The Real Cost of Cheap Machine Vision: Hidden Risks of Low-End 3D Cameras
When it comes to automated picking, the choice of a 3D machine vision system can make or break your operation. Low-end cameras may seem budget-friendly, but their hidden costs—like mispicks, downtime, and damaged goods—can quickly outweigh the initial savings.
Table of contents
- Affordable Options and Their Limitations
- What Is Entitlement
- Main Causes of Robotic Mispicks
- Damaging Objects During Picking
- 3D Camera's Performance in Real Environments
- Is Your 3D Camera Able to Capture Everything?
- Crisp Detail with H-Res 2D
- Key Factors to Consider When Choosing a 3D Camera for Reliable Robotic Picking
Affordable Options and Their Limitations
Sophisticated 3D machine vision has developed at a furious pace over recent years. 3D cameras can perform to levels that could only be imagined five years ago. Along with advances in performance, such as point cloud quality and accuracy, the cost of these devices has fallen to a price point that makes them available to anybody. A quite reasonable 3D machine vision camera can be purchased for around 1000 USD or even less, which is quite remarkable.
Often, engineers and programmers will begin experimenting with 3D machine vision with cameras such as the Intel RealSense or, even earlier, the Microsoft Kinect. These cameras offer an easy and quick interface to get introduced to the most basic interactions with using stereo machine vision. Eventually though when you move on to more complicated tasks you might need better data.
And as with all things, you tend to get what you pay for and, conversely, don’t get what you don’t pay for.
Entitlement – The Right to See Everything
Entitlement is a term used in automated picking, describing the ability to see whatever is in the bin, and more importantly, the ability to generate a good selection of pick poses for the robot to grasp the objects in the bin.
The quality, and the completeness of the point cloud is a deciding factor in this process. While a low-cost 3D camera may give quite acceptable results on a manila envelope, it will start to struggle very quickly when presented with shiny parts and transparent objects.
If your system has a high level of entitlement, it indicates the cell’s ability to keep picking successfully without intervention. A picking cell that cannot pick all parts in the bin is more than just an inconvenience. It will require operator intervention that cannot be predicted. This can be a very costly situation and introduces delays in your facility.
A high-quality industrial 3D camera such as Zivid 2+ is meticulously designed to deliver highly accurate and complete point clouds across a wide range of objects and scenarios. This is one of the first steps in creating a high entitlement system - the quality vision system.
Main Causes of Robotic Mispicks
Poor entitlement can show in diverse ways but one of the key forms is mispicks. This can lead to picking multiple objects at a time, having a poor grasp on an object and dropping it, or just picking the entirely wrong object. Occasionally you might not pick the object at all, and then what happens?
Being able to prevent mispicks is one of the first steps to having a dependable picking cell. The choice of 3D camera will have a profound impact on your entitlement.
The first instance is the inability generate a good pick pose, which can leave the robot cell in a paused state. A low-end 3D camera may have substantial portions of missing data in the point cloud thus making the object unrecognisable. When faced with more challenging and shiny materials these 3D cameras have very little mitigation for artifacts and noise that are inherently present.
These artifacts can take almost any form and can obscure the object, making it unrecognisable or they can appear as real obstacles that the detection algorithms cannot discern as errors. In this scenario the robot’s motion planning sees an obstacle where non exists, and these can also lead to a stalled picking cell.
For many detection algorithms, 2D is employed. A low-resolution 3D camera will have a limited ability to discern features and edges. When some items are separated by a narrow gap, such as two boxes side by side the system’s algorithm may identify the two boxes as a single box. It may not be able to process this, or it may generate a pick pose that is likely located on the gap between the boxes. When the suction cup end effector tries to pick, there will not be a secure vacuum seal, and the pick either fails or works partially, and the item is dropped during robot motion.
Damaging Objects During Picking
Insufficient point cloud quality can also lead to damaged items during picking. Most piece-picking systems employ suction-type end effectors with an inherent amount of compliance. But this compliance has its limits and is typically a few millimeters or perhaps a couple of centimeters.
When a noisy, inferior-quality point cloud is used, the accuracy of the system suffers, and items are not where the point cloud says they are. This means when the end effector descends into the bin to pick the object it has a high chance of over, or under-shooting the target.
Often, there will be occasions where the error is within the end effector compliance limits. But when this is exceeded, especially on an overshoot, the full force of the robot pushes into the object. With any object that is rigid, this will almost certainly result in its damage.
