The best way to mount your 3D machine vision sensor
Today we'll focus on the question: is there a correct way to mount your 3D machine vision sensor?
There are obviously several ways to mount your 3D vision sensor, and we'll look at options for mounting when you want a robust robotic pick and place solution.
Stationary mounting is reasonably straightforward and probably most popular; however, a 3D camera on the robot arm itself can give you some additional benefits. At the end of this article, you can watch some industrial examples of both options.
The industrial Zivid One+ and Zivid Two 3D cameras support both robot cell configurations, so today, we'll consider options and decisions we need to make before we start implementing a 3D vision-based random bin-picking system.
You should perform a 3D hand-eye calibration independently of your final setup to achieve optimal detection, picking, and placing results.
We show you both why and how to achieve 3x better translation and 5x better rotational calibration in The practical guide to 3D hand-eye calibration and Understanding the importance of 3D hand-eye calibration.
Stationary mounting the 3D camera.
When using 3D and robots to pick randomly placed objects from bins, the most common setup is still to have the depth camera and vision system placed in a fixed position relative to the target. A fixed placement like this is typically above or to the side of the bin or tote housing the various objects we want our robot to pick.
Typical 3D sensors (stereo and laser included) have particular distances and areas they can cover while providing reliable data. Working range limitations mean that you need to consider the flexibility and requirements of your bin-picking solution.
With Zivid's 3D cameras, you benefit from both a flexible field of view (FOV) and a large and functional working distance. The result is that you'll have a platform capable of handling most SKUs, tasks, and working environments.
A pro tip is to mount the camera at a slight angle to the target bin (or objects). Check out the quick-start guide for more info.
Compared to a 2D sensor, depth cameras don't need a square or strict top down view or additional light sources. By mounting your 3D camera at a slight angle, you also help the structured light sensor to capture great point clouds without unnecessary reflections from the object and light source.
The stationary mounting considerations.
- A fixed 3D camera is in little or no conflict with the bin, gripper, or the robot arm.
- Once objects are picked and the gripper and robot arm is outside the FOV, the system can immediately capture and process new point clouds.
- Robot cycle times can be kept very short and is not so much dependent on waiting for the depth sensor.
- In some settings, the 3D camera can cover both the picking and the placing bins.
- Static camera mounts cover a single area, so unless you can securely place or drop picked objects or parts, it is advised to use 3D cameras also in the drop-off or placement area.
- Your vision algorithms still need to wait until the object, gripper, and robot arm is outside target FOV.
- A stationary mounted camera requires less effort when it comes to system cabling.
In the Zivid webshop, you can find a low-profile, flexible camera mount for easy installation on for example V-slot profiles.
On-arm mounting the 3D camera.
Another, more flexible option is to attach the 3D camera directly to the robot arm. In this configuration, the vision system moves together with the robot and the end-effector (tool or gripper).
You might have seen this setup already in inspection applications. A robot moves a relatively sizeable and costly vision sensor around an object to perform high-quality surface, volume, and metrology imaging. This is a very slow process, and not in the scope of bin-picking applications. In the opposite quadrant, we find popular and often low-cost depth cameras. Here we're looking at size- and weight attributes that are attractive for our on-arm robot mounting tasks.
However, these depth sensors (usually stereo vision cameras) give us a challenge we can't ignore. The low-cost option don't offer point cloud data suited to ensure high SKU coverage (thousands of products and colors) and reliable emptying of our bin. This is a critical requirement in universal, 3D vision-based picking applications.
You will find the best 3D machine vision solution for bin-picking in-between the high-end and expensive multi-camera sensors, and the lidar and low-cost stereo depth cameras.
These depth camera offerings also include the optimal 3D cameras for on-arm robot mounting. For example, you can use Zivid's industrial 3D cameras and benefit from both an optimized baseline, small footprint, and blazing fast high-quality 3D imaging.
