Why 3D machine vision is better than 2D
3D machine vision is one of the most exciting technological advancements in robotics. Many companies are turning to 3D vision because it offers a number of benefits over traditional 2D, including increased accuracy, speed, and flexibility. In this blog post, we will discuss how 3D vision works and why you should consider it for your application.
Get our latest eBook: Basics of 3D machine vision vs. 2D
The two-dimensional view
The fact that 2D machine vision systems have been deployed for a few decades now is a testament to their worth. 2D machine vision is a great tool for many applications, but it has some fundamental problems.
2D cameras only see the world in flat images. This means you can't inspect objects as they actually are or measure them as you would expect to be able to. It also means that your inspection software needs to apply complex algorithms and heuristics to try and guess what an object may look like from a single image. These assumptions often fail and lead to errors in your applications.
Since the target object image is formed from light reflected from it, variations in lighting in the field of view due to changes in ambient conditions or artificial lighting can have an adverse impact on accuracy. Too much light, too little light, or shadowing in the factory environment, can adversely affect the clarity of edges and features appearing in the 2D plane.
Lack of contrast poses a problem for 2D machine vision since it’s those clear contrasts (and thereby edges) in an object's surface that determine how well something can be picked out by cameras. For example, dark or shiny surfaces will not show up clearly and so they'll lack detail. Lack of contrast poses a problem.
Since we’re not handling any height information with 2D machine vision, errors due to target object movement in the Z-plane presents a further limitation. If the object was always sat on a perfectly flat surface at a precise focal distance from the image sensor, then it wouldn’t be an issue for imaging accuracy.
Want to learn more? Download our free eBook about the basics of 3D vs. 2D:
The beauty of three dimensions
Here is the important point about 3D. By virtue of being able to capture the extra third dimension data reliably, 3D machine vision systems are immune to the environmental factors adversely affecting 2D systems – the aspects of lighting, contrast, and distance to object discussed earlier are no longer an issue.
Yes, compared to two-dimensional image processing, working in 3D is indeed more time, processor and software-intensive, however rapid advances in multi-core processors, 3D algorithms and software tools mean that 3D machine vision systems are now more than capable of keeping up with production line throughput requirements.
As a result of this much-extended capability, 3D machine vision is being applied to a broad spectrum of tasks where 2D capability falls short, including among many:
- Thickness, height, and volume measurement
- Dimensioning and space management
- Measuring shapes, holes, angles, and curves
- Detection of surface or assembly defects
- Quality control and verification against 3D CAD models
- Robot guidance and surface tracking (e.g., for welding, gluing, deburring, and more)
- Bin picking for placing, packing, or assembly
- Object scanning and digitization
Random bin picking, in particular, is still regarded by many as a real acid test for machine vision systems and it’s not hard to understand why. The robot needs to choose one part and work out how best to grip it. But it also needs to take into account size differences between itself as well as various measurements. To do this, the robot needs to see the parts very clearly!
And if they are dark or light-absorbing, shiny, and reflective, it needs to handle the changing scene dynamics; the reflections, missing data, and inherent noise. This process has to happen fast and accurately, time and time again.
This is where 3D machine vision comes into its own. It’s the only way to be able to process all this information in real-time and with high precision, regardless of position or orientation of an item in the bin.
Learn more about the basics of 3D machine vision.
Important considerations
We are happy to give you this summary of the key differences between 2D and 3D. However, for you to truly unleash the potential of your vision-guided application, you are going to need to go deeper in your research.
- There are four main techniques for achieving 3D machine vision systems: laser triangulation; stereo vision; time-of-flight and structured light. Which one should you choose? Zivid cameras for example use structured light.
- What is a point cloud?
- Resolution, color, speed, and accuracy: what is the best for my application?
- 3D measurement principles employed behind the camera: are there pros and cons to consider?
Don't worry! We are here to help and we have put all the information in a free eBook, just for you:
We hope you enjoy it.
You May Also Like
These Related Stories
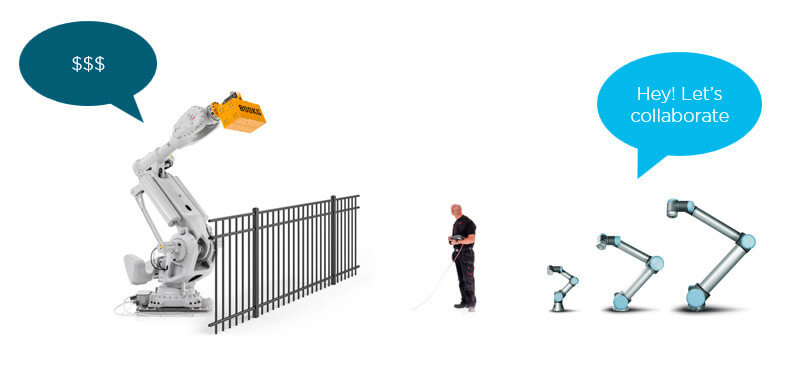
Collaborative 3D Cameras – Safe, Flexible, Precise and Easy to Use
-1.jpg?width=341&height=192&name=Zivid-Two-on-arm-robotics-3D-vision-color-camera%20(1)-1.jpg)
Zivid wins gold design innovators award for robot-mounted 3D camera
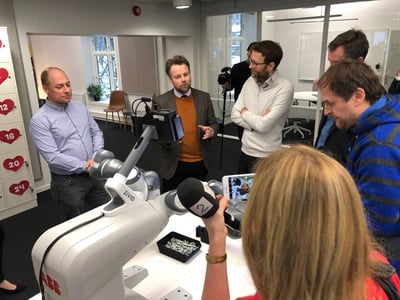