How this New Architecture will Revolutionize ROI for Robotic Systems
Last week, I had the pleasure of hosting a webinar on 3D machine vision and on-arm mounting, which is now available on-demand.
To elaborate on that discussion, we will now go deeper and discuss the quantifiable ROI of robot automation and specific sensor mounting approaches.
The Consensus is Clear: Let’s Automate!
In most cases, there is no need to argue the ROI for automating some tasks in warehouses and factories. The benefits are well understood:
- Increased productivity
- Increased quality
- Free up laborers to add value somewhere else in the business
Through an operational and quality cost lens, the financial benefit of automating a cell typically looks like this:
There is an initial investment in automating the task (green point in 2021), but the benefits are realized in subsequent years, hence the lower cumulative cost through 2025. Many automation projects “break-even” in the 2nd year after investment. (Note: “Manual costs” include labor costs, employee turnover, quality yield loss, and cost of returned goods and lost customers).
Veo Robotics, a leader in collaborative robot safety solutions, has recently published an article on how automation adds manufacturing flexibility and lowers unit costs. In this case, the ROI is showing cost as a function of production quantity.
Each ROI calculation depends largely on the market and application, so we will not dive into the assumptions and details in this article. However, I think we can all agree that automation is a beautiful thing and is revolutionizing more than just its birthplace of automotive factories.
What’s Next?
Most organizations have moved on to deeper questions now:
- What about AI?
- How can robots collaborate with humans more effectively and safely?
- Which new sensor technologies should be integrated to add more value and “future proof” the factory and business?
Some of the latest advancements are borderline science fiction, such as robots learning to identify objects and to manipulate them (the “Dactyl” robot solving the Rubik’s cube with a human-like hand).
Within the realm of sensors, machine vision is one capability that is exponentially growing and offering new, unprecedented opportunities also. Yes, the industry is well versed in 2D vision (line scanners, defect detection, and more), but 3D vision is still emerging and venturing into unchartered territories.
Sensor Mounting Architecture – One Powerful Decision that Affects ROI
Although not as sexy as “Artificial Intelligence” or “Machine Learning”, some new capabilities are just as valuable (and probably more practical). The sensor mounting architecture is a perfect example of this and is the focus of the remaining sections.
When designing a robot cell with 3D vision, there are two options for mounting the sensors:
- Stationary, or fixed to a structural rig (left/center in image below)
- “On-arm” (right-hand side in image below)
The mounting architecture affects number of sensors, workspace flexibility and space utilization, and image quality. Most importantly, this all translates to the application lifetime cost and the automation reliability.
Historically, the industry has favored stationary sensors. The reasons for this included:
- Sensors were large/bulky - Not ideal for robot arms, maneuverability, and bin picking
- Image capture time was too slow - Mounting on-arm penalized cycle time
- Sensors were not robust enough - Architects defaulted to stationary mounting
The Shortcomings of Stationary Mounting
While stationary mounting simplified the system integration, it negatively affected other aspects:
- Deployment of multiple sensors to see the entire workspace (higher BOM and maintenance)
- Average image quality because of a fixed view
- Failures during the more challenging pick scenarios (edge of bin, shiny objects, etc.)
Bottom line: Integrators and OEMs are out there right now failing pick-and-place tests because of imaging challenges like reflections and occlusions. Even worse, the burden of maintaining and servicing multiple sensors is being passed onto the factories and plant managers.
Luckily the world has changed and on-arm mounting is now a viable alternative to address these shortcomings. We are no longer forced into sub-par vision and maintaining 2x-4x the number of sensors that were needed, which was the case with stationary mounting.
Why On-arm Mounting Increases ROI
On-arm mounting brings new benefits to the factory. The table below compares the new on-arm alternative to stationary mounting:
As we know, there is no “perfect” solution that solves every system problem. It always depends on the application and goals, and there are always tradeoffs (this will likely haunt us forever). But we can clearly see the benefits of on-arm mounting.
Don’t just take our word for it. One of our lead partners, Kolektor Digital, an industry leader with 60 years-experience in industrial manufacturing experience, took on the challenge of building a solution that was integrated, collaborative, fast, and reliable.