What is most concerning in this situation is that the damage is unlikely to be detected. This can mean shipping broken or damaged products to customers or a jamming of the system downstream due to non-conformity of the item.
Check for 3D Camera's Performance in Real Environments.
One of the first things to plan is evaluation and testing in realistic conditions. 3D cameras are high-precision pieces of measurement instrumentation that are often measured in terms of micrometers.
Even small variations in surroundings, temperature, vibration, ambient light can have significant impact on performance as calibration drift sets in.
Most 3D cameras can offer satisfactory results in the lab where all variables can be controlled and kept optimal. But the lab is not where they will earn their living, they need to perform in warehouses and factories, so it is essential you evaluate them in these environments.
Is Your 3D Camera Able to Capture Everything?
A defining feature of a high-quality 3D camera is its ability to capture good data on items in various colors, surfaces, and lighting conditions. Lower-cost machine vision will have serious limitations here.
Their limited dynamic range requires them to either expose for the highlights or expose for the lowlights and lose data on the other. This results in large area of a scene having an absence of points, there simply isn’t any data to work with.
Zivid 3D cameras feature a patented HDR feature which enables a broad spectrum of light intensity to be captured. With HDR the 3D camera can reliably capture detailed, low-noise point clouds across just about anything that is presented to it.
Crisp Detail with H-Res 2D
2D imaging is one of primary means of detecting and categorizing objects in automated picking. Related algorithms use the definition of these images to make pick pose estimations.
When the edges and gaps between items are poorly defined, these algorithms can fail to recognize edges and gaps. As previously mentioned, two boxes aligned side by side, with several millimeters of spacing may appear as a single, larger box to the detection algorithm. In this event, the pick pose generated will likely aim for the center area directly on the gap.
When the vacuum cup tries to pick, it cannot make a good seal, and a mispick or dropped pick becomes highly likely. The high-resolution and low-noise images from a high-end camera should offer a millimeter-level definition or better.
Key Factors to Consider When Choosing a 3D Camera for Reliable Robotic Picking
There is a broad selection of 3D cameras and sensors on the market today. Ultimately the question comes down to: ‘How reliable and capable should my robotic picking cell be?’
The reliability and capability come down to three key criteria:
- The point cloud fidelity (in terms of accuracy, cleanliness, and completeness).
- Delivery of high-fidelity 2D images.
- Industrial design that allows for staying calibrated in harsh situations.
When you choose a high-quality 3D camera such as Zivid 2+, you have a single device that delivers superb 3D and 2D imaging from a single machine. It will be armed with a broad array of features and filters that ensure very high point cloud quality on almost any subject. That gives you confidence that your robot cell will function as you expect and deliver the results you need.
Lower end 3D cameras have their place and are certainly very good value for the money. However, their limitations will need to be considered. Some demanding applications, such as picking transparent and shiny items, will not work with any long-term degree of confidence.
At the end of the day, the few thousand dollars extra for high-quality machine vision is very likely money well invested compared to the very significant costs of dealing with a picking cell that fails regularly.
Want to learn more about the perfect camera for your piece-picking cell? Register for our new product launch!
