Robotic piece picking (also known as order picking) is part of automated order management used in warehouse logistics. In typical scenarios, items are picked individually from a container to another location, rather by a case or pallet, using a collaborative robot or fully automated system.
The demand for robotic piece picking increases among international e-commerce companies that need to operate 24/7 continuously. With successful order picking implementation, the companies can achieve productivity improvements and order accuracy with lower costs.
However, the simple operation that is easy for humans, like detecting objects, picking, and placing them correctly, is still a challenge for robots.
Last year only, Amazon hired more than 400,000 more workers to handle online orders that are not fully automated. It indicates that there are some challenges with existing piece picking solutions. This article covers four typical challenges with robotic piece picking and how to solve them with cutting-edge 3D vision technologies.
Challenge 1. Tiny, densely stacked, or randomly arranged objects
Detecting and picking unknown SKUs of various shapes, sizes, and materials is still one of the biggest problems in logistics. Unpickable objects go under terms like “uglies” or “pathologicals”.
In piece picking, robots are often required to handle tiny, thin, porous, deformable, or highly irregular objects densely stacked with a little gap or piled on top of each other. It causes wide baseline cameras, often used in order picking, to miss smaller objects hidden shadows of other objects or the container. Such occlusion issues may result in lower accuracy and an increasing number of mispicks.
Zivid 3D cameras are designed for covering typical order picking objects in industrial automation environments. The cameras have a small baseline making it easier to distinguish features smaller than 5mm, with minimal occlusion. Its powerful 2.3 MPixels image sensor ensures reliable object recognition and separation of boundaries even for very tiny and thin objects.
Point cloud example with Zivid Two 3D camera (View in 3D)
Challenge 2. Shiny, reflective, and plastic-wrapped objects
Handling shiny, reflective, and plastic-wrapped objects are common challenges in machine vision applications. They can cause point cloud artifacts and negatively affect the robot’s ability to detect, pick, and place items correctly. For example, artifacts like inter-reflections can lead to a heavily distorted point cloud with floating groups of points, “ghost planes,” and a seemingly random scatter of noisy points.
Over the years, Zivid has developed unique machine vision technologies like 3D HDR and Artifact Reduction Technology (ART) to ensure excellent suppression of imaging artifacts from reflections, interreflections, specular highlights, and high transitions.
ART includes a reflection removal filter called ContrastDistortion, which improves the 3D image quality from primary underlying error sources. With Zivid 3D cameras, users can also benefit from the Stripe engine, which adds optimal patterns for capturing point clouds of shiny or reflective objects to see an immediate improvement in image quality.
Point cloud example with Zivid Two 3D camera (View in 3D)
Challenge 3. Pick and Place Requirements
Capturing a broad range of objects is essential in piece picking scenarios where there is usually a mix of objects in a bin. It requires a machine vision system to recognize objects with similar shapes, colors, and material fast, and separate them for proper and place operations.
There are many 2D or low-cost 3D vision cameras that are not necessarily optimized for order picking applications. Robots might be able to detect objects with such a solution, but they cannot pick them every time due to scaling, rotation, or translation errors.
Zivid 3D cameras ensure that robots can detect, pick, and place objects faster than typical stereo 3D cameras used in piece picking today. With Zivid 3D, robots can capture typical piece picking objects <100ms for low to medium dynamic range and < 300 ms for high dynamic range scenes, including shiny and dark absorptive.
The unique combination of native color and high dynamic range enables a wide object coverage, including ceramic, metal, cardboard, and wood with a low occlusion. The Zivid cameras are also designed to work with all kinds of grippers (suction, vacuum, fingers stiff/compliant, soft) and meet strict dropping requirements.
Challenge 4. See transparent and semi-transparent
Transparent materials are prevalent in e-commerce packaging. Some items are themselves transparent or semi-transparent, but a significant number of items are enclosed in some form of transparent materials such as poly bags, bubble-wrap, and shrink-wrap.
Transparency has long been considered the ultimate challenge in 3D imaging. If you look at an object inside a polybag you will see various surfaces, the surface of the bag, the surface of the object, and even the surface of the bag of the bag.
These multiple reflective surfaces are the source of the challenge. In the field of stereoscopic 3D imaging, the essence of creating a detailed three-dimensional map lies in the ability to find corresponding points between multiple images. This task, however, presents significant challenges in certain scenarios, particularly when dealing with surfaces lacking distinct visual features.
Zivid takes the place as the first 3D industrial camera to provide accurate and pickable data on transparent and translucent surfaces with the Zivid Omni-engine. Being able to truly image transparent items is what allows robots equipped with Zivid's technology to excel in environments where such items are prevalent, such as eCommerce or Logistics.
