Robotic Wire and Arc Additive Manufacturing with 3D Vision
On-Demand Manufacturing will be vital in helping solve the supply chain issues, especially for welding and repair. Wire and Arc Additive Manufacturing WAAM can use various materials like Cobalt, Copper, Titanium, Iron, and Nickle to produce and build complex and large components on-site. Jake Hall, aka the Manufacturing Millennial, goes deeper into the subject in a Linkedin Live Webinar.
The welding industry is seeing some of the most innovative growth in the field of robotics. There is an industry need for metallic parts to be manufactured or repaired as needed to high-quality specifications. Additionally, the cost should be highly competitive and should be within the reach of just about any company.
Specifically for the repair (or overlay welding as it is also called) of metallic parts, there is the challenge of a global shortage of experienced welders and the demands for better productivity are also in play. Robotic welding techniques offer huge possibilities for consistent quality and increased ‘on-arc’ time that is not possible using human welders.
The relatively new field of additive manufacturing using Wire Arc Additive Manufacturing (WAAM) is a very exciting development for both manufacturing and repair of metallic parts. There is a need to reduce waste and energy consumption in manufacturing coupled with a desire to build and repair parts that it has just not been possible to do with traditional techniques.
WAAM outperforms conventional manufacturing approaches such as forging and casting in the following ways:
- Quality assurance: repeatable
- Create large objects: print objects of size only limited by the reach of the robot.
- More design freedom: WAAM allows the manufacture of very complex-shaped objects.
- Low start-up cost and TCO: WAAM is lower CAPEX cost than traditional forging and casting and other AM techniques.
- Hybrid manufacturing: WAAM is suited for use with complementary production methods.
- Waste reduction: Material is only deposited where needed leading to waste reductions of up to 50%.
