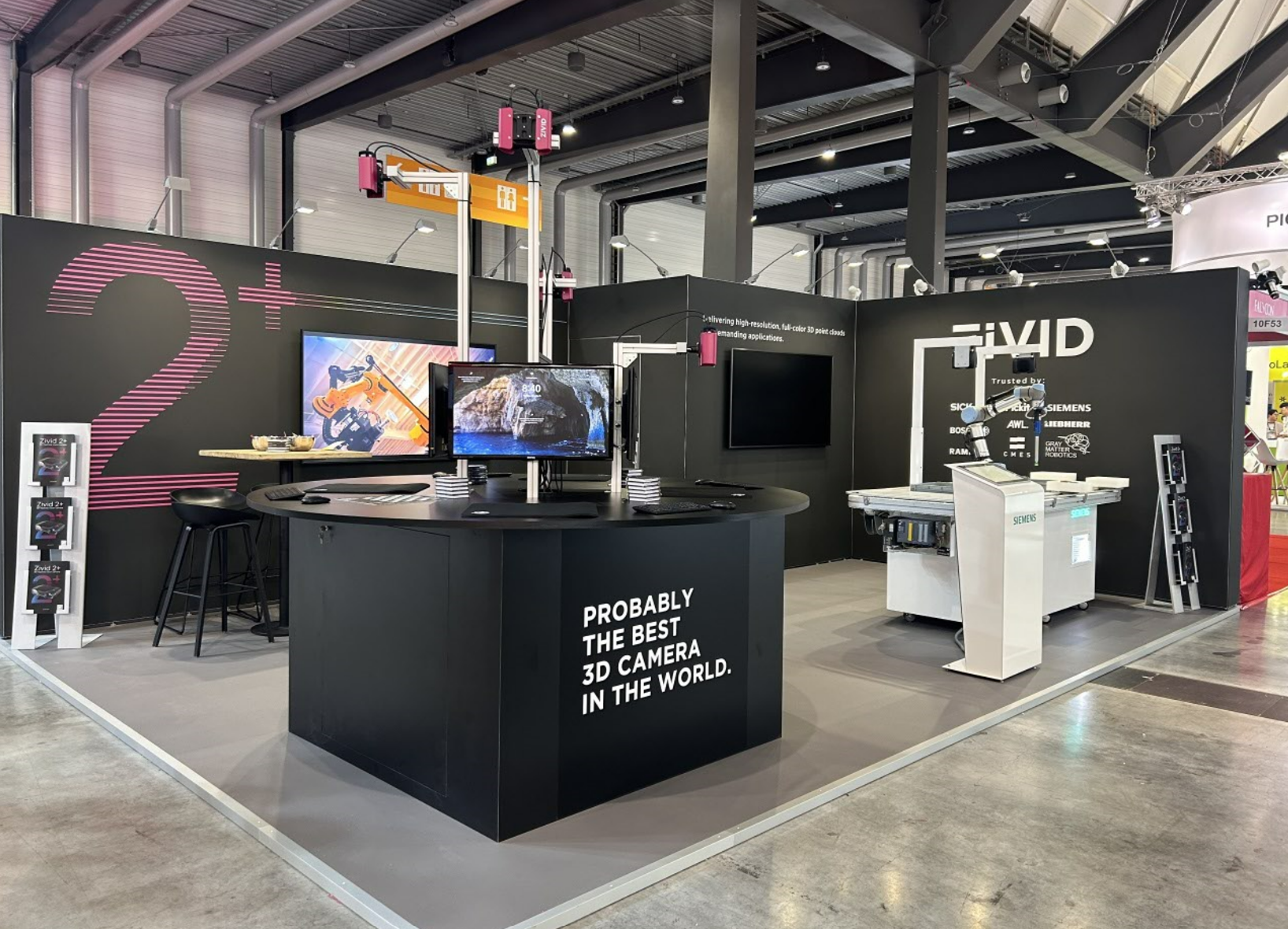