Despite different use cases, the goal is the same for piece picking. Customers want automation that allows flexible picking solutions with high-accuracy, reliability, and speed. It is crucial to choose the right machine vision system to meet the business requirements by testing all the piece picking scenarios addressed above.
Zivid is a pure-play company specialized in 3D machine vision. Its focus is to provide hardware and software solutions for easy 3D application development in the world of automation.
To find out more about solving piece picking challanges with 3D machine vision, you can go to our application page or download the eBook!
Key topics explored in this eBook:
- Understanding the Fundamentals of Piece Picking
- Benefits of 3D Vision in Piece Picking
- Integration Challenges and Solutions
- Real-world Case Studies
- Key Zivid Features for Success
You May Also Like
These Related Stories
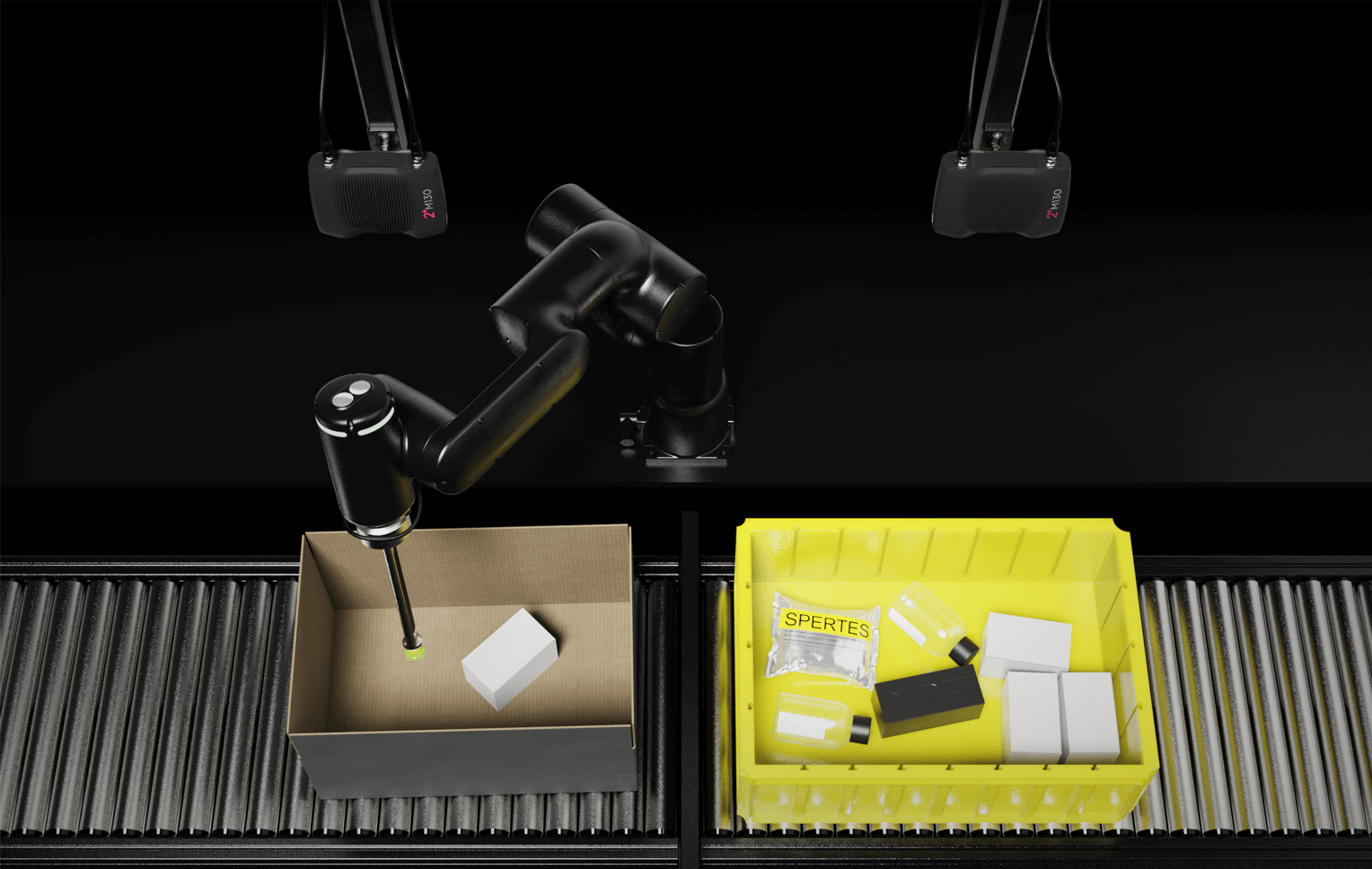
Unlocking transparency with Zivid 2+ for reliable piece-picking
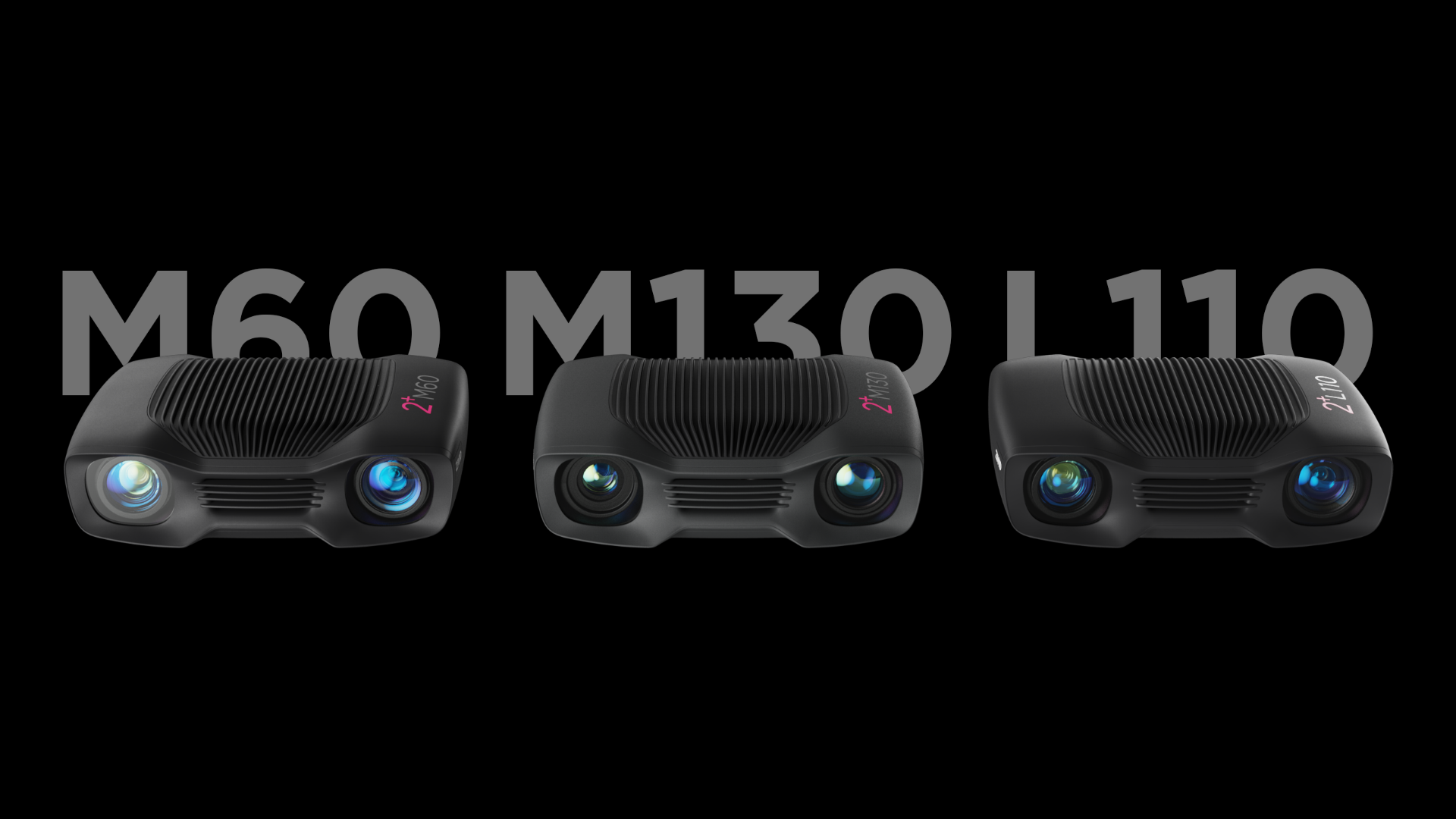
Solving Picking Challenges with Zivid 2+ 3D Vision
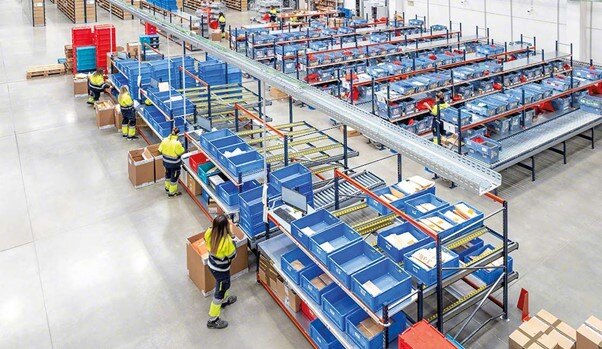