Robotic welding company RAMLAB, based in Rotterdam, is focused on the development of this WAAM technology and specifically the MaxQ system to automate the monitoring and control of the welding process. In this world-renowned international port that is Rotterdam, there is indeed an initiative there to offer novel industrial services such as additive manufacturing (AM), or 3-D printing of massive boat parts.
For RAMLAB, the vision challenge was to find a 3D sensor strong enough for highly accurate arc welding processes that could also operate smoothly in a hot, dirty, and tough environment. The application also required a camera light and robust enough to be mounted on the arm of the robot. For those criteria, they chose the Zivid 2 industrial 3D color camera.
The MaxQ system from RAMLAB is a cutting-edge application that delivers unprecedented and new manufacturing and repair possibilities to a swathe of companies that did not have those opportunities previously. A combination of robot guidance expertise and Zivid’s best-in-class industrial 3D vision system means complex additives and welding can be sourced ‘on-demand’ at a reasonable cost.
In an exclusive round table, Linkedin influencer and manufacturing enthusiast Jake Hall, also known as the Manufacturing Millennial, Vincent Wegener, CEO and founder of RAMLAB, and Thomas Embla Bonnerud, CEO of Zivid, discuss the benefits of robot-guided WAAM coupled with 3D machine vision. Watch the replay here:
The webinar covers
- The growth of the Wire and Arc Additive Manufacturing (WAAM) industry
- The challenges of building complex and large components with a welding collaborative robot
- How RAMLAB's automated solution solved these challenges using Zivid 3D vision
Speakers
![]() |
![]() |
![]() |
Want to learn more? Read the case study.
You May Also Like
These Related Stories
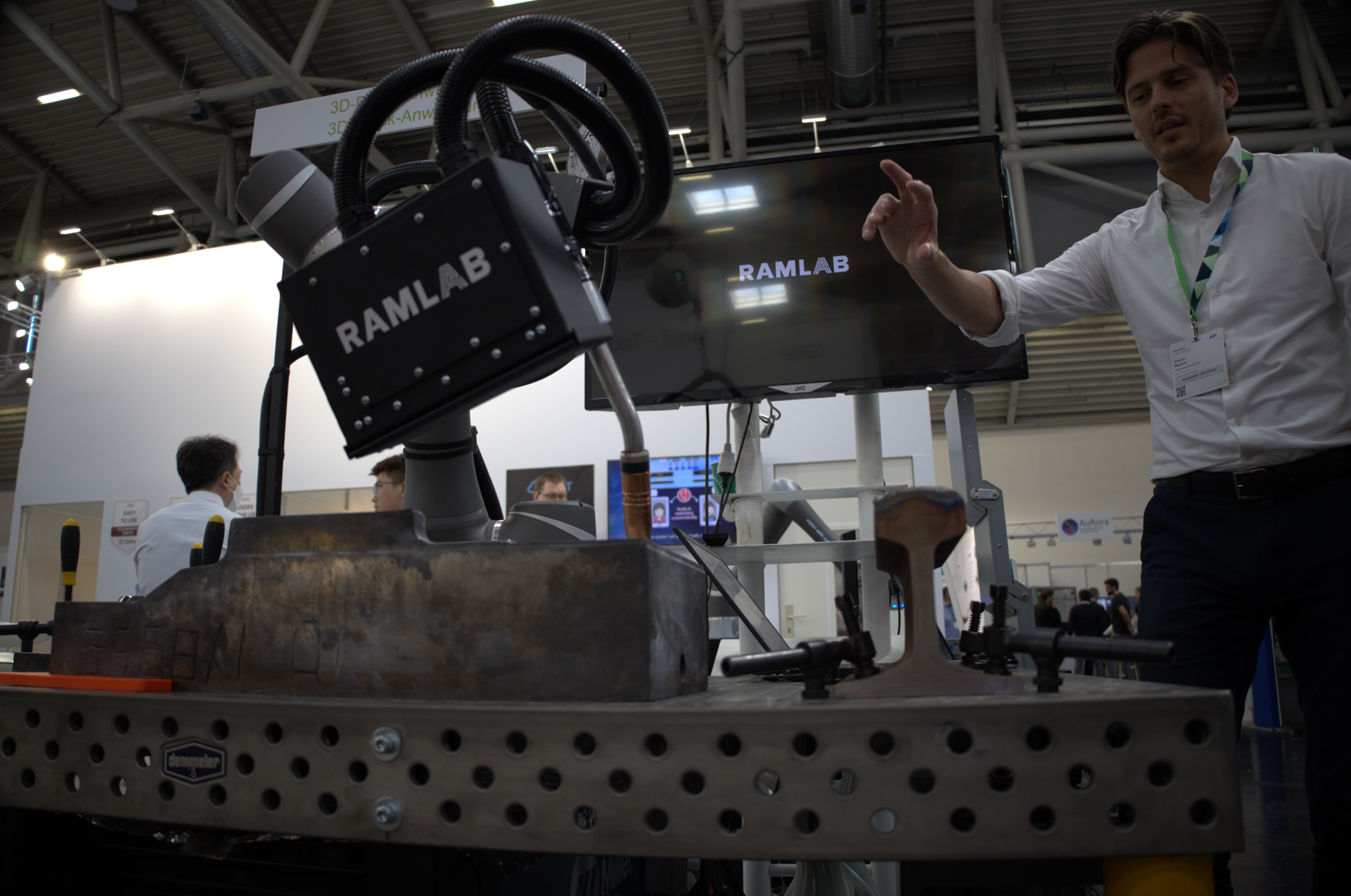
Choosing a 3D Camera for Collaborative Robotics Solutions
-1.jpg?width=341&height=192&name=Zivid-Two-on-arm-robotics-3D-vision-color-camera%20(1)-1.jpg)
Zivid wins gold design innovators award for robot-mounted 3D camera
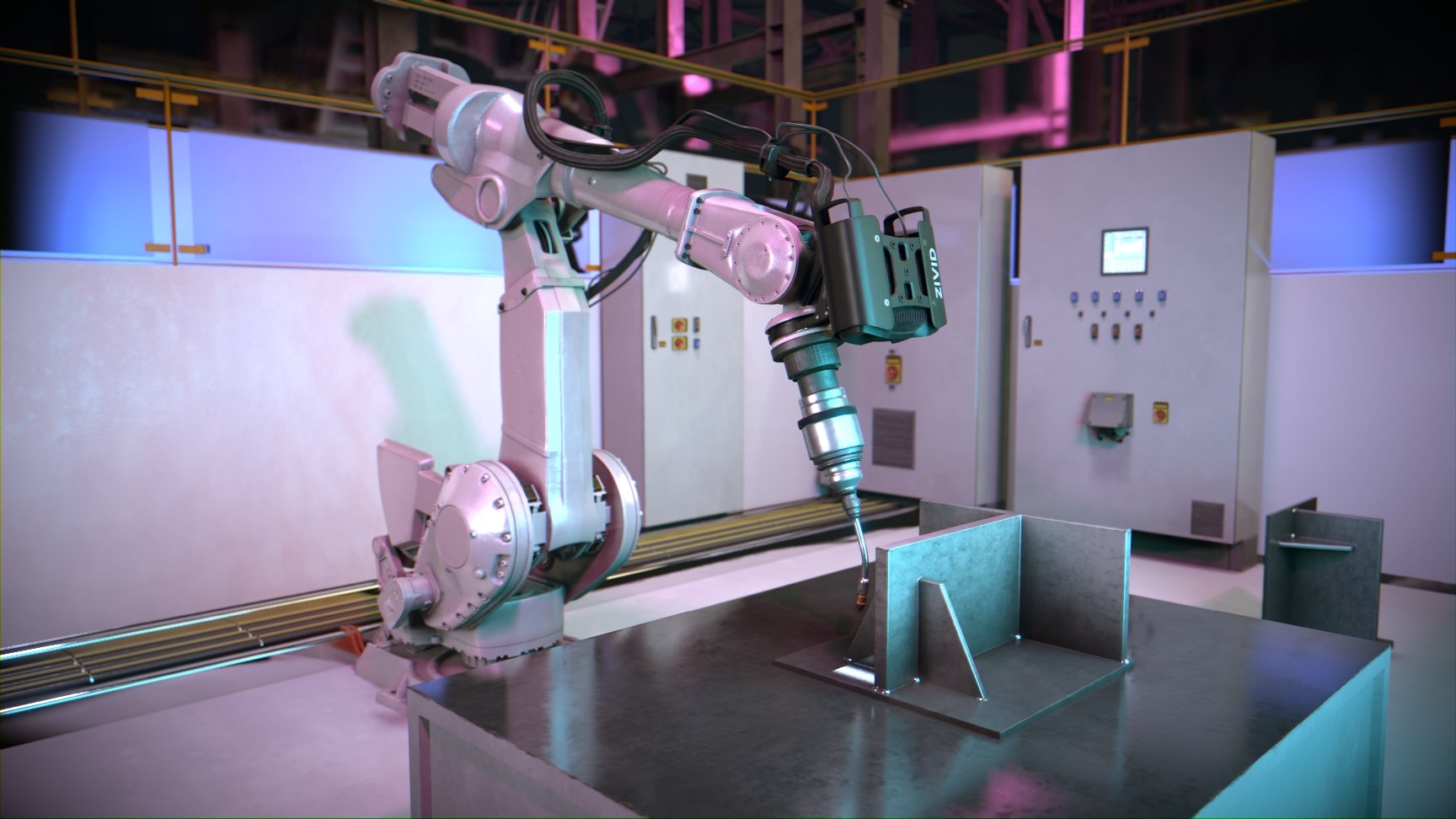