You May Also Like
These Related Stories
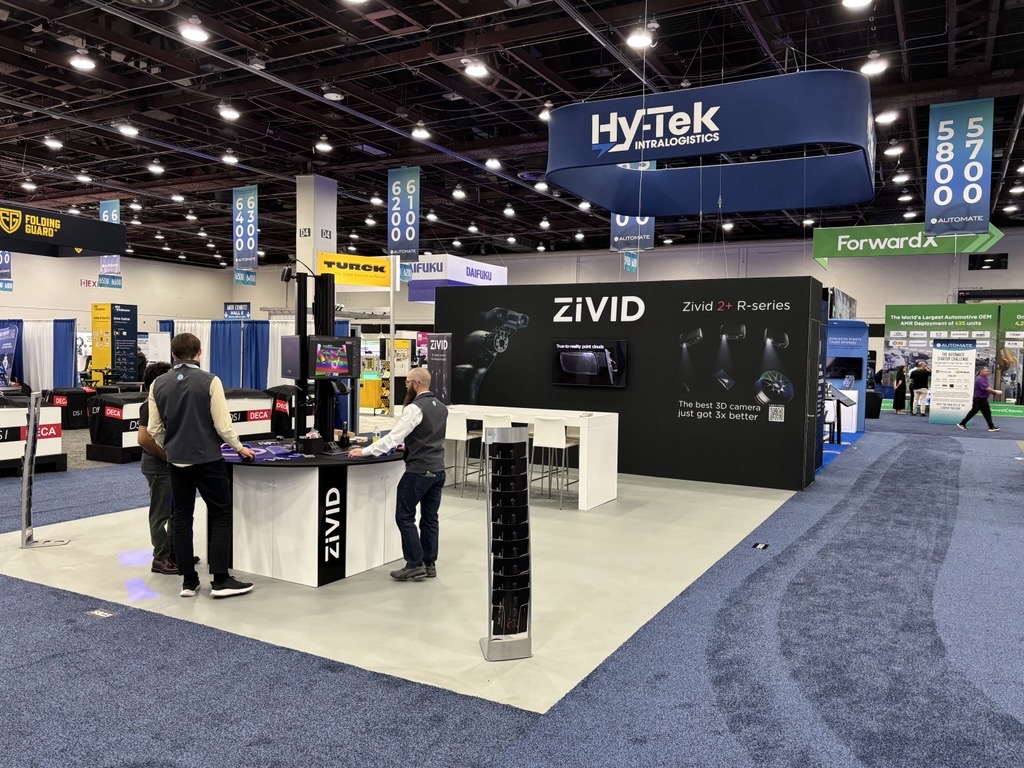
Highlights from Automate 2025 with Zivid 3D Vision Cameras