Because we wanted to offer customers a fully-integrated, out-of-the-box robot worker, our aim was always to mount the machine vision camera on the robot arm. This of course had implications for the choice of camera. Too heavy and it would limit gripper payload. We had to maximize payload and reach. - Jure Skrabar, Senior Researcher of Optical Metrology at Kolektor Digital
With improved reliability and reduced number of sensors, the new cost of a robot cell can look like the green line below.
(pph = picks per hour)
The only remaining question is… Which 3D sensor to choose?
Zivid 2 – A Human-Like 3D Camera that Can Do Both
This is where Zivid comes into play and assists by providing versatile human-like vision for robots. The overall system solution is only as good as the supplier toolbox, and Zivid hopes to reinvent that toolbox.
Specifically, the Zivid 2 3D camera is redefining the boundaries that we outlined above.
- Large and bulky sensors – Zivid 2 is 940g and can fit in your hand
- Image capture time was slow – Zivid 2 captures 2.3Mp point clouds in < 80 ms.
- Not robust enough – Each Zivid camera is tested across shock, vibration, and temperature in an on-arm mounted system.
It is time to reimagine what is possible – Choose a flexible, high-quality camera that is designed for stationary and on-arm!
Explore More
If you find this topic interesting and want to learn more, there are several resources to keep exploring.
Our webinar from the Vision Systems Tech Summit is available on-demand and there is a new e-book that details the design considerations for on-arm mounting.
Keep innovating!
You May Also Like
These Related Stories
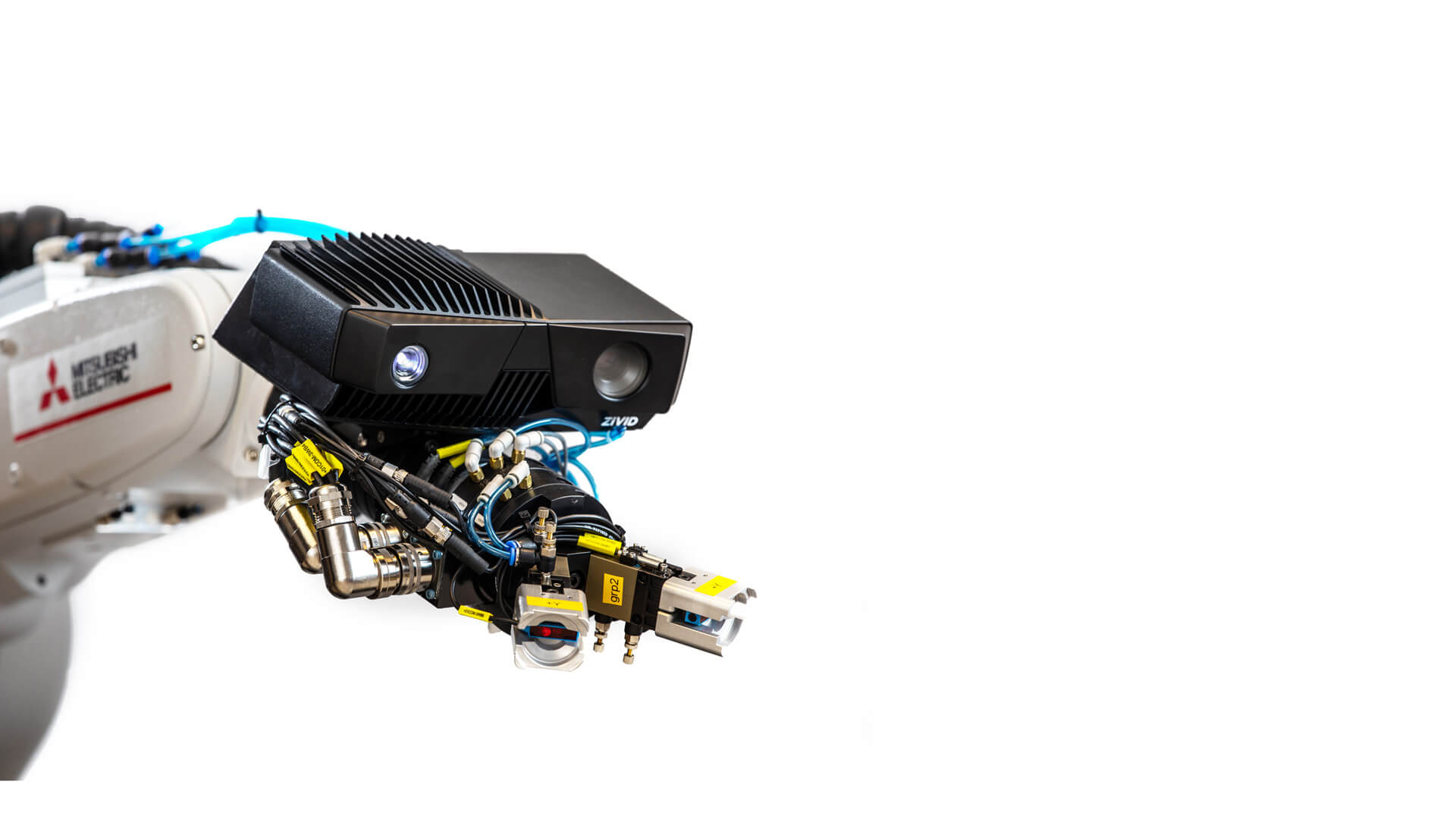
Why robot-mounted is the future of 3D machine vision
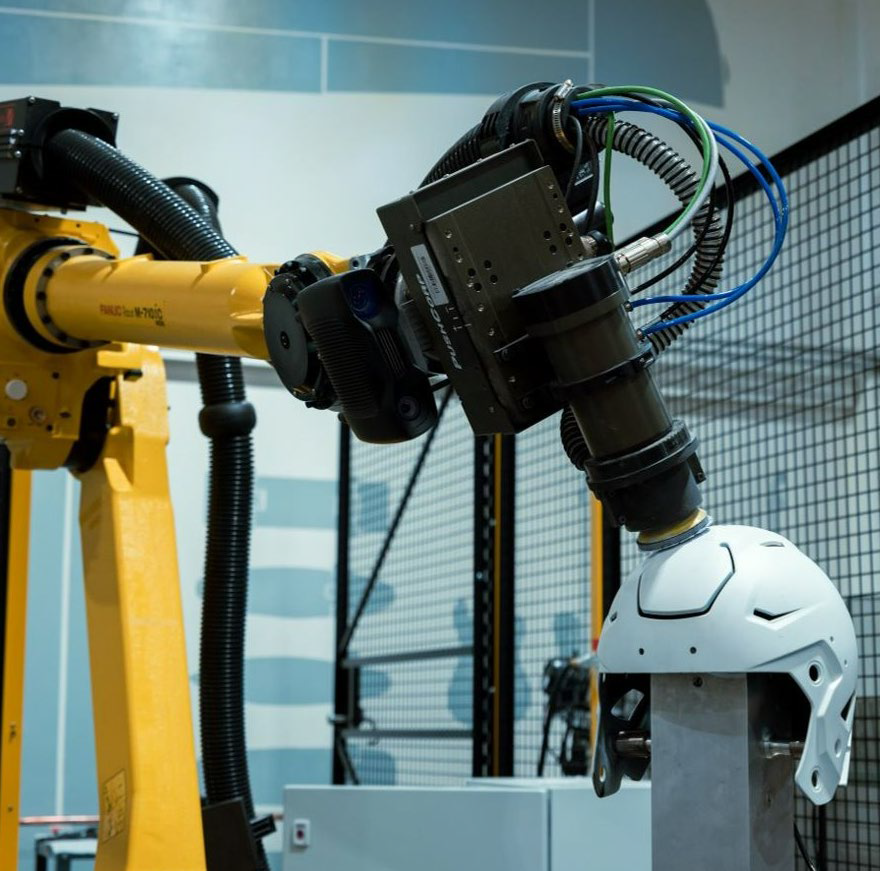
Streamlining Surface Finishing with Robotic Automation
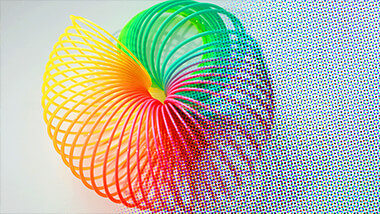