The outcome of your choice dictates if your 3D vision platform is future proof and usable in different tasks and environments. Applications that benefit from on-arm 3D sensors are machine tending in manufacturing and piece picking order fulfillment in logistics.
The on-arm robot mounting considerations.
- Capture data from multiple positions. 3D cameras mounted on the robot arm give you the option to capture the target area (bins, totes etc.) from various angles and always get the best point cloud quality and coverage.
- You can stitch multiple 3D captures if you need even higher resolution point clouds.
- You only need a single depth sensor to cover both the pick and place locations.
- Cycle time requirements. Faster 3D sensors make it possible to reduce the time performing stop-capture-move and keep cycle time low.
- Compared to a stationary mounted 3D camera, the on-arm mounting option requires more path planning and robot guiding.
- The size and weight of the 3D sensors can reduce the maneuverability and payload of your robot. If you have a collaborative robot, the weight is much more important to consider than for the more powerful industrial robots.
- Consider the speed and acceleration of your robot arm. You want an industrial depth sensor with IP and shock rating.
- On-arm mounting requires more advanced cabling.
In the Zivid webshop, you can find a low-profile, on-arm robot mount and extender for easy installation on for example Universal Robots, Omron/TM etc.
So what is the verdict on on-arm robot vs. stationary 3D camera mounting?
As we have seen, there are pros and cons with both stationary and on-arm robot mounting of your depth sensor. And in some sense our promise of picking the best 3D camera mounting option is still open.
But, no matter which option you go for; the robust, industrial Zivid 3D camera is designed to be lightweight, small, and fast to minimize the impact on robot maneuverability and payload.
The high-quality and color point cloud data output gives your AI, machine learning, and detection algorithms the best possible view of reality, ensuring that whatever mounting option we choose, our bin-picking solution can cover more SKUs, reduce mispicks, and empty the whole bin.
To make it easy to select your FOV, working distance, size, speed and other requirements, you can visit our 3D camera product selector here.
You May Also Like
These Related Stories
The new 3D vision tools enabling bin-picking automation
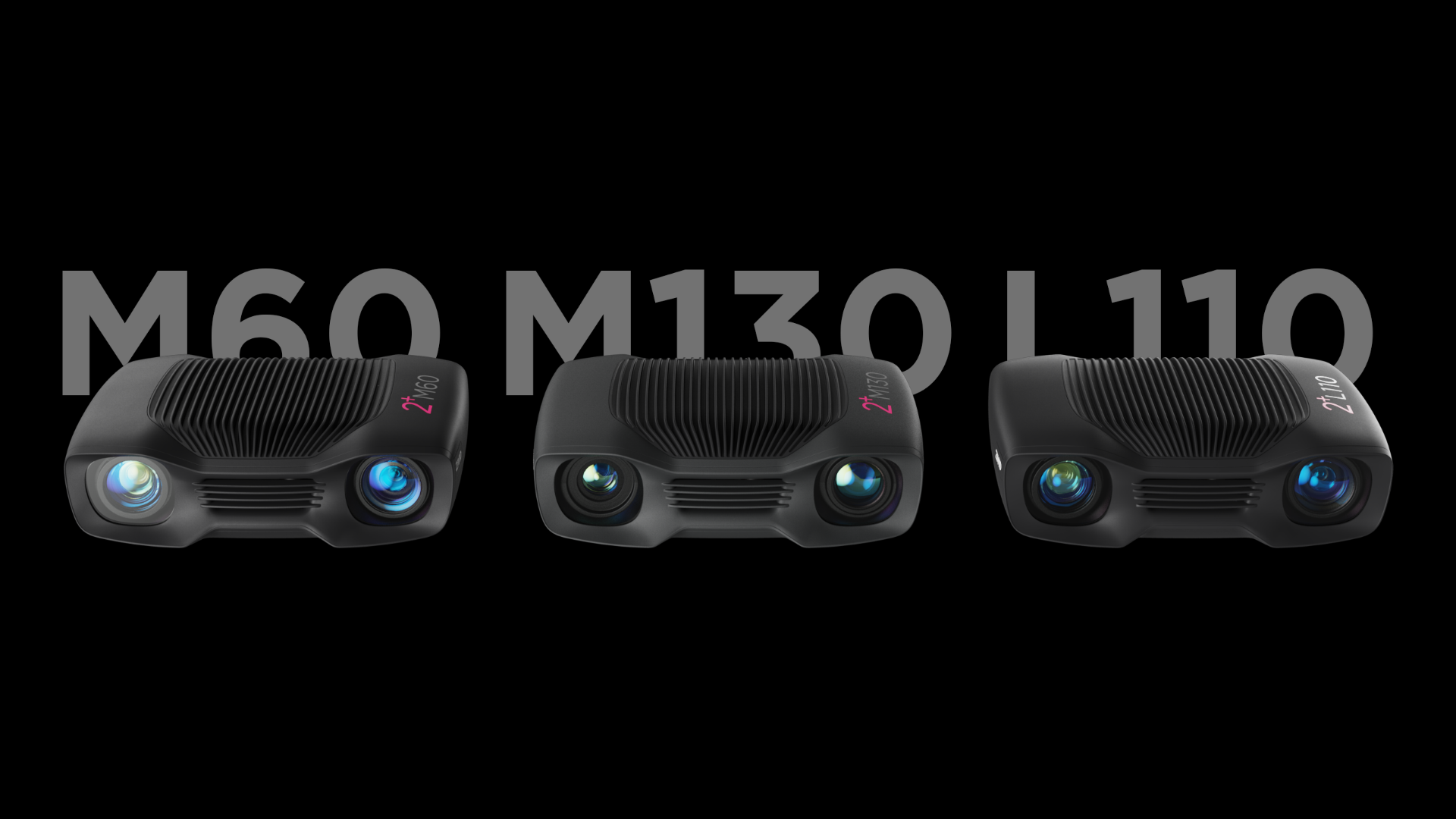
Solving Picking Challenges with Zivid 2+ 3D Vision
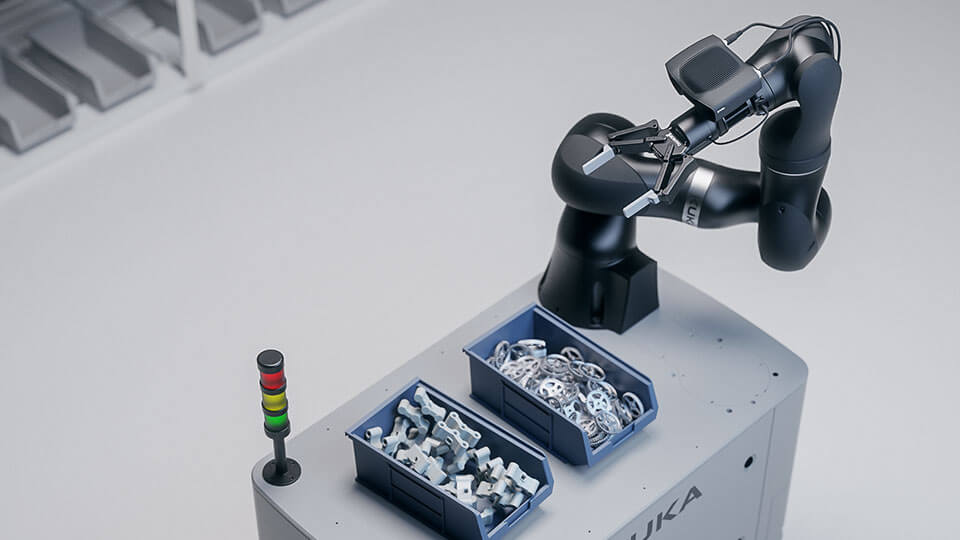