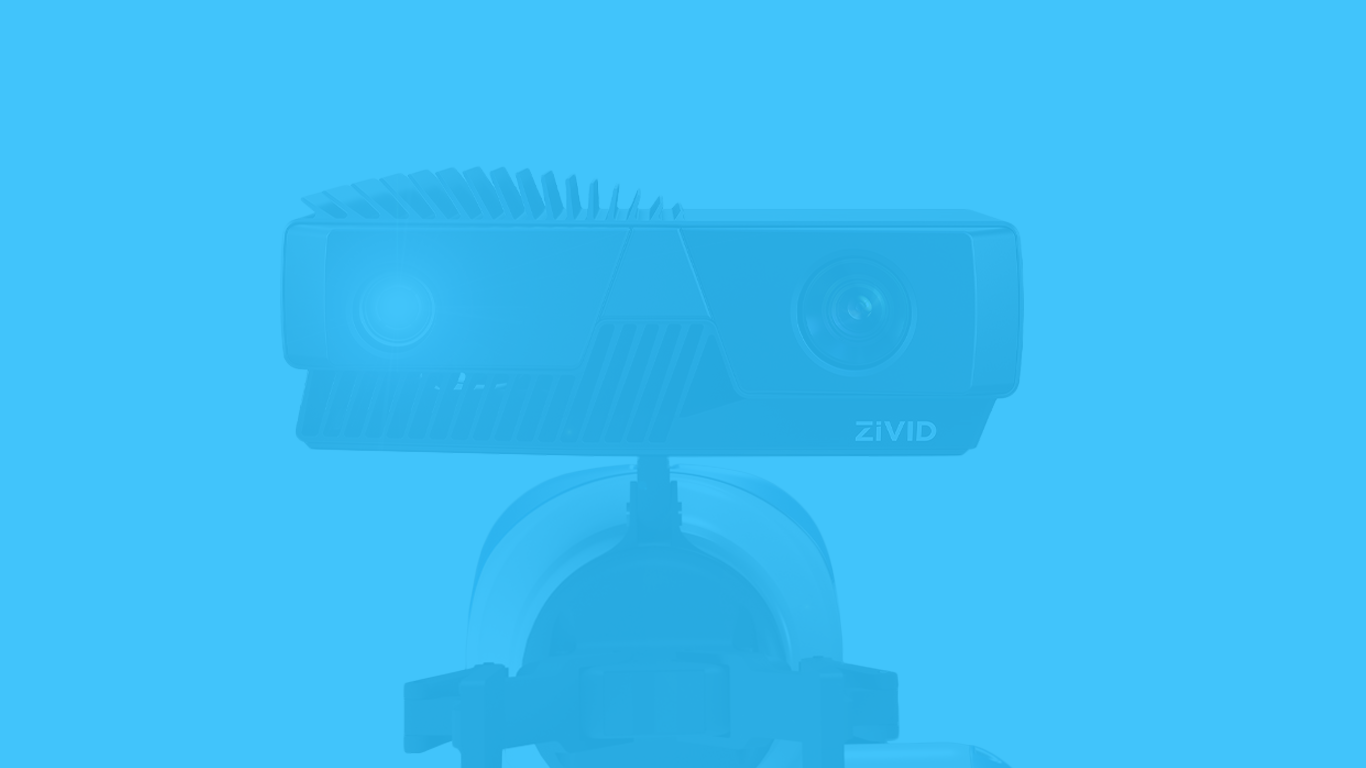
A beginner's guide to 3D machine vision cameras
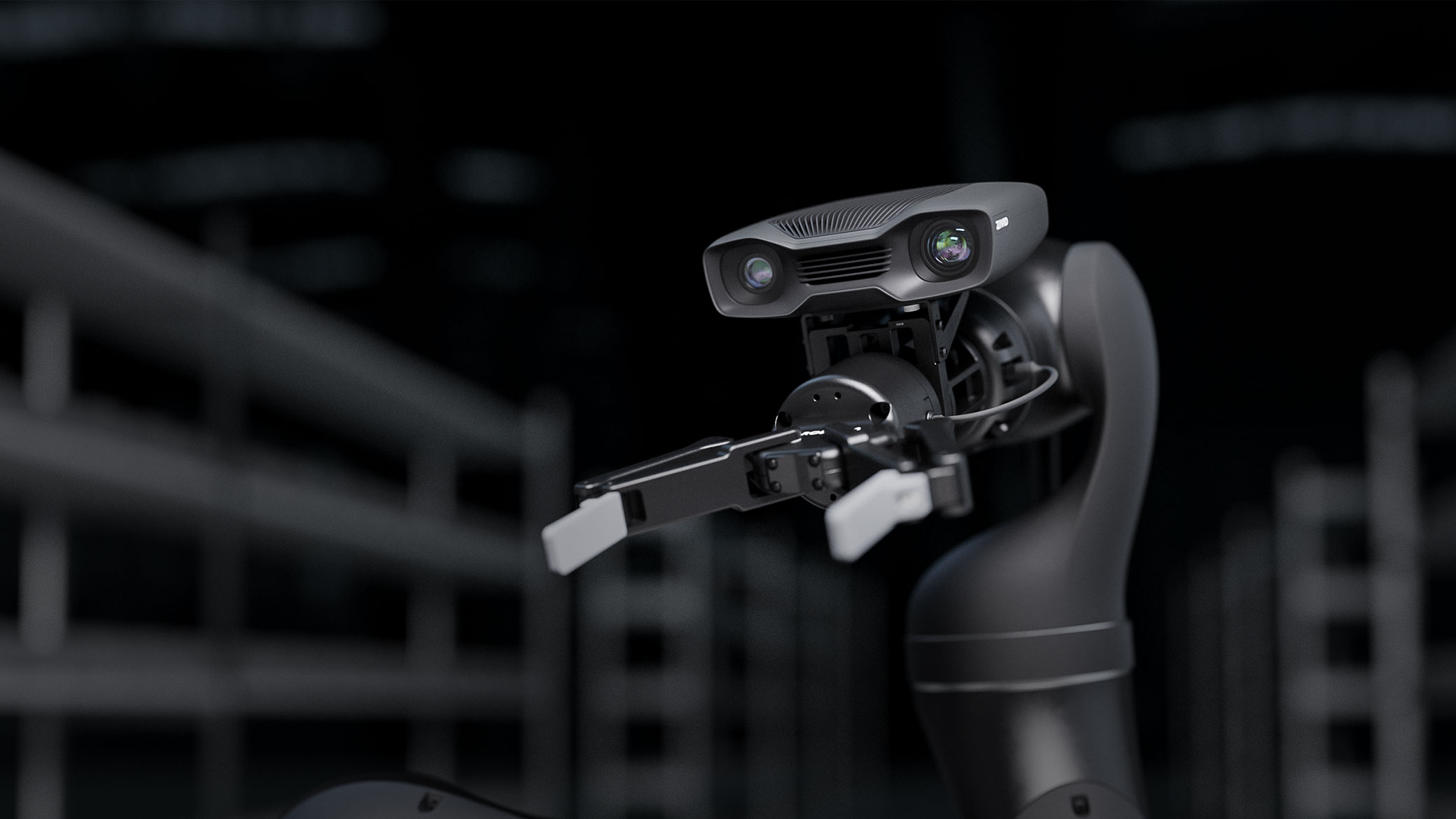